Compare your metrics to OSHA’s leading & lagging indicators
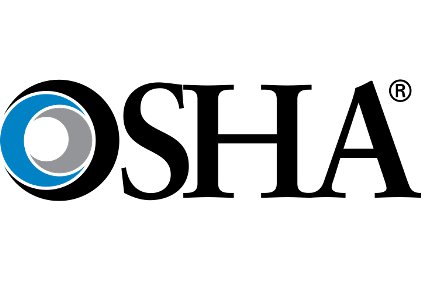
Everyone these days is talking about performance indicators for workplace safety. It’s widely understood that if you only measure injuries and follow OSHA injury/illness recordkeeping requirements you have a large blindspot in truly assessing how you safety processes are working, or not working.
OSHA has its own set of measures. They were devised for the Labor Department’s 2011-2016 Strategic Plan. With tweaking, some of these metrics could be applied to an organization. Specifically, OSHA uses these performance measures:
• decrease the fatality rate for the four leading causes of workplace death – falls, electrocutions, caught in or between and struck by for construction and general industry;
• number of hazards abated associated with hearing loss in construction and manufacturing;
• number of hazards abated associated with illnesses in general industry and construction;
• number of hazards abated associated with workplace amputations;
• number of employees removed from workplace hazards through inspections;
• federal agency total case rate for injuries and illnesses;
• federal agency lost time case rate for injuries and illnesses;
• percentage of serious, willful and repeat violations in high hazard manufacturing and large construction projects; and
• recidivism rate for serious, willful and repeat violations in high-hazard industries.
As you can see, OSHA uses a “dashboard” of leading and lagging indicators. “Hazards abated” prior to injuries is a leading indicator. “Total case rate for injuries and illnesses” and for lost-time cases are lagging indicators – measuring what has already happened.
As in a business, top management, in OSHA’s case the Labor Secretary’s office, sets general “Outcome Goals.” In the strategic plan, one such goal is to ensure worker voice in the workplace. OSHA then decides how to measure its performance in meeting this objective.
So the agency sets its own goals to support the larger Department of Labor goals. For instance, in FY 2012, OSHA said it would strive to respond to 95% of worker complaints within one working day, or to initiate an on-site inspection within five working days. OSHA also declared it would dedicate enforcement resources toward opening an inspection in 98% of fatality cases within one working day of notification.
How did the agency perform?
According to data in the FY 2013 Congressional Budget Justification for OSHA (a 136-page document) the agency responded to fatalities and catastrophes in 97% of the cases (goal was 95%) within one business day. OSHA’s compliance officers responded to 94% of non-formal complaints by initiating an inquiry within one working day and initiating an onsite inspection within five working days of formal complaints (goal was 98%).
Looking for a reprint of this article?
From high-res PDFs to custom plaques, order your copy today!