Cintas issues top five safety resolutions for 2012
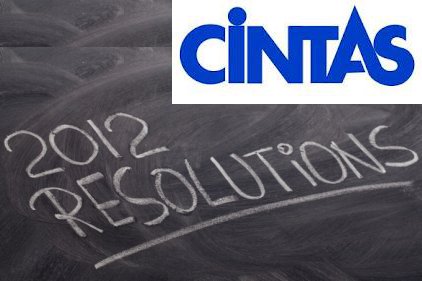
The top safety resolutions for 2012 include:
1. Perform regular audits of workplace safety initiatives: Benchmark safety programs to establish a baseline of performance. Once this has occurred, regularly audit the program to ensure it is working. Solicit feedback from employees and work with third-party organizations to pinpoint areas that work well and/or need improvement.
2. Set a zero-injury goal: Studies show that workplaces with higher employee engagement programs are less likely to have accidents and that reducing the frequency of incidents allows worker productivity to remain high. To achieve a culture of safety, create prevention programs that exceed compliance regulations. Engage employees in the safety process by having them lead committees and facilitate safety audits.
3. Offer training classes that engage employees: Blended training programs that incorporate adult learning principles with traditional and technology-mediated learning is more likely to capture the attention of employees, and in turn, be more successful. In addition to adjusting meeting formats, focus the content of safety meetings on topics of interest to employees.
4. Raise awareness of leading causes of workplace injuries: Overexertion from excessive lifting, falling objects and slip and fall injuries are among the most common reported workplace incidents. Ensure that employees understand the conditions that lead to common injuries and the potential hazards associated with not following protocol. For example, to reduce slip and fall incidents, train personnel to clear excess liquid and objects from the floors immediately.
5. Implement a first-aid cabinet: Having a first-aid cabinet in the workplace ensures emergency response can occur quickly in the event of an injury or illness. Cabinets provide a centralized location for bandages, aspirin and antibiotic ointment so employees know where to go should an accident occur. This also makes it easier to maintain inventory and keep track of items that need restocking.
In 2007, OSHA fined Cintas Corp. a proposed $196,000 for 15 safety violations following an inspection of its Mobile, Ala, plant.
Also in 2007, OSHA proposed $2.78 million in penalties against Ohio-based Cintas Corp. following an inspection into the March 2007 employee death at the Cintas laundry facility in Tulsa, Okla. The employee was killed when he fell into an operating industrial dryer while clearing a jam of wet laundry on a conveyor that carries the laundry from the washer into the dryer.
Cintas is the largest uniform supplier in North America, with more than 400 facilities employing more than 34,000 people. The facility in Tulsa has 160 employees.
In July, 2011, Cintas’s facility in Franklin, IN was awarded OSHA’s Voluntary Protection Program Star status.
In November, 2011, Cintas’s San Jose facility was named a VPP Star site.
According to the company’s website, Cintas currently has 132 facilities nationwide actively seeking either VPP certification or other recognition under OSHA safety excellence programs.
Looking for a reprint of this article?
From high-res PDFs to custom plaques, order your copy today!