Best practices for safe chemical handling in parts washing processes
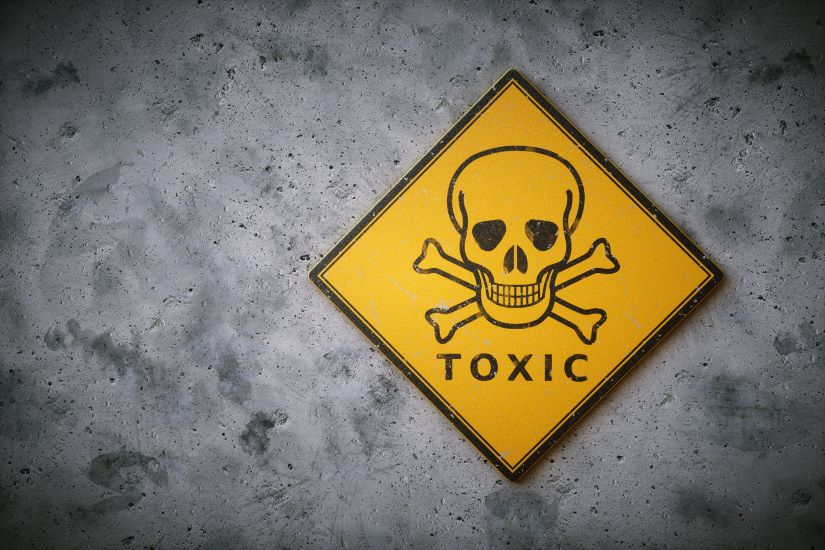
Credit: Getty Images
Parts washers are essential assets to countless industries, providing quality automotive, medical and electronic equipment. However, these workers frequently handle dangerous chemicals, requiring the most attentive training and safety adherence. What are the best practices as output expectations and parts complexity increase?
Conducting a risk assessment
Risk assessments identify areas of opportunity to make parts washing safer. Without recognizing oversights, then complacency and quality concerns may arise.
First, washers should identify chemicals that are a part of the process, and outline their risk profiles. What are the hazards workers are most exposed to in the workplace? Environmental considerations are also crucial to mark.
Then, companies must implement controls and training programs to mitigate the most prominent safety threats. For example, hypochlorite fumes are more potent than others, whereas peracetic acid and other oxidizers should never be near water. Inspire emergency protocols based on these risks, providing first aid training to employees as needed.
Following Personal Protective Equipment (PPE) compliance
Assessing risk is a foundational requirement but so is adhering to PPE guidelines. Parts washers can interact with the world’s most dangerous chemicals with the right visors, gloves, suits and glasses. PPE is the mandatory shield for the rest of these best practices to fall behind. These frameworks are the most critical when discovering the latest industry-leading recommendations:
- Automotive Industry Action Group (AIAG): Specifies guidance for auto parts cleaning.
- Globally Harmonized System of Classification and Labeling: Classifies chemicals with Safety Data Sheets (SDS) and recommends PPE based on each.
- Code of Federal Regulations: Advises respiratory, eye, face and general PPE in 40 CFR Part 262 and 29 CFR 1910.132-134 for parts washing processes during production, training and maintenance.
- National Fire Protection Association: Details electrical risks near chemical and flammable components in code 70E.
- International Safety Equipment Association: Decides what gloves, goggles, face shields and other garments are acceptable for chemical resistance.
All PPE should be accessible to parts washers in safe environments prior to interacting with chemicals. Adequate storage, maintenance and inspections solidify their integrity. Legislation is still coming out today, as the EPA just announced the most sweeping chemical safety rule in history, backed by the American Chemistry Council despite industrial opposition.
Installing top-tier ventilation
Local exhaust ventilation systems and filters considering novel pollutants at the smallest sizes are crucial for isolating fumes and removing health deterrents. Fumes hoods capture vapors near or at the creation point, preventing them from spreading to other parts of the washing area. Washers working with fast-spreading fumes should wear adequate face masks with reduced inhalation, but a facility’s greatest asset will be well-maintained vents.
Incorporate automation
Automation prevents employees from directly interacting with the most dangerous aspects of their job, especially with toxic chemical solvents like caustics and butyl cellosolve. This makes workplaces safer and optimizes for efficiency. High-volume washers reduce the number of wash cycles parts must undergo, saving resources and lessening risk by altering dilution ratios or incorporating neutralizers.
Another perk is the minimal manual involvement, which keeps employees out of high-pressure, harsh environments. Industry 4.0 technologies for parts washers may also include water-based machinery, which decreases the frequency with which staff has to mess with hazardous, irritating chemicals like toluene and acetone.
Automation tools, like the Internet of Things (IoT), can monitor chemical use and determine how frequent maintenance checks are necessary to prevent disruptions that could lead to more dangerous circumstances.
Implement spill response
Part of emergency protocols should be spill response plans. Chemical spills have the potential to harm more than washers — seepage into nature becomes a safety issue for wildlife and habitats. Spill kits should always be nearby as a precautionary measure, always containing adequate quantities of absorbent materials, neutralizers and specialized PPE for spreading chemicals.
Washers will hopefully never encounter these circumstances, but should know how to react because regular drills are in place. Spill kits and proper training should be included in overall business continuity, preparing even the most recent staff for the worst-case scenario.
Handling safety
Chemical handling for parts washers will only get more demanding as novel treatments and liquids enter the scene. Contaminant and debris removal and processing optimize if workers consider safety from start to finish. To make workplaces better and more sustainable for their employees, high expectations are vital for using chemicals on parts responsibly.
Looking for a reprint of this article?
From high-res PDFs to custom plaques, order your copy today!