Dispelling the myth that your worksite is unique
“Accidents just happen around here”
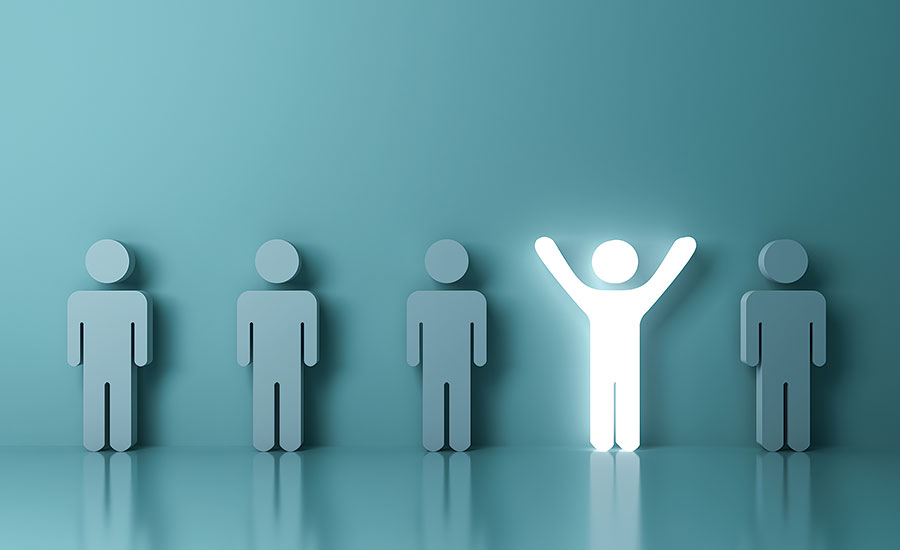
We tend to view our own industry, whatever it is, as unique. We’re prone to see our industry as having characteristics that distinguish it from other industries. I am often told by clients, “this business is unlike any other.”
Ford and General Motors are certainly different companies, but they are both in the auto industry. They are more alike than Ford and Neiman Marcus, or General Motors and General Mills. More broadly, Ford and General Motors are in the business of designing, manufacturing, assembling (and servicing and repairing) motorized/automotive equipment. So they bear some similarity to Caterpillar, Harley-Davidson, John Deere, and so on. But Ford or GM associates typically see themselves as having few if any meaningful common denominators with Yum Brands, or Procter & Gamble, or Delta Airlines.
Myth: HROs have nothing to learn
“High-reliability organizations,” (HROs) whose work requires a high level of technical skill and a high level of error management, often believe they have nothing to learn from “smokestack industries.” Flying airplanes or operating a nuclear power control room is just nothing like punching out widgets on an assembly line. In general, the more high-tech and professional an industry sees itself, the more likely its members are to see themselves as uniquely different from others.
Adopting “crew resource management” (CRM) communication and teamwork training into the commercial aviation industry was challenged by the widespread opinion that “pilots would only listen to and learn from other pilots.” So, “If you personally haven’t flown x-thousand hours in this aircraft, how could you possibly have anything of value to tell a captain?”
One carrier had behavioral science experts train their personnel in how to deliver CRM training partly because they assumed pilots would only listen to other pilots -- and certainly not pointy-headed professors/consultants who only ever “flew in the back.” But the excellent content of the training was developed by said pointy-headed professors, and the airline personnel were not training and development experts. They were, of course, expert pilots. But CRM training was not aimed at technical skills. When instructors got reasonable questions from participants, their knowledge base extended only as far as the training materials that the behavioral science experts had provided. To use the old phrase, their knowledge was “a mile wide and an inch deep.”
Myth: Manufacturers have nothing to learn
I’ve also had people in conventional manufacturing environments tell me they have nothing to learn from HROs. “We do fabrication and assembly work… we don’t fly airplanes or do surgery in the operating room; those examples don’t fit us.”
Points taken. And disagreed with (good naturedly, of course). I would argue, to the contrary, that we have much to learn from industries other than our own, even industries much different from our own.
In every industry, objectives are set by leaders which must be met by employees. Common functions include production/operations, maintenance, sales and marketing, finance, HR. In order to accomplish their objectives, people must meet and communicate clearly and effectively. Disagreements must be resolved constructively. Common issues of employee safety must be addressed. The critical elements of a true high performance organization are generally the same across industries.
Reality: Knowledge transfer
I once took a group of managers and hourly employees in a fairly sophisticated high tech industry to visit an iconic team-based factory – that made dog food. From this experience the visitors learned a great deal about implementing self-directed work teams, pay-for-skill compensation systems, gain-sharing, effective plant safety committees, and much more.
Common issues bedevil many companies. HROs are in many ways a gold standard for safety. Due to the extreme consequences of accidents in their setting, they must continually focus on mindful, pre-emptive approaches to safe work. They focus on error reduction to the max. They run “what-if” scenarios. Still, accidents do occur. And when they do, the consequences can be catastrophic.
The same sort of error (or chain of errors) that might result in a factory maintenance associate getting a bad cut or a broken bone can, in an HRO, result in an airliner crash with massive loss of life. Or an oil spill with severe ecological and economic consequences. Or a surgical patient in a routine procedure being lost.
Importing strategies that work
HROs have to do it right. Why not import their strategies into non-HRO industries? The same errors that can cause calamities in HROs (plane crash; process explosion) can cause much more minor, but still serious, injuries in everyday manufacturing and construction. I have worked with industrial companies with recordable incident rates of five or more, and in at least one case, approaching ten. I have worked with heavy construction companies, and their industry is commonly identified by government statistics as the most hazardous, with the highest fatality rate. Those companies were not flying airplanes or running offshore oil rigs. But they really didn’t have to accept such a high rate of injuries. I have had welders tell me “when you weld, you are going to bet burned.”
Really? How about if we look at the procedures you are following, re-engineer our work environment, get the most modern tools to work with, establish guidelines for watching out for each other and continually coach each other in best-practice safe behaviors?
My general point is this: to the extent that HROs have achieved world-class safety results by focusing on specific strategies and tactics that improve their work systems and reduce avoidable error to at or near zero, why would any company not want to use those strategies and tactics? So you fabricate and assemble equipment, or work in a warehouse distribution center, or do heavy construction, or make household cleaning products. So you don’t work in a nuclear power plant. So what?
Accidents are not tightly bound to the specific work of your industry. They do relate to unsafe equipment, poor procedures, insufficient management support, lack of training, poor communication, fatigue, bad work habits, and unsafe acts. Those factors, like many others, are not industry specific.
Looking for a reprint of this article?
From high-res PDFs to custom plaques, order your copy today!