Responding to safety scrutiny: Tesla CEO more direct than most
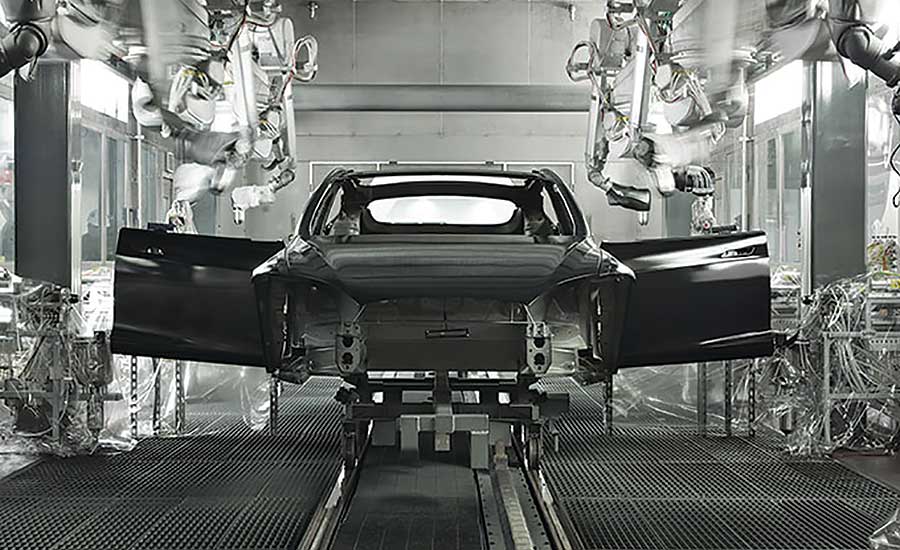
Several years ago I wrote what was to be a cover story on a $4 billion, well-known “brand” corporation and its reinvigorated safety efforts after a publicized worker fatality, only to be informed by the top safety manager that he would lose his job if the story was published. The piece was positive in describing the company’s determination never to have a tragedy like that again, but apparently the higher-ups did not want any mention of the accident – to the extent that they would fire a well-respected safety executive.
It’s something of a tradition in workplace safety to observe how different company cultures react to bad news about accidents, hazardous conditions, OSHA penalties, worker complaints and negative press. In my experience, most of the time defenses go up immediately. The “safety first” flag is vigorously waved. Some companies will contest OSHA in court. Spin doctors downplay any negatives to the media. The top execs are often silent, or issue short disclaimers and denials. Interviews with safety officials, if granted at all, are scripted and monitored. After all, safety is like motherhood and apple pie – a company just cannot be perceived as not caring.
The barrage begins
In mid-May this year, The Guardian, a UK-based newspaper, broke a story about factory workers at electric car manufacturer Tesla’s Fremont, Calif., plant being rushed out in ambulances more than 100 times since 2014 suffering from fainting spells, dizziness, seizures, abnormal breathing and chest pains, according to incident reports obtained by the newspaper. A media barrage ensued. “Tesla workers are passing out on the factory floor.” “Tesla factory workers are a burned-out bunch.” “Grueling conditions are taking a toll on Tesla’s factory workers.”
Tesla’s culture is a mix of Silicon Valley startup adventurism and traditional manufacturing muscle and sweat assembly, and the company, founded in 2003, did not respond in typical fashion.
CEO Elon Musk, a 45-year-old South Africa-born, Canadian-American business magnate, investor, engineer and inventor, got on the phone with The Guardian reporter for an interview that was woven into the investigative report. His accessibility, directness and blunt talk was atypical.
‘We’re a money–losing company’
Workers had been “having a hard time, working long hours, and on hard jobs,” Musk told the reporter. “We’re a money-losing company. This is not some situation where, for example, we are just greedy capitalists who decided to skimp on safety in order to have more profits and dividends and that kind of thing. It’s just a question of… how do we survive? How do we not die and have everyone lose their jobs?”
He added that starting a car manufacturer from scratch was likely “the worst way to earn money, honestly. On a risk-adjusted return basis, an auto company has to be the dumbest thing you could possibly start.”
Sleeping on the floor
In early 2016, Musk told The Guardian he slept on the factory floor in a sleeping bag “to make it the most painful thing possible. I knew people were having a hard time, working long hours, and on hard jobs. I wanted to work harder than they did, to put even more hours in. Because that’s what I think a manager should do.”
According to The Guardian investigation, Tesla’s manufacturing practices seemed to have been most dangerous in its earliest years. Tesla does not dispute that its recordable incident rate (TRIR) was above the auto industry average between 2013 and 2016. The company released data indicating its TRIR went from slightly above the industry norm in late 2016 to a record in the first quarter of 2017 that was 32 percent better than average.
The company attributed the improvement to its decision to add a third shift (10,000 production workers are employed at the sprawling Fremont facility), the introduction of a dedicated team of ergonomic experts, and improvements to the factory’s safety teams.
‘These jobs are not for everyone’
On its website, Tesla describes its culture as “not just an automaker, but also a technology and design company with a focus on energy innovation.” And it concedes: “These jobs are not for everyone; you must have a genuine passion for producing the best vehicles in the world. Without passion, you will find what we’re trying to do too difficult.”
How often do you hear a company state “these jobs are not for everyone” and you might just “find what we’re trying to do too difficult”?
Or a CEO admitting his company went through a period of “production hell,” as Musk did in 2016. He acknowledged that there was mandatory overtime to make up for production stoppages, but that the frequency of it was dropping. He said that he's “not losing sleep at night because of production issues” anymore, but that he has “a whole lot of mental scar tissue.”
To be sure, Musk also went on the offensive. He called the allegations by 15 current and former employees interviewed by The Guardian of harsh, dangerous conditions and production taking priority over safety “morally outrageous” and claimed one of the complainants was hired by the United Auto Workers (UAW) to agitate for a union. The UAW denied the claim, stating that Tesla employees have reached out about forming a union.
“It’s incredibly hurtful, and, I think, false for anyone to claim that I don’t care,” Musk said.
When ISHN checked Tesla’s job board on its website in late May, the company was seeking “a motivated Associate Environmental Health & Safety Manager.” Responsibilities include compliance with safety and environmental regs, ISO 14001 and OHSAS 18001; managing a team of one to four safety engineers and/or technicians; being on call 24/7; dealing with safety issues and corrective actions to get at root cause factors; participating in all tool install and construction design reviews; approve all new gas and chemical additions to processes; and “proactively take ownership of site EHS issues, concerns, improvements and program development.”
The position requires ten years-plus experience, a four-year EHS-related degree, and “evidence of exceptional ability.”
Looking for a reprint of this article?
From high-res PDFs to custom plaques, order your copy today!