Averting chaos: Preparing for emergencies
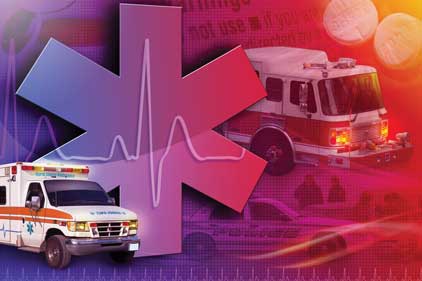
OSHA requires employers to evaluate their workplace for hazards (29 CFR 1910.1200). Plans, procedures, engineering controls and personal protective equipment (PPE) are then often used to help prevent those hazards from affecting workers’ health and safety. Emergencies such as natural disasters and chemical spills are forms of workplace hazards, and the need for planning, employee training and drills can be linked to more than one OSHA regulation.
Emergency Action Plans
(29 CFR 1910.38)
Emergency Action Plans document the directions that employees are to follow when there is a fire or other workplace emergency. Emergency evacuation plans and procedures for employees who will remain to operate critical equipment must be described.
The plan must also detail how alarms will be used to notify employees of an emergency. Training is a required element of Emergency Action Plans to ensure that everyone understands the alarms that will be used as well as their role during an emergency.
Process Safety Management
(29 CFR 1910.119)
The Clean Air Act Amendments of 1990 required OSHA to create regulations to protect workers from the risks associated with releases from hazardous chemical processes. Facilities with greater than a threshold quantity of any of the 130 chemicals listed in the Process Safety Management Standard must perform a hazard assessment for those chemicals and any processes involving them. This assessment is the basis for developing plans and procedures that prevent releases and keep employees safe.
Anyone working with or near a chemical process must understand the hazards of the chemicals and processes they are using. This knowledge forms a basis for teaching employees about the safe work practices and standard operating procedures that will be used to prevent chemical releases and maintain a safe work environment.
Employee training must also include reviews of both normal and emergency shut-down operations as well as emergency evacuation procedures. Regular drills are required to solidify these practices so that when they are needed in an emergency, they are second nature.
Fire Prevention Plans
(29 CFR 1910.39)
Employees who will be exposed to fire hazards must be trained to protect themselves. The storage and use of flammable materials is common in many industries and presents hazards that may endanger employees and the facility. Having a plan to control ignition sources and the accumulation of flammable materials can help minimize the chance of a fire.
Fire prevention plans must contain proper storage and handling procedures for anyone working with flammable materials. These plans must also document the procedures that will be used in the event of a fire as well as the equipment that is available for firefighting operations. In addition to this regulation, facilities with portable fire extinguishers (29 CFR 1910.157) or other fire extinguishing systems (29 CFR 1910.160) must also ensure that employees know how to operate this equipment.
HAZWOPER (29 CFR 1910.120)
Responding to small spills that don’t pose an emergency can be covered with standard operating procedures. But when employees respond to emergency spills and releases, they must be trained under OSHA’s Hazardous Waste Operations and Emergency Response (HAZWOPER) Standard. This standard identifies various levels of training for everyone from personnel who may witness a spill and notify the appropriate people to clean it up, to the actual responders who will contain, control and clean up the spill.
Facilities need to train their employees to understand the difference between incidental and emergency spills. No set of criteria can be used to determine this because every spill is different.
A spill of just one milliliter of mercury creates a different response scenario than a 200-gallon release of hydraulic fluid fully contained in a processing area. Ensure that those who could encounter a spill know their limits and know who to call for emergency response. Evaluate specific chemical hazards throughout your facility and establish guidelines based on those hazards as well as employees’ level of training.
Confined Space
(29 CFR 1910.146)
Confined spaces, by definition, are not designed to be continuously occupied – which should immediately throw up a few safety flags. Often confined spaces present a unique set of hazards, and entry is only obtained after permits have been established. These permits establish the conditions that must exist before someone may enter, what protective equipment is necessary, and what tools and procedures ensure the entrant’s safety.
Anyone entering a confined space needs to understand the hazards that may be present, be able to use any safety equipment that is needed, and have the skills to safely perform any duties that they are assigned to do in the confined space. Confined entry attendants, entry supervisors and rescue providers must also be properly trained to understand their duties to monitor, protect and aid the confined space entrant if there is an emergency.
Control of Hazardous Energy (Lockout/Tagout)
(29 CFR 1910.147)
Uncontrolled electricity, hydraulic lines and high-pressure water pipes are a few examples of hazardous forms of energy that can cause injuries or other emergencies in a facility – especially during machine servicing or when equipment starts up unexpectedly. Having lockout/tagout plans and procedures in place can prevent electrocutions, cuts, burns and other injuries.
When lockout/tagout processes are used, it is important to train both the employees who will perform the work as well as others who may be in the area where the work is performed. All should know the purpose of locking or tagging out equipment and the importance of not removing or altering tags while work is being performed.
First Aid and Medical Services (29 CFR 1910.151)
Facilities need to have medical services such as hospitals, clinics or infirmaries in “near proximity to the workplace.” In an interpretation letter, OSHA clarifies that if there is a chance for serious injury, the medical provider should be available within three to four minutes. If medical services are not that close, first aid supplies should be stocked, and a person (or persons) needs to be adequately trained to render first aid until emergency medical services can be provided.
Because it can reasonably be expected that those who are trained to render first aid may be exposed to blood or infectious substances while helping an injured person, employers should also train first aid responders in OSHA’s Bloodborne Pathogen Standard (29 CFR 1910.1030).Training must include the use of personal protective equipment and engineering controls as well as sanitation practices, medical evaluations and other exposure control methods.
Hazard Communication
(29 CFR 1910.1200)
Safety data sheets and container labels provide reminders of chemical hazards, but employees must understand them. OSHA requires employers to use effective training methods to ensure that employees understand the hazards and dangers of chemicals used onsite.
Employees should know the location of the written hazard communication plan and safety data sheets. The standard also requires employees to be able to detect the presence of hazardous chemicals in a work area as well as releases of those chemicals. They should be able to take appropriate precautions to protect themselves, including the use of established standard operating procedures, engineering or administrative controls and personal protective equipment.
Making plans work
Identifying hazards and creating plans and procedures is an essential first step toward being prepared for emergencies. Training and drills make sure what’s written on paper can and will happen when unexpected emergencies occur. Incorporate preventative measures and emergency measures into your standard work procedures to ensure that when the time comes to use them, learning will prevail and chaos will be averted.
Looking for a reprint of this article?
From high-res PDFs to custom plaques, order your copy today!