GE VP Speech at VPPPA
GE’s philosophy: Fix systems, not people
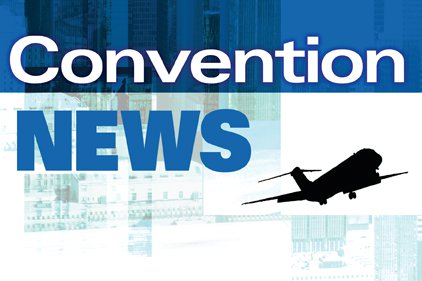
By ISHN Editor Dave Johnson, reporting from the annual VPPPA conference
Mistakes will happen, it’s human error, people are people working within the context of systems, so GE takes people out of the equation and focuses on risk, the risks of the systems that employees work within, said Ann R. Klee, the VP for Environment, Health and Safety at GE, speaking at the opening session of the 30th annual meeting (Aug. 25-28) of the Voluntary Protection Program Participants’ Association (VPPPA), in National Harbor, MD, outside of Washington DC.
GE did not want its more than 300,000 employees worldwide, at more than 500 manufacturing sites, “rolling their eyes at another safety program,” so it decided that the company’s focus on fixing systems, not people, would be a philosophy, not a program, she said. And it would not pertain only to EHS. It is a corporate-wide principle, which has seen some quick success stories in quality as well as EHS, and is spreading to other areas of operation, Klee said.
She gave the example of forklift truck operators at one site who experienced too many incidents of colliding with product in the warehouse. Initially, GE’s approach was “three strikes and you’re out;” if an operator had three incidents, he or she was ordered back for more training. When GE investigated why the incidents were occurring at unacceptable levels, it asked operators, “Who in the plant are the best forklift operators?” The answer: operators in the warehouse, the same people subjected to retraining.
Under the fix systems, not people philosophy, GE studied where most of the forklift-product incidents occurred; which warehouse intersections were most dangerous, where most incidents occurred, and assessed the risks posed by those intersections. It then made improvements to the intersections, with a subsequent reduction in the number of incidents and product damaged.
Another aspect of GE’s philosophy centers on giving employees more leeway to use their judgment in decision-making situations. Klee cited as an example replacing STOP signs at site intersections – what she called a “rules-based” don’t-think-about-it-do-it methodology, and replacing sharp-cornered intersections with circular traffic patterns. The move taps into employees using their own judgment, perceptions, “risk assessments” and thinking. GE was questioning if it was using the full potential of its workforce – their judgments, perceptions, problem-solving and thinking – when it decided to move away from a rules-based approach in this example, and others, said Klee.
GE’s operating philosophy, again, it’s not limited to EHS, shifts the paradigm away from traditional EHS approaches or reactions to problems of using training or re-training (though it does not eliminate training by any means) and command-and-control rules (though rules are still part of the game) and puts the emphasis on risk, fixing system risks, and on individuals’ ability to make the right choices and decisions.
This is how GE’s philosophy is described on its website www.gesustainability.com/how-ge-works/health-safety/--
“The Company’s Health & Safety program includes elements that 1) create a culture of operational ownership; 2) protect employees from the risks associated with the work they perform; 3) take enhanced control measures to protect employees engaged in elevated risk activities or high-risk chemical processes; (4) defend against human error including the organizational and systematic factors that influence human behaviors; 5) drive employee engagement; and 6) create a learning culture regarding incidents that do occur and share lessons learned across the Company.
Operational Ownership and Risk Control
“GE believes that workplace health and safety begin with a strong culture of operational ownership. Accordingly, while GE employs a talented and experienced network of health and safety professionals, it places primary responsibility for health and safety upon its operating managers. GE tracks leading indicators (for example, EHS Framework scores) and lagging metrics (for example, injury and illness rates) at its facilities and operating units, and holds its operating managers accountable for their results.
“In 2013, a team of experienced EHS and operational leaders created a new EHS Framework management system to drive a stronger risk-based hazard-identification and -control process that has clarified guidance and is simpler to execute. This simplified system will enable our EHS professionals to spend more time working with employees to identify and eliminate or controls hazards.
“To reinforce operational ownership, GE’s operating managers regularly deliver presentations on their health and safety performance in a unique live forum called Session E. During Session E, the Company’s corporate and business leaders review individual managers’ health and safety metrics, probe their commitment to workplace safety and review plans for improvement. The Session E process demonstrates GE’s commitment to hold its leaders accountable for health and safety.”
In 2013, GE corporate-wide had a recordable incident rate of 0.94 and a days away from work rate of 0.33. Rates are based on 100 employees working 200,000 hours annually. It has a total of 244 Voluntary Protection Program sites.
GE has seen a 12% reduction in the U.S. since 2008 in health-related absences, and it has expanded itsHealthAhead program to promote employee wellness to 480 sites covering about 220,000 employees.
The company has achieved a 37% reduction in recordable injuries since 2003, and an 8.7% decrease in 2012-2013. Its days-away-from-work incident rate has been reduced 13% since 2003 and was reduced 17.5% in 2012-2013. Toward its goal of zero work-related fatalities, the company for 2013 reported six fatalities in a single airline crash and two fatalities in motor vehicle crashes.
Looking for a reprint of this article?
From high-res PDFs to custom plaques, order your copy today!