Who’s serious about safety?
An accountability system for supervisors
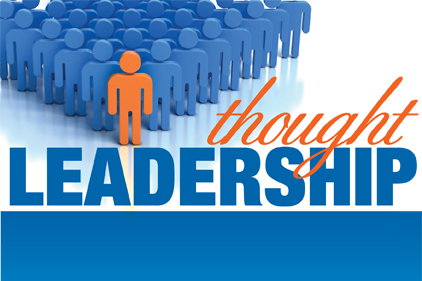
As safety professionals, we all know the difference between the safety performance of workers under a safety-oriented supervisor and workers under a supervisor that does not push safety. A company’s front line supervisors can make or break a safety culture. The Safety Accountability for Supervisors (SAS) program is a simple, effective tool to get the front line supervisors to take safety much more seriously.
Before the program is implemented, it should be explained to all of the concerned parties. This should also include a commitment from upper management and a statement that these results will weigh heavily during evaluations.
SAS is simply a spreadsheet that tracks safety violations and assigns the results to the front line supervisors and managers. In the following example, a company has three locations, Tampa, Miami and Pensacola. Tampa has one Manager and no Supervisors. The Manager is the Supervisor. Miami has a Manager and two Supervisors. Pensacola has a Manager and three Supervisors. Every time that a worker receives a safety violation, it is also entered for his Supervisor. The Manager’s rating is the total of his Supervisor’s ratings. Here is what it would look like:
Tampa Manager | Miami Manager | Pensacola Manager |
Mike Smith | Al Martin | Beth Jones |
2 | 17 | 5 |
Supervisor | Supervisor | Supervisor | Supervisor | Supervisor | Supervisor |
None | Chuck Adams | Fran Clark | Dan Davis | Jeff Evans | Keith Foster |
2 | 17 | 0 | 0 | 4 | 1 |
At first glance, it would seem that Supervisor Chuck Adams in Miami is not promoting or enforcing safety for his workers. Additionally, Manager Al Martin appears to not take safety very seriously.
When using the SAS system, if a Supervisor issued a safety violation to one of his own workers, that violation would not be entered into either his or his Manager’s rating. If a Manager issued a safety violation, it would not be entered into his rating, but it would be entered into the responsible Supervisor’s rating.
Perhaps, the Tampa location only has 20 workers, the Miami location has 100 workers and the Pensacola location has 200 workers. In that case, the numbers would have to be adjusted. To use 100 as the set point, we would have to adjust the numbers by multiplying Tampa by 5 and multiplying Pensacola by 0.5. Now the spreadsheet would look like this:
Tampa Manager | Miami Manager | Pensacola Manager |
Mike Smith | Al Martin | Beth Jones |
10 | 17 | 2.5 |
Supervisor | Supervisor | Supervisor | Supervisor | Supervisor | Supervisor |
None | Chuck Adams | Fran Clark | Dan Davis | Jeff Evans | |
10 | 17 | 0 | 0 | 2 | 0.5 |
Of course, Mike Smith will say, “Come on, I only had two incidents, but the correction factor put me up near the top.” That may be a valid point. It is something to consider.
So, while these are not hard numbers, in normal circumstances, they will be a good indication of which Managers and which Supervisors are being serious about safety. Even more important than simply knowing who is serious about safety, the SAS program will change the performance of Managers and Supervisors because their safety performance is being rated and evaluated.
Looking for a reprint of this article?
From high-res PDFs to custom plaques, order your copy today!