AIHA comments on OSHA's PSM standard
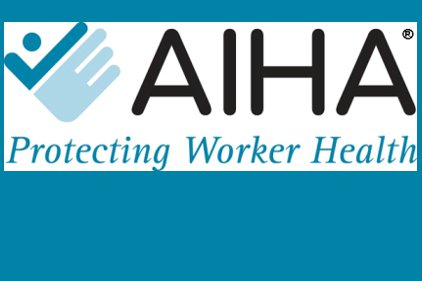
The American Industrial Hygiene Association (AIHA) this week sent its official comments to OSHA on the agency's Request for Information (RFI) to the Process Safety Management (PSM) Standard, which was published in the Federal Register on December 9, 2013, Volume 78, No. 236, beginning on Page 73756.
OSHA said the RFI was in response to an Obama Administration request that the agency identify issues related to modernization of its PSM standard and related standards necessary to meet the goals of preventing major chemical accidents. While this RFI is in response to several uncontrolled releases of highly hazardous chemicals over the past several years, the most recent event occurred in West, Texas, on April 17, 2013, resulting in the deaths of at least 15 individuals.
AIHA Comments on the Request for Information:
(by AIHA President Barbara J. Dawson, CIH, CSP)
Section 6. Revising the PSM Standard to Require Additional Management System Elements
Q28. Would expanding the scope of the PSM standard to require additional management-system elements, or expanding the scope of existing PSM management-system elements, prevent worker injuries and fatalities?
AIHA supports requiring additional management-system elements or expanding the scope of the existing PSM management-system elements in order to better protect worker health. AIHA recognizes the important relationship between effective management systems and worker health and safety, which is why AIHA has worked with representatives from dozens of organizations to develop and publish the first U.S. occupational safety and health management system consensus standard, ANSI (American National Standards Institute)/AIHA Z10.
ANSI/AIHA Z10 was developed as a voluntary consensus standard, and therefore, it is not appropriate to adopt it in its entirety as a regulatory requirement. While not citing all of the elements of a management system, AIHA encourages OSHA to include some improvements to the PSM standard, including the following, based on ANSI/AIHA Z10:
1. Employers should clearly document roles, responsibilities, and lines of authority under the PSM standard. Appendix B of ANSI/AIHA Z10-2012 includes an example of documented roles and responsibilities. Such a requirement would be consistent with the risk management plan requirements in 40 Code of Federal Regulations (CFR) 68.15(a), and therefore would not be expected to create any additional burden for most PSM-covered facilities.
2. Employers should establish and implement a documented plan for achieving PSM objectives. The plan should define resources, responsibilities, timeframes, intermediate steps, and appropriate measurements of progress and ways in which to evaluate this progress. Employers should periodically, e.g., annually, review and update the plan. Appendix E of ANSI/AIHA Z10-2012 provides guidance and an example implementation plan.
3. Employers should establish a process for achieving feasible risk reduction, based on a preferred hierarchy of controls, such as the one described in Appendix G of ANSI/AIHA Z10-2012 and summarized as follows:
a. Elimination;
b. Substitution of less hazardous materials, processes, operations, or equipment;
c. Engineering controls;
d. Warnings;
e. Administrative controls; and
f. Personal protective equipment.
4. Employers should establish a management review process. Top management should review the PSM program at least annually to recommend improvements and ensure its continued adequacy and effectiveness. Reviews should include a presentation of progress toward program objectives in an easy-to-understand format, e.g., scorecards, to focus top management on the PSM elements that require the most attention. Appendix M of ANSI/AIHA Z10-2012 includes an example of a management review scorecard. Action items from the management review should be documented, communicated to affected individuals, and tracked to completion. AIHA recognizes that this recommendation could be addressed by modifications to the PSM compliance audit requirements.
Section 7. Amending Paragraph (d) of the PSM Standard to Require Evaluation of Updates to Applicable RAGAGEP
AIHA supports the inclusion of a requirement for facilities to (1) evaluate updates to applicable recognized and generally accepted good engineering practices (RAGAGEP) and (2) determine the resulting risk reduction from these updates for the facility in question. It is important, however, to be clear that this requirement is focused on the “evaluation” of the updates and does not require facilities to continuously update their equipment and/or processes with every change in RAGAGEP.
Q36.What would be an appropriate time period in which to conduct this evaluation? Would such a requirement be more appropriate in another paragraph of the PSM standard? For example, should such a requirement become part of the Process Hazard Analysis revalidation requirements at 29 CFR 1910.119(e) (5)?
AIHA believes that it is appropriate for an employer to evaluate and update its selected RAGAGEP concurrent with the process hazard analysis (PHA) revalidation. This would allow the employer to identify and address recommendations as part of the PHA process. Therefore, AIHA recommends that OSHA require a RAGAGEP review as part of 29 CFR 1910.119(e) (5).
Section 8. Clarifying the PSM Standard by Adding a Definition for RAGAGEP
The engineering practices and ongoing maintenance of facility equipment are crucial to any continuous improvement system employed in the facilities covered by PSM. The creation of the term “RAGAGEP” was a useful advance in the continuous improvement concept highlighted in the PSM standard. However, given that PSM is a performance-based standard, there is significant confusion regarding what constitutes RAGAGEP.
AIHA supports the inclusion of a more detailed definition of RAGAGEP and believes that this would increase worker protection and enhance process safety by making it easier for facilities to determine applicable guidance.
Q39.Would adding a definition for RAGAGEP to the PSM standard improve understanding of PSM requirements and prevent worker injuries and fatalities? If so, what specific definition for RAGAGEP should OSHA add to the PSM standard?
AIHA believes that while beneficial, a more detailed definition of RAGAGEP would need to be relatively broad to include codes, consensus standards, recommended practices, and guidelines that relate to engineering, operation, or maintenance activities. This section of the regulation should, therefore, list organizations that commonly provide access to these documents, including, but not limited to, the International Code Council; ANSI; the American Petroleum Institute; the American Society of Mechanical Engineers; the Instrumentation, Systems, and Automation Society; and the National Fire Protection Association. When there is more than one applicable RAGAGEP, OSHA should provide guidance on how facilities should determine which takes precedence.
As discussed in our response to question 36, employers should assess changes to RAGAGEP during PHA revalidations.
Section 9. Expanding the Scope of Paragraph (j) of the PSM Standard to Cover the Mechanical Integrity of Any Safety-Critical Equipment
Q43. Would expanding the scope of Sec. 1910.119(j) to cover the mechanical integrity of all equipment the employer identifies as critical to process safety, in addition to the equipment listed in existing Sec. 1910.119(j), prevent worker injuries and fatalities?
AIHA supports expanding the scope of Sec. 1910.119(j) to cover the mechanical integrity of all equipment that the employer identifies as critical to process safety. AIHA believes that this is a common-sense change to the PSM standard that is consistent with the current practices of most PSM-covered facilities, and therefore unlikely to create a significant burden. The proposed change to the mechanical integrity requirements would provide improved clarity and be consistent with several OSHA letters of interpretation, the preamble to the PSM standard, and many other generally available guidance documents.
Section 10. Need for a Clarifying Paragraph (l) for the PSM Standard with an Explicit Requirement that Employers Manage Organizational Changes
AIHA supports the inclusion of an explicit requirement that employers manage organizational change. This element rightly focuses on the importance of individuals as an important element/component of operational safety in how they relate to the facility equipment, procedures, and each other.
Although OSHA issued a letter of interpretation indicating that organizational changes are intended to be covered under the existing standard, the Chemical Safety and Hazard Investigation Board (CSB) reported that in 2002, 20 years after the PSM standard’s issue, only 44% of management of change (MOC) programs included analysis of organizational changes. Clearly, many facilities do not recognize the importance of organizational change on operational integrity, despite OSHA’s letter of interpretation. A stronger statement with more specific guidance is therefore needed and should be included in an update of CFR 29 1910.119. Documenting these types of changes is also important to ensure a complete assessment during future PHA revalidations.
This importance of organizational change is highlighted in other standards that AIHA has published, including the ANSI/AIHA Z10 Standard for Occupational Health and Safety Management Systems.
Q44. What do you consider to be an organizational change within the context of process safety management practices? For example, would you consider the following, or similar, changes to be organizational changes: reducing the number of operators in a shift; changing from 5-day to 7-day operations; changing from 8-hour to 12-hour operator shifts; replacing a unit manager; relocating a technical group to a remote corporate location; or changing a supervisory or compensation structure?
AIHA recognizes that a major difficulty in discussing the inclusion of organizational change in the regulatory process is the broadness of the term. AIHA recommends expanding the list of changes requiring MOC in 1910.119(l)(1) to include “organizational changes that can potentially impact process safety, such as changes to working schedules and conditions, personnel, staffing, task allocation, equipment, operations and maintenance schedules, and organizational structure or policy.” Therefore, the examples provided in question 44 would typically be subject to MOC unless the facility could determine that the proposed changes did not potentially impact process safety. Organizational changes tend to be subtle in nature, so it may be appropriate to provide additional guidance in Appendix C of the PSM standard.
Q46.Would clarifying Sec. 1910.119(l) with an explicit requirement that employers manage organizational changes prevent worker injuries and fatalities? What would be the economic impact of such a clarification? Are there any special circumstances involving small entities that OSHA should consider with respect to this option?
AIHA believes that having an explicit requirement that employers manage organizational changes will prevent worker injuries and fatalities. Although the letter of interpretation was an important stopgap measure following the CSB recommendations related to the BP-Texas City accident, it is clear that the impact of organizational change is not obvious or well assessed by many facilities. In their discussion of the revalidation of PHA’s, Frank and Whittle[1] list several organizational changes that are commonly undocumented and uncontrolled, often because they are simply not recognized as change. These include changes, substitutions, and additions in personnel, which modify the risk of the process.
Section 12. Revising Paragraph (o) of the PSM Standard to Require Third-Party Compliance Audits
Q57. Should OSHA revise Sec. 1910.119(o) to require employers to use compliance auditors (internal or third party) with certain minimum credentials or certifications?
AIHA believes that competence and independence are important principles for ensuring the integrity of PSM compliance audits.
Individuals conducting PSM Compliance Audits need to have the necessary knowledge and skills to perform such audits. This competence needs to include both appropriate technical knowledge and the knowledge and skills needed to perform effective compliance audits. AIHA believes that the determination of the auditor competence that is needed should rest with the organization for which the audit is being performed. Given the complexity and uniqueness of the various PSM processes that may need to be audited, AIHA recommends that OSHA avoid mandating specific credentials or certifications.
Independence and objectivity are important for ensuring the integrity of the PSM compliance audit results. Auditors should be independent of the activities and operations they audit. The organization should be responsible for establishing processes to ensure objectivity is maintained throughout the audit process and for ensuring the audit findings are truthful and accurate. This does not mean that audits need to be conducted by individuals external to the organization. Independence and objectivity can be maintained using internal resources. The use of third-party auditors does not, by itself, necessarily ensure objectivity.
Q59. Would revising Sec. 1910.119 (o) to require employers to respond to deficiencies found in the compliance audit within certain timeframes prevent worker injuries and fatalities? What would you consider to be an appropriate timeframe?
AIHA supports the requirement that sufficient progress be made in the timely completion of audit findings with appropriate company leadership responsible for the progress. Each audit finding should be assigned an appropriate timetable for correction based on its complexity with all recommendations requiring resolution by the next audit.
Conclusion
With this request for information, OSHA is hoping to improve the health and safety of workers by updating the process safety management standard and its management program for highly hazardous chemicals in the workplace. AIHA agrees that, while the process safety management standard has been effective in improving process safety in the United States and protecting workers from many of the hazards associated with uncontrolled releases of highly hazardous chemical, too many major incidents have continued to occur.
As an organization, AIHA’s members and goals focus on preventing occupational illness and injury as a fundamental principle of the industrial hygiene field. AIHA also develops science-based public policy and practice through collaboration across scientific and technical communities, and works to ensure that safe and healthy environments are provided for all workers and communities.
AIHA appreciates the opportunity to work with OSHA to help achieve the mutual goal of protecting American workers from workplace injuries and illnesses. As the agency moves forward, the AIHA offers its breadth of experience as a resource and we look forward to further opportunities to work with the agency on this and similar issues.
Looking for a reprint of this article?
From high-res PDFs to custom plaques, order your copy today!