CSB: Fatal explosion came after company ignored warnings
NDK Crystal received special exemption from state of Illinois
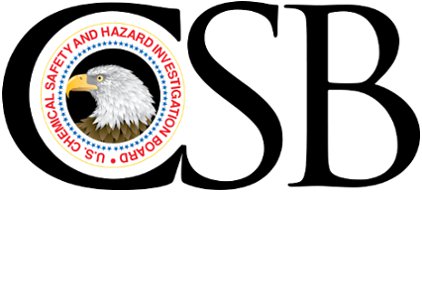
An explosion which occurred December 7, 2009, at the NDK Crystal manufacturing company in Belvidere, Illinois, fatally injuring a truck driver at a nearby gas station on the Illinois Tollway, resulted from corrosion in the walls of a pressure vessel, which went uninspected for years. The U.S. Chemical Safety Board (CSB) released those findings last week in a draft investigation report.
The CSB also released a safety video on the accident entitled “Falling through the Cracks,” which utilizes a computer animation to depict the sequence of events and investigation findings. CSB videos may be viewed at www.CSB.gov or www.youtube.com/uscsb.
8,000-lb fragment tore through a wall
The violent rupture occurred in the Number 2 vessel which was growing synthetic quartz crystals at extremely high pressure and temperature. One piece of steel from the building was blown 650 feet, striking the driver who was walking back to his vehicle. Another piece - a vessel fragment weighing over 8,000 pounds - tore through a wall at the facility, skipped across a neighboring parking lot and struck the wall of an automotive supply company where 70 people were working; but only one was injured.
A "near-inevitable catastrophe"
CSB Chairperson Rafael Moure-Eraso said, “Over the years, NDK ignored safety recommendations and warnings that it should regularly inspect the interior walls of the vessels. Because the vessels did not meet requirements of the widely recognized national pressure vessel code, the State of Illinois allowed installation of three of the vessels under a special exemption. In doing so, the vessels were incorrectly put into “non-corrosive” service. The manufacturer of the vessels - including the one that exploded years later - recommended annual inspections, but neither NDK nor the state performed the inspections. This set in motion a near-inevitable catastrophe.”
Company ignored a direct warning
The CSB found that had NDK Crystal ignored a direct warning by a third-party safety auditor called in by its insurance carrier following an uncontrolled leak of hot, caustic material in January 2007 from the lid of another similar pressure vessel. The consultant concluded the accident resulted from the vessel’s improper design, fabrication and material selection, determined four vessels were experiencing stress corrosion cracking, and advised against returning any of the facility’s eight vessels into service.
The insurance consultant cautioned “far more catastrophic scenarios are possible,” specifically naming danger of public death or injury at the gas station where the truck driver would be killed in 2009. But NDK never established an internal vessel inspection program and did not perform testing on the vessels before returning them to service. In the CSB case study on the accident, investigators note that raw mined quartz, or silica, was mixed with a corrosive sodium hydroxide solution at high pressures and temperatures. The resulting reaction with the steel vessels formed a layer of iron silicate, called acmite, on the inside of the vessel walls, which the company believed would protect the vessels from corrosion. Yet despite warnings that in fact corrosion might be occurring, resulting in a phenomenon known as stress corrosion cracking, or SCC, NDK continued to operate the vessels without performing the recommended inspections.
CSB lead investigator Johnnie Banks said, “After a review of the metallurgical testing data, the CSB found strong evidence of cracking on and near the inner diameter of the vessel fragment. The cracks reduced the vessel material toughness, which eventually led to large flaws resulting in the catastrophic failure. Stress corrosion cracking was the likely failure mechanism that caused the cracks. Had NDK conducted regular inspections, it would have discovered that the acmite coating was not protecting the vessel walls.”
State of Illinois did not conduct internal inspections
The CSB found that the Illinois Board of Boiler and Pressure Vessel Safety - after incorrectly designating the NDK vessels for non-corrosive service - did not conduct internal inspections. The state conducted three inspections of the vessel that failed in 2003, 2006 and 2009 (less than three months prior to the incident) but these inspections focused only on accessible external surfaces and did not look for inside corrosion.
The investigation determined that the vessels did not meet requirements of the American Society of Mechanical Engineers’ (ASME) Boiler and Pressure Vessel Code - which provides codes and standards that are adopted by state and federal regulators, including those in Illinois. The report found NDK vessel walls, eight inches thick, exceeded the recommended limits - seven inches, making them possibly too thick for proper heat treatment during manufacturing. Investigator Lucy Sciallo-Tyler said, “Evidence from the 2007 and the 2009 accidents suggests the excessive wall thickness at NDK resulted in improper manufacturing and contributed to the metallurgical damage mechanism that led to the catastrophic rupture.”
Zoning inaccuracy
The investigation also examined zoning laws that permitted NDK Crystal to be built near the Illinois Tollway Oasis and other nearby businesses including the automotive supply company. The CSB found that NDK’s property was zoned “light industrial,” for businesses such as car repair shops or lumberyards. Investigators determined that NDK should have been considered “heavy industrial,” in the category of oil refineries, metal and ore manufacturing and fertilizer manufacturing. However, the CSB found no evidence NDK informed the City of Belvidere that its pressure vessels would operate at extremely high and potentially dangerous temperatures and pressures typical of heavy industry.
Chairperson Moure-Eraso said, “NDK was not identified as a potential risk to the nearby community when it was built in 2001. In this and other CSB investigations, we express concern that potentially hazardous chemical facilities are permitted to be built near, or to continue to operate near public facilities. Particularly where the public might be endangered, companies should pay all the more attention to near misses and other warnings to preclude catastrophic accidents.”
Lead investigator Banks said, “Our report lists eight key findings, which in summary point to the results of regulatory ambivalence and a culture of not inspecting for problems in the face of clear warnings. NDK did not verify the integrity of the vessel coating; regulators incorrectly designated vessels as ‘non-corrosive;’ NDK did not examine vessels even after being told of corrosion; and the company didn’t perform inspections even after a recommendation to do so by the vessels’ designer – who knew the equipment better than anyone else.”
CSB recommendations
The CSB report makes eight safety recommendations to pressure vessel code and regulatory authorities, and to NDK.
The company has not resumed operations since the accident. But should it plan to restart, the CSB called on the Office of the Illinois State Fire Marshal to prohibit NDK the use of its existing pressure vessels for crystal growing operations. The board called on the company to ensure that any restarted process is rigorously demonstrated to be inherently safer than the existing one, and that NDK commission a facility siting study of all potential off-site consequences, emergency planning and response programs relevant to each failure scenario and to provide a copy of the study to the city and state.
The CSB recommended the marshal’s office see that the state’s pressure vessel approval process identifies corrosion and similar deterioration mechanisms and ensures regular inspections.
The CSB recommended that the American Society of Mechanical Engineers revise its Boiler and Pressure Vessel Code to include specific material thickness limitations to prevent environmentally-induced damage.
The report also recommends NDK Crystal implement a program to ensure the ongoing integrity of the interior coating of vessels, and implement an annual inspection and corrective action program in accordance with the pressure vessel inspection code of the American Petroleum Institute.
The CSB is an independent federal agency charged with investigating industrial chemical accidents. The Board does not issue citations or fines but does make safety recommendations to plants, industry organizations, labor groups, and regulatory agencies such as OSHA and EPA.
Looking for a reprint of this article?
From high-res PDFs to custom plaques, order your copy today!