Touch screen gloves facilitate data input
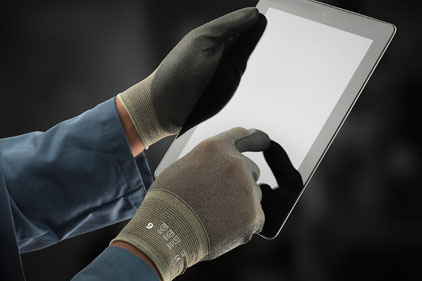
Smart phones, tablets and touch screens haven’t just become an integral part of the way we live — they’ve also become an important part of our work.
The use of touch screen technology is taking off in the industrial workplace. According to a recent survey conducted by Ansell, 65 percent of companies across the U.S. have started to use touch screens within the past three years. Another 90 percent of decision-makers indicated they expect more of their employees to work with touch screens during the next five years.
Touch screens such as smart phones and tablets are employed in a variety of industries — from industrial and consumer goods manufacturing to construction and transportation. A worker on an assembly line in an automotive manufacturing plant, for example, may use a touch screen to mark off when specific tasks are completed. A flow manager on a construction project may employ a touch screen to record the processes that have been completed during an inspection.
Most smart phones, touch screens and tablets used in industrial and construction environments include capacitive touch screens. The challenge is that most hand protection products on the market to date do not work with capacitive touch screens unless they have a conductive yarn that allows an electric charge.
In the absence of work gloves that promote the efficient use of touch screens, workers often remove the fingertips from their gloves or doff the product entirely. Working barehanded or with an altered glove product exposes workers to the risk of job-related injuries and results in non-compliance. The time required to constantly don and remove gloves can also negatively impact productivity.
Capacitive touch screens
Most smart phones, touch screens and tablets used in industrial and construction environments include capacitive touch screens composed of an indium oxide sheet that retains an electric charge. These devices are growing in popularity because they offer easy, finger-driven navigation and multi-touch capability.
Capacitive touch screens interpret touch by detecting a change in the electrical signal or impulse that is naturally generated by a worker’s body (bioelectricity) and transmitted to the fingertips. Tiny amounts of moisture, salts and oil allow electrons to flow between the worker’s hand and the device, conducting the energy necessary to operate a touch screen.
Ordinary materials used to manufacture work gloves and jackets are made with non-conductive materials, which are unable to activate touch screens. While work gloves are available that are intended for use with touch screens, most lack the consistency required to ensure proper touch screen interaction.
Most of these products are cut and sewn and include a chip in the fingertips that allows workers to use a touch screen. The chip, however, sometimes works loose and moves away from the fingertips, rendering the gloves useless as far as touch screen interaction is concerned. When this occurs, workers often have little choice but to remove the gloves and use their bare fingers to work with the touch screen — or remove the fingertips from their gloves altogether.
New touch screen technology
New technology was recently introduced to ensure workers can efficiently and effectively use a touch screen without removing their gloves. A new yarn covered with a layer of metal provides the conductivity needed between the fingertips and the gloves’ polyurethane coating. The coating enhances the sliding and finger movements on the screen, while providing the precision and sensitivity necessary to input data.
Depending on the application, new touch screen gloves are palm and finger coated with polyurethane for better mechanical protection or fingertip dipped for greater contact. The gloves also provide protection, as research has confirmed that many applications in which workers use touch screen devices also include abrasion risks.
Workers in the package, delivery and handling industry or shipping and receiving, for example, often work with potentially hazardous items such as corrugated boxes and metal hand trucks that can cause injury. A palm coated glove provides better mechanical protection to prevent abrasion, blisters and cut injuries.
Fingertip-dipped gloves offer greater flexibility because the palm is uncoated and allows greater movement, making the gloves suitable for working with smaller devices and objects that require greater dexterity. New finger dipped gloves may also be used as a liner under single use disposable gloves for life science manufacturing and test lab applications.
The demand for comfort
Most individuals who use touch screens wear their work gloves for an entire shift and demand sufficient comfort for all day wear. New touch screen glove technology incorporates a high tenacity polyamide continuous thread knitted into a seamless liner that includes copper for greater breathability, tactility and dexterity.
Workers on an assembly line or who operate machinery, for example, may need sufficient tactility to handle knobs and small parts. Maintenance and repair personnel also require dexterity and tactility when working with tools.
Machine operators, such as forklift drivers, are constantly moving product from one area of the manufacturing facility to another. They are required to use touch screens at each stage to log in lot numbers, location and date. Without the use of touch screen capable work gloves, they would have to constantly don and doff their gloves.
Summary
Touch screen devices are essential tools in today’s manufacturing, construction, logistics and transportation environments — and their use will only escalate. Glove manufacturers continue to research and develop new technology to meet workers’ performance needs when interacting with touch screens — while also keeping them safe and productive on the job.
While new touch screen glove technology is intended for use in multi-purpose applications such as inventory, machine operations, maintenance and transportation where abrasion risks and less severe cut hazards may exist, gloves are in development for applications with a higher cut risk, including many jobs in the construction market.
Looking for a reprint of this article?
From high-res PDFs to custom plaques, order your copy today!