Arc Flash: Layering levels of protection
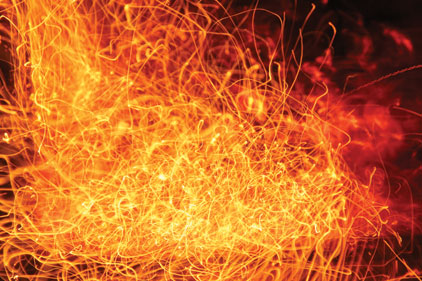
In a perfect world, workers would wear maximum-protection arc-rated clothing throughout their shifts, and comfort and cost would not be an issue. In the real world, however, protection must be balanced with worker comfort and cost in mind. Layering becomes one possible solution for increasing arc flash protection.
A layered system
During the work day, electricians or maintenance workers may move between various jobs with arc exposures of HRC 1, HRC 2 or HRC 3/4. Having easy access to the HRC 3 flash suit — and the time to don it — is not always the case. The tendency might be to skip the change and simply do the work with the HRC 2 daily wear.
Not having the correct level of protection when an accident occurs can be costly to both the employee and the employer. Burn injury to employees because of improper PPE can be painful, expensive and even fatal. Employers may have medical, legal or OSHA citation costs to bear, not to mention the loss of worker production and other workers’ lowered morale.
Layering garments is one way to achieve a higher level of arc flash protection. By having access to an HRC 2-rated coverall to pull on over an HRC 2 uniform, you can oftentimes provide a layered HRC 3 level of protection. This layering of protective clothing (along with the other appropriate PPE) satisfies the NFPA 70E standard for electrical safety requirements for arc protection to engage in the live electrical repairs in the area.
Many of the FR fabric manufacturers have test data showing the arc rating of a layered system.
For example: the combination of a daily-wear 7–oz. shirt with an arc rating of 8.7 cal/cm² (HRC 2) and a 7-oz. 8.7 cal/cm² arc-rated coverall over it achieved a 27.2 cal/cm² (HRC 3) level when tested. This layered combination achieves the HRC 3 level and is much easier to carry around and slip into than having an HRC flash suit readily available.
There is still the need for other PPE to protect other parts of the body like head, face, neck, eye, hand, etc.
The use of additional layering with the arc-rated coveralls serves two functions: it keeps the worker in compliance with the required safety regulations for body protection, and it provides the comfort and flexibility needed to complete on-the-job tasks. Because performing various jobs with varying arc exposures is not uncommon, this method of providing protection will likely cause minimal downtime and much less impact on operation efficiency.
Protection with comfort
The key to the above example is an analysis that shows a fairly high percent of all tasks at a typical industrial company are at HRC 2 or below, with some tasks at HRC 1 or 0. The example shows how the workers are adequately protected with a primary layer during duties that occupy most of their time. When moving to the higher arc-exposure task, the additional coverall boosts the protective clothing to HRC 3, providing heightened protection with acceptable comfort and mobility. It is then easy to shed the coverall when returning to more common duties.
Having to wear heavy gear for extended periods could affect worker comfort as well as the motivation to stay compliant. This example is not to negate the importance of heavy gear for intended uses. It simply shows that there are other paths to protection, particularly for workers who do not need HRC 3/4 for many of their typical duties.
Air factors in
Layering results are not simply a matter of adding manufacturer arc ratings for flame resistance. Air exists between layers of garments and acts as the ultimate buffer between garments and skin — it adds positively to the safety equation. Loose fit, not snug fit, creates a vital air “envelope” for additional insulation.
Air can provide protection above and beyond the layered garments. Test results show the inter-garment air layer contributes to an aggregate flame resistance surpassing the combined protection ratings of the two FR garments.
As shown in the example above, the actual layered rating of 27.2 cal/cm², is higher than the 17.4 cal/cm² sum of the two ratings. However, note that there is no measurable standard for the extra protection afforded by air trapped between garments. This is due to the many variables involved in individual situations such as amount of air trapped, tightness of garments, size of wearer, etc. Although adding the actual combined rating of the garments worn is a commonly used maximum rating number, the actual rating of the combination is not really known unless the specific combination of fabrics has been arc tested.
Outer and under layers
Another important fact to remember is the outermost layer must always be FR/arc rated. To add a non-FR layer, like a jacket or high-visibility vest, over the arc-rated daily wear defeats the purpose of wearing the arc-rated garment in the first place. If this worker was exposed to an arc flash, the outer layer would ignite and burn, with the heat of the burning layer transferring through to the arc-rated clothing underneath, thus nullifying the burn protection of the protective clothing.
Non-FR undergarments can also help provide additional protection but they are not recognized by the industry standards, like NFPA 70E. The important thing to remember about undergarments is they must be flame resistant and made from non-melting natural fibers.
It’s likely workers may require multiple garments to maintain safety while performing multiple tasks within a day’s work. There may be many pieces of clothing, but only one philosophy: proper protection at all times for changing risk. Know the arc flash exposure and wear the level of protection to match or exceed that exposure. Layering may be a sensible answer that combines comfort, convenience and safety.
Looking for a reprint of this article?
From high-res PDFs to custom plaques, order your copy today!