Stock up on warehouse safety signs and markers
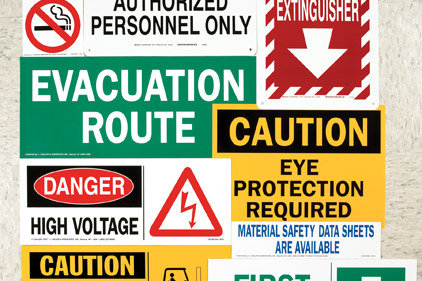
Knowing where these markings are necessary may be a challenge. While you’ll have some site-specific ideas, you’ll also want to review the sign and marking provisions set by OSHA. These are the minimum standards for safety and health, and whether you house auto parts, breakfast cereal or swimming pool chemicals, it’s likely your warehouse has some sign and marking requirements.
Walking-working surfaces
Your permanent aisles and passageways must not only adhere to proper width requirements but, according to 29 CFR 1910.22, they must be “appropriately marked.” Painted lines remain the most feasible method of marking, where practical. However, you can also use other methods, such as marking pillars, powder stripping, flags, or traffic cones or barrels, when vehicle operators and workers are trained to recognize these markings.
In addition, the agency has concerns about overloading storage floor surfaces, including mezzanines. Specifically, your building official must approve load limits for these surfaces and post them on plates in a conspicuous place. If the plates are lost, removed or defaced, you’ll have to replace them.
The ladder is yet another working surface in the warehouse with a marking requirement. Be sure to tag or mark any defective portable wood and metal ladders with the words, “Danger. Do Not Use.” See §§1910.25 and .26 for more information.
Exits
Section 1910.37 is your source for exit sign requirements. Install “Exit” signs using plainly legible letters and keep the line-of-sight to exit signs clearly visible at all times. Look around and ask yourself if the direction to the nearest exit or exit discharge is immediately visible. If not, post signs along the exit access indicating the direction of travel. What’s more, if along an exit access someone could mistake one of your doors for an exit, OSHA calls for you to mark it with a “Not an Exit” sign or with a sign identifying its use, such as “Closet.”
Hazardous materials
Flammable liquids, compressed gases and liquefied petroleum (LP) gases are some of the OSHA-regulated “hazardous materials,” under 29 CFR 1910 Subpart H that may affect your warehouse operation. These, too, come with sign and marking provisions. Check out §1910.106(d)(3), which says that flammable liquids cabinets must be labeled in conspicuous lettering, “Flammable — Keep Fire Away.” Or try §1910.101, which requires in-plant handling, storage and utilization of all compressed gas cylinders to align with Compressed Gas Association Pamphlet P-1-1965. Within the pamphlet you’ll find that the cylinders must bear a Department of Transportation (DOT) label, and signs must be posted in cylinder storage areas, where appropriate, that provide the name of the gas and the phrase, “No Smoking.” Similarly, take a look at §1910.110(c)(2), which says containers of LP gas must be marked in accordance with DOT regulations, but additional markings not in conflict with DOT regulations may be used.
Lockout/tagout
Improper use of lockout/tagout procedures also creates hazards in the warehouse environment, and violations of §1910.147 have been some of the costliest under OSHA jurisdiction. Make sure your tags are durable; standardized by color, shape or size, as well as print and format; and substantial enough to prevent removal without tools. Tagout devices must also indicate the authorized employee using the tag.
Fire protection
Inadequate fire safety protections can spell disaster for a warehouse. If you’re using portable fire extinguishers, mark their location, in accordance with §1910.157(c), so your workers can easily spot them in a fire emergency. Moreover, §1910.158 prescribes that fire hose reels and cabinets be “conspicuously identified.” OSHA does not tell you how to mark the location of extinguishers or hoses in the workplace, but signs and painted or taped pillars, floors or walls are popular methods. Note that any color is acceptable, but according to §1910.144, “Red shall be the basic color for the identification of . . . fire protection equipment and apparatus.” The important thing is to train your employees in whatever method you choose.
Materials handling
The ability to handle materials, moving them from one location to another, is vital to any warehouse. Forklifts, overhead cranes and slings are the typical workhorses of the warehouse, but they too are not without marking provisions.
You’ll want to make sure your forklifts bear appropriate, legible nameplates and markings, in line with §1910.178(a). If you modify a forklift, and this change affects its capacity and safe operation, then you’ll need to not only get the lift manufacturer’s approval to do it, but you’ll also have to adjust the nameplate and markings accordingly.
Similarly, you’ll want to look for the rated load marking on each side of an overhead crane. If the crane has more than one hoisting unit, each hoist has to have its rated load marked on it or its load block. If you cannot clearly read the marking from the ground or floor, it’s not compliant with §1910.179. Pendant control boxes must also have clear control markings. And overhead cranes call for “Warning” or “Out of Order” signs on the crane and either beneath it or on the hook, before you make crane adjustments and repairs.
Slings are one of the most commonly used materials-handling devices. For the protection of the worker, slings must have the manufacturer’s marking, which provides the load capacity and other safety information. According to OSHA§1910.184, you cannot use slings unless these identification markings are legible and affixed to the sling itself, and you cannot load a sling in excess of the load limit recommended on that marking.
Electrical
Don’t overlook electrical markings at §1910.303 and .305. Ensure electrical equipment and disconnecting means are labeled or marked with the intended purpose, unless, in the case of disconnecting means, this is evident. If you have an electrical room with exposed live parts, mark the entrance forbidding unqualified persons to enter. You may be wondering if you should use a “High Voltage” sign on your electrical panels. OSHA says pull and junction boxes for systems over 600 volts, nominal, require a “High Voltage” mark, placed outside the box cover so it’s readily visible and legible; however, it may be a good idea to mark all cabinets, boxes and fittings over 600 volts, nominal, with such a marking. Your local and state codes may also have more stringent provisions.
Hazard communication
The Hazard Communication Standard at §1910.1200 is one of the top-violated OSHA standards for the warehousing and storage industry. Even in work operations where workers only handle chemicals in sealed containers that are not opened under normal conditions, the agency has labeling provisions. If that is the case, it’s pretty simple — ensure that labels on incoming containers of hazardous chemicals are not removed or defaced.
On the other hand, if your employees will have exposure to hazardous chemicals, review all the labeling provisions in paragraph (f) of the standard. Hazardous chemical containers shipped to your warehouse should already have proper labeling, but if a worker transfers chemical into a spray bottle, for example, and doesn’t use it up immediately during that shift, that bottle requires a HazCom label.
While the HazCom Standard does not require carbon monoxide signs, posting them may raise awareness to the exposure in your warehouse. The standard does not require pipe labeling, but other OSHA standards, such as for flammable liquids, §1910.106, and welding, §1910.253, do. Also, check your state and local codes for further requirements.
Final words
Signs and other markings cannot substitute for control measures, personal protective equipment and training, but they are a vital part of any warehouse safety program, providing one more stopgap to injury and illness.
Looking for a reprint of this article?
From high-res PDFs to custom plaques, order your copy today!