Cultivate a safety culture
For starters, what are perceptions of your existing culture?
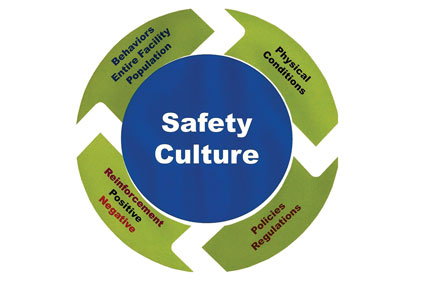
The impact of accidents on companies, employees and their families is substantial. Monumental strides have been made on the technical side of safety, but this has proven to be “not enough”. Behavioral safety has made significant headway in developing safety processes. Identifying, measuring and reinforcing safe behaviors has produced great results. However, before this can be done, there is a very important first step: identifying the “existing safety culture.” A facility’s culture directly impacts what happens in a facility and affects the safety performance of a company.
The culture of a facility is the center of a safety process. Major influences affecting the safety culture include: physical conditions, policies/regulations, behaviors–entire facility population and reinforcement–positive/negative. (See Figure 1)
What is safety culture?
As described in SKYbrary Wiki, “Safety Culture is the way safety is perceived, valued and prioritized in an organization. It reflects the real commitment to safety at all levels in the organization. It has also been described as ‘how an organization behaves when no one is watching’.”1 It could be said that perceptions are not reality, but while perceptions may not be real to some, they are someone’s reality. You must not underestimate the effect of perceptions on the culture and behaviors of the workforce.
What is the importance of safety culture?
If workers’ perception is that organization and management do not really care about safety and behave in a manner that communicates this, workers will act accordingly. When safety is perceived to be prioritized lower than production and quality, workers will take shortcuts, by-passing policies to meet the priorities inferred. Wise professionals know that production and quality rise when safety excels, yet this is often forgotten. Leadership and organizational behaviors are important to the success of any process, setting the example to follow. Workers behaviors often mirror those of management and supervision. Once employees see management and supervision “walk the talk,” they will begin to trust and accept that the culture must change.
Measuring safety culture
The best way to measure the existing safety culture is to conduct a survey of the total facility population. This is best done as an independent study. Internal studies do not have the same effect, especially if the trust level between the organization, management, supervision and primary employees is low. In a typical work environment, trust is a frail commodity at best.
In surveys conducted for our clients, we use a very large sample to raise the confidence level on the results. Surveys are done anonymously to ensure more open and honest responses. When employees sign their name to a document that gives opinions, they often fear reprisals.
The survey should cover all areas and levels of employees within the facility. The sample should not be over-weighted in management, supervision or primary employees. Likewise, no department or area of a facility should be given more emphasis.
Understand that the survey will produce many perceptions. While management might feel they are not based on facts, these answers are what people believe so don’t treat them lightly. You need to address all answers before change can occur.
The survey should include ideas to improve safety. Primary workers are the frontline people who really know what works and what doesn’t. No one knows their jobs better and what makes their performance safe. Their input is critical to reaching a safety culture desired by all.
Share survey results with the entire population. A safety culture survey is for everyone, and the information derived from it should not be kept with a small group using the excuse of “need to know.” All employees need to know.
Once you have identified areas for improvement, involve the entire population in identifying and agreeing on strategies for change. Include communication systems and levels of involvement by all workers in determining the safety culture change components. Involve all employees in drawing up the picture of desired safety culture. Once the parameters of change are identified, develop a road map. This involves training methods, schedules, safety observations, measurement processes and means of communication. Define and assign responsibilities and accountabilities. Form lead and working sub-teams.
People do more of what brings good consequences. Positive reinforcement is an important element missing from many workforce cultures. Statistics show that when workers are positively reinforced, they will go beyond what is expected of them. Every effort should be exerted in reinforcing participation in reaching a “New Safety Culture.”
Even though the initial survey is completed, areas for improvement identified and strategies implemented, plan future surveys to periodically review where the safety culture stands. This will measure the success of change.
Get all involved
Employee involvement and key management leadership are the center of cultural change. Employees have a vested interest in having an effective safety process. They know their jobs and areas they work in better than anyone. Studies show that hourly workers can be very effective and valuable problem-solvers. Solutions can often be developed before engineering gets involved. Research also shows that if people have input to a process or program they are more likely to support it. Management commitment and leadership must happen to help the change of all. The culture will evolve to a desired level by involving the whole population of a facility.
Looking for a reprint of this article?
From high-res PDFs to custom plaques, order your copy today!