“God might give out plenty of gifts, but he doesn’t give away gold medals.” Casey Barrett’s resolute last statement seals his point to his readers in his revealing article about Olympic swimmer Michael Phelps. Mr. Barrett contends that, while Phelps couples talent and a body uniquely built to propel him through the water (abnormally long torso, big feet and hands and short legs), something else helped Phelps achieve 14 gold medals: thousands of training sessions Phelps never missed early on in his swimming career. Day upon day, month upon month and year upon year, Phelps’ coach, Bob Bowman, relentlessly developed this talented young phenom into one of the greatest Olympians ever. Practice, practice, practice and more practice is what created Phelps!
So what does this have to do with safety? Warning! This next paragraph may reveal my inner safety nerd, but hang with me and I’ll answer that question! A chemical manufacturing plant that I have been fortunate enough to visit has achieved the equivalent of a gold medal in the safety world. In this plant, visitors entering the facility for the first time are required to engage in a contractor safety orientation — not just a video but a real orientation! Afterward, visitors are given a badge labeling them “first-timers” to the plant, and this is where the fun begins! Once inside the plant, employees of the plant look out for the newbies and make sure they abide by the safety rules. It’s like Disneyland but safer, well in my warped head anyway. And the facility….so clean and orderly, the machines are guarded completely and forklifts stop and honk their horns. I could go on but hopefully you get the point! If there is a manufacturing safety utopia, this plant may be it.
A few weeks ago I had the pleasure of hearing this facility’s story about their safety developmental transformation. Wouldn’t you know it! Their evolution into a “safety utopia” is much similar to Michael Phelps’ transformation into an Olympic superhero. So, the story goes this plant was never a haven for danger. On the contrary, they’ve always been quite safe and run a clean ship. Thanks to great engineering and management, they were already equipped for safety – expertly built like Phelps. However, at some point the management team at this company decided they wanted to achieve excellence in all facets of their business and they felt like they had to focus first on safety. That’s when they decided to pursue OSHA VPP status, adopt BBS and LEAN Manufacturing. In this way and with these tools, they believed they would achieve higher levels of manufacturing excellence.
With precision structure and tools including VPP, BBS & LEAN, the practice to become safer began. Everyone from the top executive down to the custodian was included in this new safety initiative. All manufacturing processes that made up the recipe of their product were scrutinized with a safety magnifying glass. Unsafe elements inside those processes were plucked out and eliminated. Contractors were required to meet their lofty safety standards or their contracts would be severed. Work performance by employees now included the expectation that you make your job safer and people were held accountable for it. Day upon day, month upon month and year upon year they practiced this standard relentlessly involving all that played a part in delivering the product to market. Safety became core to all they do.
After days, months and years of tirelessly infusing LEAN and BBS into their processes and achieving their OSHA VPP Star recognition, this same chemical plant has become a model of safety and pillar of excellence in their industry. This achievement wasn’t easy. No way… it took practice!
Dedicated, persistent practice propelled both Phelps and the chemical plant to advanced accomplishments. Phelps spent countless hours swimming back and forth across a pool with a stubborn and demanding coach at one end holding an unforgiving stopwatch. My friends at the chemical plant have implemented daily, company-wide participation in prescribed programs fixed with unapologetic safety objectives that influenced all parties involved to drive the business to higher levels of excellence. Both parties continue to achieve the highest levels of excellence in their fields. And, most importantly in the case of the chemical plant, the employees that work at this plant take pride in their work and are dedicated to the business. I know many of them well and they have expressed to me how much they enjoy working at such a dedicated facility.
You may not work at a chemical plant ideally suited for safety but there are always ways to improve through practice. So, implement a new safety mantra: Practice, Practice, Practice! Start practicing today by not taking shortcuts that compromise safety in your work, don your PPE every time, do your job by the book and look out for those around you. Like Phelps, never miss a day of practice. You can do it and you must. Remember, safety greatness comes with practice!
Safety news update: Achieving safety greatness through practice
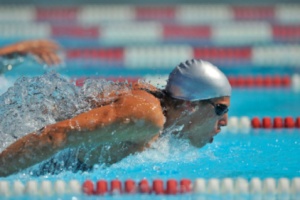
Looking for a reprint of this article?
From high-res PDFs to custom plaques, order your copy today!