Electrical power systems
Maintenance is not an option; it’s a life-saver
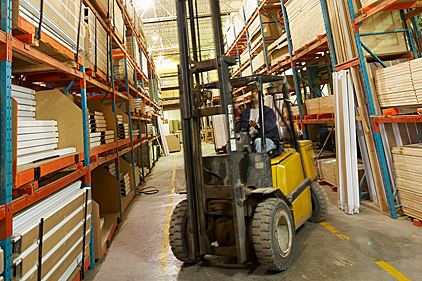
![]() |
Figure 1a and 1b Click here to enlarge image |
NFPA 70B was first published in 1968 and the MTS in 1975. I have used both standards through the years and would refer to each on occasion for maintenance-related questions, but I never considered them safety documents until I considered the effect that the lack of maintenance has on system protective devices. Lack of proper maintenance, as required by these two standards, was such a concern that in the 2009 edition of NFPA 70E several sections and Fine Print Notes (now Informational Notes in the 2012 70E) were added:
• Section 130.5 Informational Note No. 1 – “Improper or inadequate maintenance can result in increased operating time of the overcurrent protective device, thus increasing operating time.”
• Section 200.1(3) NFPA 70E states, “Informational Note: Refer to NFPA 70B, Recommended Practice for Electrical Equipment Maintenance, and ANSI/NETA MTS-2007, Standard for Maintenance Testing Specifications for Electrical Power Distribution Equipment and Systems, for guidance on maintenance frequency, methods, and tests.” The current edition of ANSI/NETA MTS is 2011. This edition was published too late to be included in the 2012 NFPA 70E, which still refers to the 2007 edition.
• In Section 205.3 General Maintenance Requirements, “Electrical equipment shall be maintained in accordance with manufacturers’ instructions or industry consensus standards to reduce the risk of failure and the subsequent exposure of employees to electrical hazards.” This requirement is new to the 2012 edition of NFPA 70E.
• Section 205.4 Overcurrent Protective Devices (OCPD) states, “Overcurrent protective devices shall be maintained in accordance with the manufacturers’ instructions or industry consensus standards. Maintenance, tests, and inspections shall be documented.”
![]() |
Figure 2 Circuit breaker after a restrike event Click here to enlarge image |
These requirements are aimed at protecting personnel from the arc flash hazard. When an Arc Flash Hazard Analysis is performed, the expected exposure to incident energy from an arc flash is based on calculations performed with the assumption that the electrical power system is properly engineered, installed and maintained and that all protective devices are functioning to and calibrated to the manufacturer’s specifications.
The problem
As a facility manager or supervisor, I may be tempted to delay the regularly scheduled maintenance for a couple years or just skip a cycle or two. After all, everything’s going along just fine. Fine unless you consider that many electrical power systems in the U.S. were installed in the 1960s, 1970s and 1980s. Many have been expanded, so there’s some newer equipment, but large parts of these electrical power systems are now 20 years old or older. I’ve seen power systems still in operation using equipment installed in 1911.
An arc flash study bases its incident energy calculations on the voltage, available short circuit current and maximum total clearing (operating) time of the OCPD. If the expected operating time of the OCPD instantaneous function is four cycles (0.07 seconds), as is typical for a 480-volt draw out circuit breaker, the incident energy is based on that operating time.
Consider a scenario where the upstream OCPD does not operate properly (due to lack of maintenance), does not see the fault as a short circuit (because of its settings) or the OCPD has a short-time delay (STD) function. If the OCPD sees the fault as a large overcurrent, the device could take one or two seconds to operate, instead of operating instantaneously. This would be fairly disastrous, subjecting the worker to much higher incident energies than expected. Incident energy is proportional to time, so any increase in the operating time of the OCPD translates into a proportional increase in incident energy received by the worker. If the device has a STD function, there could be up to a half-second delay in operation, even under short circuit conditions. This could cause multiples of its instantaneous operating time and multiples of the incident energy expected. And if the next device upstream also fails to operate, the situation becomes even grimmer.
![]() |
Figure 3 No repair possible Click here to enlarge image |
If one circuit breaker fails due to lack of maintenance, there’s an increased probability that the upstream OCPD in the system could fail as well. Figure 2 shows a power system circuit breaker that suffered a restrike. A “restrike” is where a circuit breaker could not clear a fault and the next circuit breaker upstream must clear it. In this situation, six breakers failed consecutively when an underground 15kV cable faulted. This company was out of production for six days and had to replace the equipment at premium prices and pay overtime to contracted workers.
Figure 3 shows the only alternative for switchgear that has gone through an arc event such as the one depicted in Figure 2 — you tie a cable around it, drag it into the parking lot, and cut it up for scrap. Nothing could be salvaged from the original installation, and all cabling and control circuits had to be reinstalled. This customer paid more than $500,000 just for the equipment and installation.
How maintenance standards can help
For maintenance departments or companies that want to start or improve electrical power system maintenance programs, NFPA 70B is a single-source document that explains it all. It covers such topics as maintenance philosophies; developing an effective maintenance program; personnel safety, which contains excerpts from NFPA 70E; and specific recommendations for all common types of electrical equipment. A section on testing and test methods includes several recommended forms, as well as inspection and testing procedures.
NFPA 70B also contains chapters discussing the maintenance of equipment subject to long intervals between shutdowns, UPS systems, engineering studies, power quality, vibration and grounding. These chapters go into detail about what the issues are and how to evaluate and correct any problems found. In the Annexes, there are sections on recommended maintenance intervals, equipment storage inspection checklists, and equipment maintenance and storage during construction.
ANSI/NETA MTS-2011 works hand-in-hand with NFPA 70B. ANSI/NETA MTS-2011 covers the inspection, maintenance and testing of each component in the electrical power system, as well as the acceptable requirements (both for visual/mechanical inspections and electrical tests) for each component. As a bonus, ANSI/NETA MTS-2011 provides guidance on frequency of maintenance in Annex B in an easy-to-use matrix format.
No accident
Electrical safety is no accident. It takes hard work and constant diligence to have a safe work environment. As an electrical working culture, we have come a long way since the bad days of the 70s and 80s. We have more tools available and employees and employers are becoming more educated about what their responsibilities are and how what we do (or don’t do) can affect safety.
One important missing component has been the proper maintenance and calibration of electrical power systems and their protective devices. Poorly engineered, poorly installed or poorly maintained electrical power systems are a hazard to anyone who works on or near them. An arc flash can injure or kill personnel several feet from the equipment, and as power systems age and are operated to their maximum tolerances, the probability of failure increases. Maintenance is not an overhead item — it is a safety item. NFPA 70B and ANSI/NETA MTS-2011 provide the information you need to make your power system safe to operate or to work on.
Looking for a reprint of this article?
From high-res PDFs to custom plaques, order your copy today!