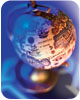
2010 has been a rough year for worker safety; miner deaths in West Virginia made people reexamine the safety of mine workers, then deaths associated with the gulf oil disaster called the company’s preparedness and response to the disaster into question. Many companies large and small are looking at their safety and wondering whether a similar tragedy could befall them. Even as the economy continues to sputter, companies are considering investing in improving worker safety. Unfortunately, not all organizations are ready for a world-class safety system and many will waste their investments.
As organizations grow, their views on worker safety evolve according to where they are in the maturation cycle.
"Keep OSHA out"
Once a company has reached a certain size, it realizes - either because of rising occurrences of injuries and workers’ compensation costs or OSHA citations - that it needs to implement safety policies and rules. Companies in this stage tend to measure safety in terms of OSHA compliance and see safety efforts as a nuisance or a necessary evil. These companies focus on minimal compliance and nothing more. Safety professionals are often little more than the “rules police” and are typically seen as an impediment to business and are generally at loggerheads with operations. Discipline tends to be draconian, and rules are seldom enforced, except after an injury. As rules are ignored, stricter rules with harsher punishments are implemented.
"Frustrated by workers"
The next stage of safety maturation is the carrot and stick stage. In this stage safety is measured in rates and lagging indicators or inappropriate leading indicators. Here companies try to use behavior modification to entice workers into working more safely. These behavior-based safety systems appeal to frustrated operations leadership who are tired of injuries caused because the injured party behaved unsafely.
While these programs can be effective in reducing injury rates, there is growing research that finds that many of these programs force injuries underground as injured workers - whether because they fear discipline for being injured or because they don’t want to be the reason that a safety incentive is withheld - fail to report injuries.
This under-reporting of injuries often results in a false sense of security as the organizations interpret the fall in recordable incidents as indicative of a reduction of risk injuries. Tragically, this often results in unanticipated serious injuries or fatalities that leave the organization at a loss to explain the “freak accident.” Additionally, many companies find themselves funding a larger and more bureaucratic safety infrastructure.
"It's the system, stupid"
Companies with world-class safety systems believe that it is impossible to measure one’s success in terms of injury rates; instead these organizations describe safety in their workplaces as expressions of risk.
World-class safety programs are typically based on a problem-solving philosophy. In this view of safety, injuries are seen as process failures and symptoms of larger process instability, since failure modes across the business spectrum (safety, quality, delivery, cost, moral, and environment) represent unplanned variation into the system.
Organizations that have developed truly world-class safety systems focus on eliminating the system flaws that cause injuries. These organizations recognize that people make mistakes and no amount of behavior modification will change behavior that isn’t cognitive. Safety is hardwired into the organization and is embedded into the core systems of the organization.
World-class safety systems are characterized by these elements:
- Recognition that a critical few hazards represent the majority of the risks of serious injuries.
- Understanding that despite all efforts, the probability of injury - however small - can never be completely eliminated, and efforts to mitigate the severity of injuries that do occur are essential.
- A strategy for prioritizing safety interventions so that resources are allocated to the areas with the highest exposure.
- A robust infrastructure for data gathering and interpretation.
- Solid workflow management to ensure the containment and speedy correction of hazards.
- A relentless desire to improve safety performance.
Barriers to world class
Implementing a world-class safety system takes more than mere desire, and sadly, many organizations may never achieve it. Some of the most common barriers to implementing a world-class safety system include:
- Cost. While organizations with world-class safety systems tend to see expenditures on safety improvement initiatives as investments in business optimization and pursue only those actions with a measurable return on investments, smaller companies may lack the resources to invest. The limited resources of these organizations tend to be used for other, more pressing needs.
- Lack of discipline. Companies that have dysfunctional systems (poor meeting skills, lack of discipline to processes, dysfunctional interaction between departments, etc.) typically are unable to sustain world-class safety systems.
- Will. Weak leadership of less mature organizations does not support or value efforts to implement a world-class safety system.
- Lack of systems. Many companies evolve without viable business systems, and while this may serve them well while they are small, as they grow a lack of formal business systems makes it impossible to become world-class at anything, including safety.
- Widespread process variation. Process variation makes it difficult to consistently produce goods or services for sale and to satisfy your customers. It results in a work environment that is fraught with chaos and unpredictability; these are hardly the conditions for the development of a world-class safety system.
A world-class safety system is necessary for any company to reach its fullest potential and to gain a lasting competitive advantage. Unfortunately, the challenge for some companies to reach this point may prove insurmountable.