SYSTEMS THINKING: Safety & health worst practices
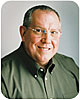
One does not learn from doing something right, but one can, although not necessarily, learn from doing something wrong, by making a mistake.
— Russell L. Ackoff, Ph.D.
For the sake of this discussion, I propose to define the term worst practice as processes, approaches, or activities that have been shown through research, evaluation or experience to be ineffective, inefficient or counterproductive, resulting in undesirable outcomes. Remember, for every best practice there is an equally opposite worst practice.

Unintended Side-effects of
Safety Fixes (Adapted from Carroll 9)
Worst practices Hall of Shame
Some of the foremost reasons individuals commit worst safety and health practices include:Beating the system: Employees who fall into this pattern of behavior believe in the axiom that “if I don’t get caught, I didn’t break the rules.” 1
Behaving unethically: Frequently, safety and health professionals find themselves in “no-win” situations. These “no-win” situations are accompanied by work pressures, peer or supervisor pressure, or offsite pressures.2 Common rationalizations described by Sims, et al. include, since it helps the organization, the organization will condone it and protect me; or it’s in our best interest; or it’s not really illegal or immoral; or, my favorite, no one will find out.3
Failing to learn: Many organizations are afflicted with “organizational learning disabilities.” They fail to learn from others’ accidents and, worse yet, fail to learn from their own accidents, even catastrophic ones.4,5 Prominent examples include NASA’s Challenger accident in 1986, followed 17 years later by the Columbia accident in 2003. In both accidents, the underlying cause was the normalization of risk (i.e., a mindset that partial malfunctions were considered normal).
Andrew Hopkins drives this point home in his comparison of BP’s Grangemouth, Scotland petrochemical plant accident in 2000 and BP’s Texas City Refinery accident in 2005.6 In both cases, investigators stressed the need to emphasize a persistent focus on the application of process safety management.
A caveat: Research in ultra-safe systems (e.g., commercial air travel) has revealed continued elimination of mistakes can paradoxically lead to a decrease in safety.7 The keys to learning from and adapting to existing and past safety and health worst practices is having an organization open to this form of scrutiny and diagnostic analytical tools to systemically assess all aspects of a worst practice.
Diagnosing a worst practice
A number of systems thinking tools can serve to diagnose a worst practice. One such tool is the modeling feature found in System Dynamics.System dynamics is used to describe and dissolve problem behaviors in socio-economic systems through the use of feedback loops, which serve as a framework for dealing with dynamic complexity.8 Marais, Saleh and Leveson have developed safety system archetypes covering most underlying systemic patterns we face when analyzing an accident. These archetypes include:
- Challenges of maintaining safety: Stagnant safety practices in the face of technological advances; Decreasing safety consciousness; Eroding safety goals (i.e., disappointing safety programs not living up to expectations); Complacency (i.e., operations without incidents leading to complacency).
- Side effects and symptomatic responses: Unintended side-effects of safety fixes (i.e., unsuccessful problem resolution); Fixing symptoms rather than root causes; Improperly designed reporting schemes.
- The vicious
cycle of
bureaucracy.
To give you a sense of
a system dynamics model,
take a look at the following model that depicts the
“Unintended side-effects of safety fixes” archetype.
In this archetype, Marais, et al.’s situation involves a plant experiencing an increasing number of equipment breakdowns attributed to poor maintenance practices.10 A typical “fix” for a maintenance problem is to write more procedures (B procedure fix) and disciplining workers (B discipline fix) for non-compliance. The “B” stands for Balancing Loop, which represents moving from a current state to a desired state. These fixes often lead to reinforcing loops (R distrust) and (R complexity), which ultimately leads to making the equipment breakdowns worse. The “R” stands for Reinforcing Loop, which represents action that feeds on itself to produce growth or decline. The unintended side-effects are the workers’ reduction in trust toward management for monitoring their compliance with the procedures, the loss of workers’ motivation to problem-solve on the job and workers’ blind or malicious compliance with procedures even if they are incomplete or incorrect.
One reminder: be sure to expand your search beyond mere proximal causes, such as technical issues or human errors, to include systemic patterns (i.e., root causes and contributing factors) in order to ensure the entire workforce will support and live by the implemented solution.
References
1 Ackoff, R.L. 1999. Re-Creating the Corporation – A Design of Organizations for the 21st Century. Oxford University Press. New York, NY.2 Schneid, T.D. 2008. Corporate Safety Compliance: OSHA, Ethics and the Law. CRC Press. Boca Raton, FL.
3 Sims, R.R., J.G. Veres, K.A. Jackson, and C.L. Facteau. 2001. The Challenge of Front Line Management: Flattened Organizations in the New Economy. Quorum Books. Westport, CT.
4 Hopkins 66.
5 Hale, A., B. Wilpert, and M. Freitag. 1998. After the Event: From Accident to Organisational Learning. Emerald Group Publishing LTD. Bingley, UK.
6 Hopkins 66-67.
7 Amalberti, R. 2001. The paradoxes of almost totally safe transportation systems. Safety Science. 37(2&3):109-126.
8 Marais, K., J.H. Saleh and N.G. Leveson. 2006. Archetypes of organizational safety. Safety Science. 44 (7): 565-582.
9 Carroll, J.S. 1998. Organizational learning activities in high-hazard industries: the logics underlying self-analysis. Journal of Management Studies. 35 (6): 699-717.
10 Marais, et al. 576-577.
Looking for a reprint of this article?
From high-res PDFs to custom plaques, order your copy today!