Loading dock & warehouse safety
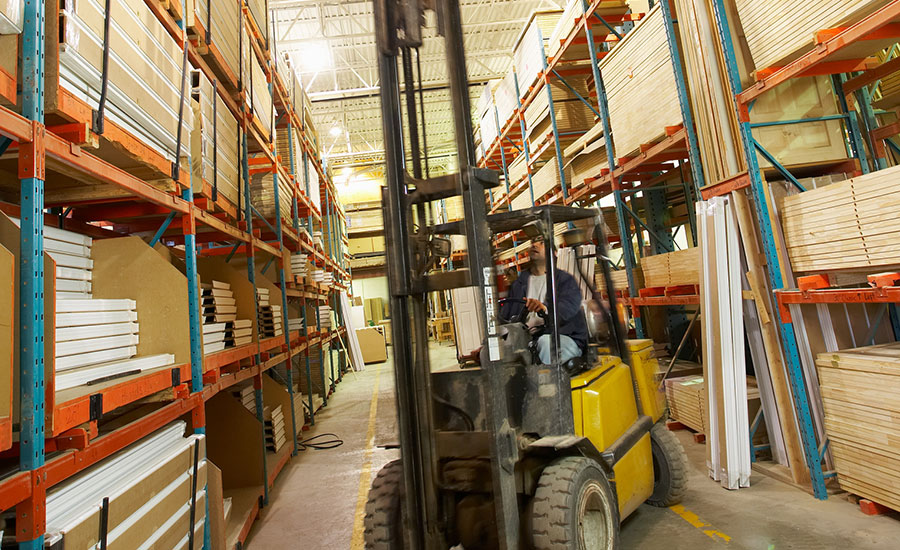
At the dock
Wheel chocks - These need to be available at the dock. They should be secured, with adequate slack, to the building, a stanchion or a similarly solid structure, as they have a habit of "disappearing." Your dock may be equipped with other types of state-of-the-art devices that can be used in lieu of chocks on most trucks. However, these devices may not be adaptable to all vehicles. There should be signs to indicate the requirement to use the chocks, with a second set of signs worded backward for viewing in a rearview mirror.Modified docks - Some companies have installed or modified docks, so that the truck is angled down to the building. In most cases, this should override or reduce the need to rely on chocks. Realize, though, that the steeper the decline, the more chance there is that the truck could slide into the building, or that persons on that surface could slip. There is also the added concern of accumulation of precipitation or leaking vehicle or drum fluid, often necessitating the installation of drains.
Trailer boxes - Your employees should know that they are not required to enter or conduct work in trailer boxes, where flooring integrity is compromised. Trailer boxes should have a suitable level of illumination, most often achieved by articulating lighting fixtures mounted inside the building. Employees should be taught to avoid lingering inside trailer boxes, as carbon monoxide and/or aldehydes from forklift emissions could present a hazard.
Bumpers/cushions - The bumpers/cushions that are mounted/secured on the outside of the building should be periodically checked. If the bumpers are not in place, there is increased risk of structural or other damage to the building. If bumpers are not fairly well aligned with each other, the truck may come to rest in a position whereby angled gaps exist between the vehicle and the wall.
Dock boards - Dock boards (bridge plates) or equivalent devices should be used to span the space between the wall and the truck floor. Portable dock boards should be secured in position by being anchored or equipped with devices (generally vertical dividers) that will prevent their slipping. Further, portable dock boards should be provided with handholds or other means to permit safe handling. Dock boards are addressed in a section of the OSHA standards (1910.30) that is merely labeled "Other Working Surfaces."
Dock bay - OSHA standards require that open-sided floors or platforms four feet or more above adjacent floor or ground level shall be guarded by a standard railing (or equivalent). This, however, is seldom done. The germane height is often just under four feet. Regardless of the height, a hazard still exists, especially with protruding, uncovered docks exposed to the weather elements. Stanchions and chains (preferably with a spring attachment) or other means of perimeter protection should be installed, as serious injuries can be sustained from workers falling off docks. At the least, the edge of the dock should be painted with a bright color. And employees closing or opening doors (by electrical or manual means) should not be positioned too close to the perimeter.
Articulating lights - The flexible, electrical cords on articulating light fixtures often create a safety hazard. The cords are frequently stripped near the plug or where entering a portion of the fixture. This damaged insulation is often at one of the arms. Grommets on these arms are almost routinely missing or not properly seated. Severely dented fixtures are another common problem. Remember that electrical receptacles between or near bays (obviously near the exterior of the building) should be equipped with ground fault circuit interrupters.
In the warehouse
Now to the inside of the building?Forklifts - 1910.178 addresses powered industrial trucks (basically forklifts), which are in frequent operation in loading dock areas. It's smart to revisit these standards. Remember that the hazards of fluid that has leaked from forklifts are exacerbated when in close proximity to an open dock.
Pallet jacks and hand trucks - Too many workplaces overlook the operation of pallet jacks and hand trucks. Even though they are not "powered," training and maintenance are important. Consider that forklifts can be unambiguously differentiated, but not so with pallet jacks and hand trucks. To set up a preventative maintenance program, they should be numbered or similarly marked.
Floors - It may be obvious that floors should be free of pocks, debris, uneven surfaces, slippery conditions and other hazards to walking and vehicle usage. Why then do these hazards still exist? A clean, well maintained floor is vital to warehouse safety.
Debris - Discarded banding wire and other common warehouse debris must not be abandoned where persons or vehicles can inadvertently come in contact with it.
Material handling, storage and housekeeping - Few employers realize that 1910.176 (not just 1910.22) addresses these issues. The specific related hazards, in the vicinity of loading docks, usually include:
- unsafe storage of portable dock boards (where they can be easily displaced);
- congestion and clutter caused by abandoned cartons and other goods;
- impediments to movement through aisles and to exits;
- impediments to extinguishers (generally mounted between bays);
- impediments to disconnects and breaker panels;
- broken pallets; and
- precarious stacking of items on pallets, where sliding, collapsing and toppling must be avoided.
Signage - Signage problems usually exist in warehouses due to visual impediments presented by high racks and the frequently large square footage. Exit signs (with arrows) at the ends of aisles and at major intersections can be extremely helpful. Extinguishers (and sometimes fire hoses) are commonly difficult to locate due to the positioning of the units as well as their signs. The signs for the firefighting apparatus should be easily recognized when looking down an aisle. Bands and/or supplementary signs, high up on columns, further assist employees and firefighters.
Oh, one more thing: never be loaded around a dock!
SIDEBAR: Odds and ends
Other areas of special note regarding loading dock and warehouse safety include:
- Ergonomics - An entire article could be devoted to proper techniques for lifting/pushing/placing/retrieving cartons and loose items. However, for a start, strive for engineering solutions.
- Conveyors - Be aware of cross-over, emergency stops and guarded in-running nip points.
- Rolling step stands - Equip them with locking wheels and railings.
- Charging stations - These are needed for PPE and emergency eye fountains.
- Sprinklers - Make sure there is proper clearance and that they are paint- and dirt-free.
- Material knives - Should be retractable, and users should be trained on proper use of them.
- Racks - Must be secured, with good condition of supports and cushioning of forklift-accessible components.
Looking for a reprint of this article?
From high-res PDFs to custom plaques, order your copy today!