The critical link between sanitation and employee safety
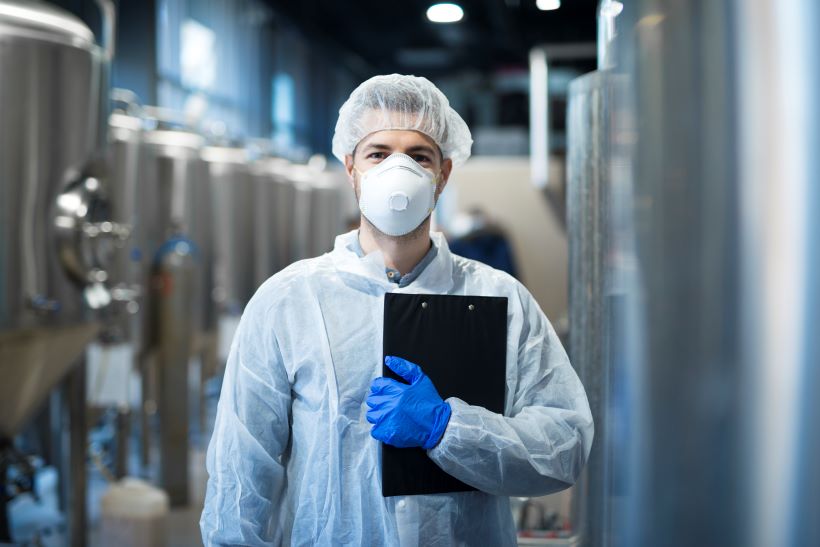
Credit: Getty Images
The link between sanitation and employees’ well-being is more substantial than many industrial sector professionals might assume. Taking preventive action can prevent legal issues, financial losses and insurance complications while navigating workplace illnesses and injuries.
How sanitation and employee safety are connected
Facility sanitation directly affects employees’ physical and mental well-being, as improperly sanitized surfaces can host hazardous contaminants, allergens, chemicals and pathogens.
They also provide breeding grounds for infectious bacteria, toxigenic mold and diseased pests. Staff often contract illnesses or experience health issues after exposure.
Improper sanitation accelerates the spread of infectious diseases, potentially resulting in localized outbreaks. In 2022, private industry companies collectively reported 460,700 workplace illnesses — a 26.1% increase from 2021 — resulting in 2.2 million days away from work. As those figures suggest, employers’ productivity losses were substantial.
In some cases, sanitation-related safety issues result in employee fatalities. The number of preventable workplace deaths totaled 4,695 in 2022, a 5% increase from 2021. Agriculture, mining, warehousing, manufacturing and retail were among the top sectors that contributed to those losses.
An in-depth look at the impact of improper sanitation
Plants that fail to sanitize equipment, workspaces and PPE put their staff’s physical and mental health at risk.
Biological hazard exposure
Bodily fluids are an overlooked biological hazard. Many industrial sector employees will carry on with cuts, burns, runny noses or coughs without considering the consequences. While they may consider it a minor nuisance, it presents issues for upstream production sterility.
Take-home contamination
Staff often unintentionally transport contaminants like lead, infectious agents or arsenic on their hair, clothes and skin. Over time, consistent exposure can make them and their families sick. Since their homes aren’t held to the same standards as their workplace, the hazard will often linger for prolonged periods.
Equipment failure injuries
Contamination and infestations accelerate wear and tear, causing premature equipment failures. Workers operating an improperly sanitized machine risk electrocution, lacerations or burns when it inevitably breaks down unexpectedly.
Infestation-related diseases
Rodents and insects will swiftly take up residence in neglected corners of a plant — including in machinery — because an accumulation of dirt, food residue or grease provides an ideal place to feed and reproduce. In these situations, workers risk bites, stress, allergens and diseases.
Hazardous chemical exposure
Improper sanitation is a hazard many safety personnel overlook. The misuse, overuse or mishandling of cleaning solvents can expose employees to chemicals, potentially causing eye irritation, chemical burns or respiratory problems. Prolonged exposure may result in the development of cancers, weaken the immune system or cause reproductive issues.
Examples of sanitation safety in various industries
In food retail, grease traps can pose safety issues. OSHA issued a hazard bulletin on them in 2020 — workers can be injured if the cover isn’t secured after cleaning. In industrial settings, fatal engulfment hazards are a serious concern.
Proper sanitation procedures protect employees from fume, slip-and-fall and engulfment-related accidents. Also, cleaning a grease trap can extend its life span, minimizing the chance of premature equipment failure — further preventing potential workplace injuries.
In the industrial agriculture sector, workers come into contact with commercial-grade pesticides. If they lack personal protective equipment (PPE) or decontamination procedures, they can bring those hazardous chemicals with them. Over time, their heightened exposure at home and work can accelerate the development of severe or chronic diseases.
Manufacturing is another example of an industry with common sanitation-related wellness concerns. Food residue invites bacterial growth, which turns into biofilm — a community of microorganisms that cling to surfaces — over time. Once one assembly line component is contaminated, it will impact upstream production.
Why companies fall short of sanitation standards
The number of people taking sick leave hit a 10-year high in 2023. The average number of absences totaled 7.8 days, according to a survey of 6.5 million workers. While improper sanitation isn’t the sole driver, it accelerates the rate of disease spread.
Many industrial sector companies fall short of acceptable sanitation standards because they have no culture of safety. Employees — who often lack the necessary oversight to feel compelled to follow through — grow careless or negligent. Instead of keeping their workstations clear and adhering to procedures, they push the responsibility onto others.
Alternatively, staff may feel they have no choice but to fall short of expectations. If they’re pressured to come into work when sick or aren’t given enough time to sanitize before, after and during their shift, they’re more likely to experience a workplace injury or illness.
Management’s role in fostering a safety-first culture
Plant management should foster a safety-first workplace culture to ensure staff consistently meets — and surpasses — sanitation standards.
Leverage sanitation tools
Safety managers should consider supplementing employee-led sanitation efforts with tools since modern technology often outperforms humans. For example, robots can use ultraviolet light to disinfect surfaces, killing viruses, spores and bacteria — all with minimal cross-contamination. Automation and robotics could enhance facilities’ current practices.
Take blanket precautions
Diseases can spread even if staff show no symptoms, so safety managers must take blanket precautions. They should strictly enforce handwashing, glove changing, PPE use and decontamination procedures before, during and after shifts to ensure employees don’t bring any contaminants into or out of the plant.
Enact sanitation policies
Management should enact sanitation-related policies to minimize contamination and foster a safety-first culture. For example, they could offer more sick days or remote work alternatives. After all, private industry companies give sick days to only 51% of their part-time employees and 87% of their full-time workers as of 2023.
Consider overlooked surfaces
Non-product contact surfaces like walls, floors and ceilings quickly become breeding grounds for mold and pathogens if left unattended, so they should be as much of a priority as equipment and workstations. High-touch surfaces like buttons, door handles and levers should get the same treatment, being sanitized at least once per shift change.
Conduct employee training
Frequent training is critical to impart the importance of sanitation among staff. Safety managers should consider covering new, specific topics in depth to be thorough and keep meetings interesting. They can supplement these deep dives with refresher courses. This way, the facility can swiftly adapt to emerging threats.
The importance of proper workplace sanitation
Safety personnel must identify their facility's cleanliness-related shortcomings if they aim to protect staff from diseases, infections and health issues. This way, they can avoid paying out of pocket for medical bills, losing productivity to sick days and losing time going back and forth with insurance providers.
Looking for a reprint of this article?
From high-res PDFs to custom plaques, order your copy today!