A comprehensive guide to combustible dust best practices
Learn how to analyze and identify hazards to protect workers

Industrial manufacturing and production facilities, must provide safe, dry and clean environments, for working occupants, stored equipment, E-commerce goods and products, and utilities. Often, these facilities, create Combustible Dusts and can create problematic, particulate deposits. Combustible Dust, can be suspended in the air, accumulate on top of facility equipment and structures, accumulate on Fire Sprinkler Systems and Sprinkler Heads, migrate and accumulate in Exhaust Fans, Exhaust Hoods, HVAC Air Conveyance Systems, and ductwork, accumulate in Dust Collectors and Dust Bag Filters, and migrate and disperse to other un-suspecting areas, in these facilities.
These types of surfaces and fugitive combustible dust areas can also impact indoor air quality, posing health risks to the occupants. This article describes potential sources of combustible dust and outlines best inspection practices for OSH professionals, certified industrial hygienists and certified remediators to perform the suspect combustible dust inspection.
NOTE: Some of these materials and substrates may also be a source of Asbestos Containing Materials, Lead Based Compounds/Particulates, or Silica Dusts, and OSH and CIH professionals and facility managers will require additional safety precautions when inspecting.
What is combustible dust?
Combustible dusts are fine particles that present an explosion hazard when suspended in air under certain conditions. A dust explosion can cause catastrophic loss of life, injuries, and destruction of buildings. The National Fire Protection Association, (NFPA), states that combustible dust is a finely divided combustible particulate solid that presents a flash fire hazard or explosion hazard when suspended in air or the process-specific oxidizing medium over a range of concentrations. Certain particles, such as fibers, flakes, and agglomerations of smaller particles, may not pass a No. 40 sieve but still have a surface-area-to-volume ratio sufficient to pose a deflagration hazard. In the most recent revisions, the explanatory notes in many of the NFPA standards have moved from a 420 to a 500-micron size threshold.
Sources of combustible dust
When operating, managing, and inspecting buildings and facilities, it is important for OSH and CIH professionals, to be aware of the various sources of Combustible Dust. Potential sources of suspect Combustible Dust will include:
- Food (e.g., candy, starch, flour, corn, spices, sugars, powdered milk, corn meal, cocoa powder, whey, cereal, spices, and gluten
- Agriculture and Grains Wheat, corn, barley, oats, feed, and soybeans
- Biosolids, soap, and pet food.
- Coal and other Carbonaceous Materials Bituminous, sub-bituminous, lignite, charcoal, petroleum coke, and carbon black
- Plastics Resins (e.g., melamine, epoxy, phenolic), polymers (e.g., polyethylene, polyvinyl chloride, polyacrylamide, polyacrylonitrile), and copolymers
- Wood Sawdust and cellulosic dusts, including dust from paper, cardboard, paper towels, facial tissue, and other paper products.
- Chemicals Adipic acid, anthraquinone, dextrin, lactose, paraformaldehyde, sodium stearate, and sulfur.
- Rubber
- Textiles, cotton, and tobacco
- Fertilizers and pesticides
- Pharmaceuticals
- Dyes and Additive Manufacturing (Microfibers)
- Metals (e.g., Alloys, Zirconium, aluminum, chromium, iron, magnesium, zinc, nickel, niobium, tantalum, titanium)
- 3D printing and printing ink
- Fossil fuel power generation
- Polycrystalline silicon, Polysilicon for (solar photovoltaic (PV))
- Nanoparticulates, nanopowders, graphene, graphite, diamond
How is combustible dust produced?
Manufacturing and production facilities equipment and machinery pulverize, mill, grind, crush, macerate, and cut the bulk product. The bulk product may also be released or poured into large vats, vessels, storage tanks, or hoppers. In return, dust is generated and accumulates on all equipment and facility structure surfaces. The fine powder dust, which is suspended on the higher, inaccessible, and unnoticeable surfaces, is the most problematic and the most hazardous, especially when a primary upset or explosion generates a sonic pressure wave that suspends these particles into the path of a flame front (reaction front), causes a devastating secondary dust explosion.
Welding, Shoveling, dumping, loading, Moving, transferring, conveying, tumbling, blending, mixing and drying bulk raw materials, cleaning and scraping mixers and conveyor belts, cleaning dust collector bag houses, Exhausts Ducts and hoods, and Dust Collecting Hoods and ductwork, may produce Combustible Dust clouds. Most types of circulation fans typically stir the dust, adding dust particles into the air and worsening the situation.
The act of broom sweeping, and using compressed air to blow down dust, actually stirs up dust into the air, which may create more issues with sensitive equipment that provides ignition sources, and possible dust explosions.
Walking and Resuspension of Dust from Personal Dust Clouds, can resuspend Combustible Dust, migrate, and disperse to other un-suspecting areas, in facilities. Combustible dust may accumulate throughout a Manufacturing Facility, into unforeseen areas, with air swirls and air currents, mechanical vibration, pressure, HVAC ventilation, and Humidity changes.
Standards for inspecting suspect combustible dust
Assessment protocol for inspecting suspect combustible dust must be developed following the National Fire Protection Association Standard NFPA 652: Standard on the Fundamentals of Combustible Dust, issued in August 2015. The standard provides general requirements for the management of combustible dust, fire, and explosion hazards, and directs the user to reference NFPA 484, 61, 654, 655, and 664 when appropriate. NFPA 652 establishes the relationship and hierarchy between it and the five referenced NFPA standards, ensuring that fundamental requirements are addressed consistently across all industries, processes, and dust types. A key requirement of NFPA 652 is the Dust Hazard Analysis (DHA).
A DHA identifies and evaluates where fire, flash fire, and explosion hazards may exist in the workplace, being a fundamental step in creating a plan to safeguard any facilities from the hazards posed by combustible dust. OSHA does not have an official standard requiring a dust hazard analysis, however, there are OSHA standards for Process Hazard Analysis, and any dust-producing process should include combustible dust risk evaluation in this analysis.
Per OSHA recommendations, an in-depth dust hazard assessment must include the following areas:
- Materials that may be combustible
- Processes that utilize any combustible dust
- Open and especially hidden areas where dust may collect
- Opportunities that may cause dust to become airborne
- Any source of ignition
The key to this hazard assessment is to correctly identify whether or not the dust is indeed combustible. Safety Data Sheets may provide partial information regarding substances fire/explosion hazards; even so, additional laboratory analysis may be required for proper risk assessment and to develop pertinent recommendations, if necessary.
What is a Dust Hazard Analysis (DHA)?
A typical Dust Hazard Analysis will consist of the following:
- Acquire Relevant Documentation. Collection of any available relevant drawings and documents that define the process, equipment, operating parameters, or existing hazards. Examples of this include:
- Process Flow Diagrams (PFDs)
- Piping and Instrumentation Diagrams (P&IDs)
- Mass & Energy Balance
- General Arrangement Drawings (GAs)
- Building Plans
- Equipment Manufacturer Drawings, Data Sheets, Manuals, etc.
- Electrical Hazard Classification Drawings
In such cases where documented information is not available, field investigation is required to document the processes, equipment, and facility to an adequate extent to facilitate the analysis. Plant operations staff can often be interviewed to obtain process data that is not documented. Documenting and understanding the materials involved in the process and their properties at each stage is also a must. Many processes involve changes to a material’s properties such as size, particle size distribution (PSD), and moisture content, which all have a significant effect on how hazardous the dust is. If the dust has been tested to determine properties like Kst (maximum rate of pressure rise), Pmax (maximum explosion pressure), MEC (minimum explosible concentration), etc. copies of the test reports should be obtained and verified that they are representative of the various stages of any process where they might change.
Field inspection to identify hazards & evaluate compliance
Due diligence should be exercised to verify that plant-specific documentation is not out-of-date, incomplete, or lacking undocumented changes for it to serve as an adequate basis for the DHA. A site visit should be conducted to observe current operations, collect necessary data, and ask questions to plant personnel, following general procedures outlined in NFPA 652. Processes and buildings are broken down into individual components. These components are identified on a Process Flow Diagram and referenced as evaluated locations. At each location, information is gathered regarding visible dust suspension, availability of competent igniters, and existing hazard management strategies. This procedure aids in establishing if a hazard exists, under what conditions, and the current degree of hazard mitigation.
The field inspection process is mandated by NFPA 652 and comprises a systematic review and critical thinking about the subject process and facility to identify potential hazards. The focus of the analysis tends to be on dust quantities/concentrations and ignition sources. For each step in the process and area of the facility, the following must be considered:
- Is there, or might there be, enough dust to produce a combustible atmosphere?
- Are there, or might there be, any means to disperse dust in a cloud?
- Are there, or might there be any ignition sources?
Prioritize hazards
Once the hazards are identified, these must be prioritized so that the hazards presenting the greatest risk can be addressed first. A risk matrix is employed to rank the hazards based on the anticipated likelihood that the event could happen and its anticipated severity. Some hazards may require immediate action, while others can be scheduled to be addressed at a future time.
An example of a risk evaluation methodology that might be used during a hazard analysis is the one developed by the engineering and automation company Hallam-ICS. The methodology was adapted from the risk priority number (RPN) calculation used with Failure Mode and Effects Analysis (FMEA). Design failure mode and effect analysis (DFMEA) is a systematic group of activities used to recognize and evaluate potential systems, products, or process failures. This semiquantitative approach can be used to calculate a Risk Level for each hazard, and these scores are used to rank and prioritize hazards for mitigation.
First, the likelihood of an event occurring is determined, and an (L) value of 1 to 4 is assigned based on the guidelines in Table 3.1 – Likelihood (L) Value Guidelines below.
TABLE 3.1 – LIKELIHOOD (L) VALUE GUIDELINES | |
1 |
Extremely Unlikely The presence of a combustible atmosphere and/or a competent ignition source is not expected to be present under any circumstances. |
2 |
Remote The presence of a combustible atmosphere and/or a competent ignition source is only expected to be present during upset conditions. |
3 |
Reasonably Possible The presence of a combustible atmosphere and/or a competent ignition source is expected to be present infrequently during normal operation (i.e. during startup or shutdown) |
4 |
Frequent The presence of a combustible atmosphere and/or a competent ignition source is expected to be present regularly during normal operation |
Similarly, a severity value (S) is determined based on Table 3.2 – Severity (S) Value Guidelines below.
TABLE 3.2 – SEVERITY (S) VALUE GUIDELINES | |
1 |
Negligible No injuries are likely. Minimal disruption to production is expected. |
2 |
Minor At least one lost-time injury is possible. Some disruption to production is expected. |
3 |
Critical Multiple lost-time injuries are possible. Significant disruption to production is expected. |
4 |
Catastrophic At least one fatality is possible. Extended disruption to production is expected. |
The likelihood and severity values are multiplied together to obtain an intermediate value (S x L) as shown in Figure 3.3 – Intermediate Value Calculation below
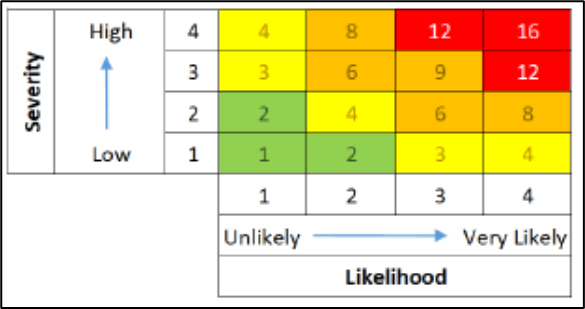
Next, a Detection (D) value is determined based on the guidelines in Table 3.4 – Detection (D) Value Guidelines below.
TABLE 3.4 – DETECTION (D) VALUE GUIDELINES | |
1 | Conditions creating a combustible atmosphere or competent ignition source will almost certainly be detected by sensors or observed by operators such that action can be taken before an incident occurs. |
2 | Conditions creating a combustible atmosphere or competent ignition source are likely to be detected by sensors or observed by operators such that action can be taken before an incident occurs. |
3 | Conditions creating a combustible atmosphere or competent ignition source are not likely to be detected by sensors or observed by operators such that action can be taken before an incident occurs. |
4 | Conditions creating a combustible atmosphere or competent ignition source will almost certainly not be detected by sensors or observed by operators such that action can be taken before an incident occurs. |
The product of the S x L is then multiplied by the Detection (D) value, to determine the final risk level using Figure 3.5 – Risk Level Calculation below.
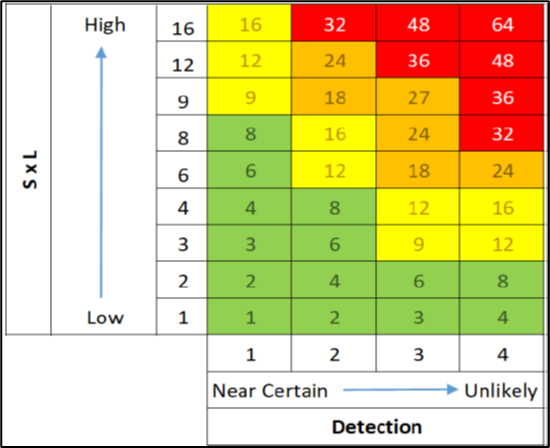
Figure 3.5 above is color-coded by Risk Level for ease of visualization. The color codes correspond to the Risk Levels as defined in Table 3.6 – Risk Level Definitions below.
TABLE 3.6 – RISK LEVEL DEFINITIONS | |
Low No mitigation is necessary. |
|
Moderate Mitigation within 12 months is recommended. |
|
High Mitigation within 6 months is recommended. |
|
Unacceptable Mitigation within 3 months or termination of activity is recommended. |
Ideally, all hazards will be mitigated to the low (green) level. However, some owners may decide that moderate (yellow) risk levels are acceptable under certain circumstances and based on their standards. It is recommended that owners consult with any authority having jurisdiction (AHJ) if they have any doubts or questions regarding acceptable risk levels.
Report Writing. NFPA 652 requires that the results of the DHA be documented. Complete and thorough documentation is necessary when an Authority Having Jurisdiction (AHJ) requests to see the DHA.
Recommendations and best practices, for inspecting sources of combustible dust
Inspecting for suspect Combustible Dust projects and areas, requires an initial plan of action to be implemented. Several recommendations for inspecting sources of Combustible Dust may include:
- Inspect all Production Equipment, Piping, and Ductwork, for sources of Overheating, Sparks, Static Electricity, Clogs and Blockages, Worn parts, and machinery, explosion-proof motors, Anti-Static materials, and hoses.
- Inspect all Dust Collectors, Storage Tanks, Vats, Silos, Tanks, and Conveyor systems, for Combustible Dust accumulations.
- Inspect all plumbing pipes, fire suppression systems, fire sprinkler heads, electrical lines, security wires, and drain pipes, for Combustible Dust accumulations.
- Inspect all HVAC air conveyance units and ductwork for proper operation, calibration, and any air leakage.
- Inspect all Electrical Panels and Connections, Overhead Lighting, Exhaust Fans, and Circulating Fans.
- Inspect all Roof Trusses and Beams, Roof Plenum Spaces, Ceiling Tiles, Fiberglass Batt Insulation, Catwalks, and Mezzanines.
- In addition, NFPA 652 (2019) § 8.7 Inspection, Testing, and Maintenance requires equipment affecting the prevention, control, and mitigation of combustible dust hazards to be inspected and tested per the applicable NFPA standard and manufacturers’ recommendations. The inspection, testing, and maintenance program is required to include the following (if/where applicable):
- Fire and explosion protection and prevention equipment per the applicable NFPA standards
- Dust control equipment
- Housekeeping procedures
- Potential ignition sources
- Electrical, process, and mechanical equipment, including process interlocks
- Process changes
- Lubrication of bearings
These best practices and recommendations for inspecting suspect combustible dust will allow a property owner to have better knowledge, to inspect for suspect combustible dust, in industrial manufacturing properties, and will help prevent secondary damages to these properties. These best practices and recommendations will also allow safe planning and execution of future suspect combustible dust inspections, in industrial manufacturing properties for OSH professionals, certified industrial hygienists and certified remediators.
Sources/References:
- American Chemical Society, ACS Omega 2021, 6, 28, 17831–17838, “Nanometal Dust Explosion in Confined Vessel: Combustion and Kinetic Analysis,” https://doi.org/10.1021/acsomega.1c00967 Published July 10, 2021, Accessed August 11, 2023.
- American Institute of Chemical Engineers, “Dust explosion mitigation using Q-Rohr and exkop,” https://aiche.onlinelibrary.wiley.com/doi/abs/10.1002/prs.680170306 https://doi.org/10.1002/prs.680170306, Published June 17, 2004, Accessed August 11, 2023.
- American Society of Safety Engineers, (Currently the American Society of Safety Professionals), SafelyMade Technical Publication, Volume 1 Issue 3, Pages 4 and 6, HouseKeeping, “Combustible Dust Cleaning, A Professional Approach” https://wp.me/p6HBj6-6c Published 2010, Accessed August 11, 2023.
- Canadian Center for Occupational Health and Safety, C.C.O.H.S), “Chemicals and Materials, Combustible Dust,” https://www.ccohs.ca/oshanswers/chemicals/combustible_dust.html#:~:text=Only%20use%20a%20dust%20collection,air%20and%20worsening%20the%20situation Published June 13, 2023, Accessed August 11, 2023.
- Centers for Disease Control and Prevention, (C.D.C.), “Control of Drywall Sanding Dust Exposures,” https://www.cdc.gov/niosh/docs/99-113/default.html Published June 6, 2014, Accessed August 5, 2023.
- Cloney, Dr. Chris (2022), Dust Safety Science, “2021 Combustible Dust Incident Report - Version #1,” DustEx Research Ltd., Retrieved from https://dustsafetyscience.com/2021-report-summary/ Published 2022, Accessed August 11, 2023.
- Cloney, Dr. Chris (2023), Dust Safety Science, “2022 Combustible Dust Incident Report - Version #1,” DustEx Research Ltd., Retrieved from https://dustsafetyscience.com/2021-report-summary/ Published 2023, Accessed January 3, 2024.
- Elsevier Ltd., Building and Environment, Volume 143, 1 October 2018, Pages 513-522, “Contribution of metals in resuspended dust to indoor and personal inhalation exposures: Relationships between PM10 and settled dust,” https://www.sciencedirect.com/science/article/pii/S0360132318304529 Published October 1, 2018, Accessed August 11, 2023 https://doi.org/10.1016/j.buildenv.2018.07.044
- Elsevier Ltd., Journal of Cleaner Production, Volume 295, 1 May 2021, 126488, “Experiments and simulations of human walking-induced particulate matter resuspension in indoor environments,” https://www.sciencedirect.com/science/article/abs/pii/S0959652621007083 Published May 1, 2021, Accessed August 11, 2023 https://doi.org/10.1016/j.jclepro.2021.126488
- Elsevier Ltd., Atmospheric Environment, Volume 89, June 2014, Pages 464-481, “Walking-induced particle resuspension in indoor environments,” https://www.sciencedirect.com/science/article/abs/pii/S1352231014001319 Published June 2014,, Accessed August 11, 2023 https://doi.org/10.1016/j.atmosenv.2014.02.035
- Hallam- ICS, (Dust Hazard Analysis, Tables and Charts attached to this article): https://www.hallam-ics.com/sample-dust-hazard-analysis-report Published January 2023, Accessed January 2024.
- National Fire Protection Association, (N.F.P.A.), “NFPA Glossary of Terms,” https://www.nfpa.org/~/media/Files/Codes%20and%20standards/Glossary%20of%20terms/glossary_of_terms_2021.ashx Published March 30, 2021, Accessed August 11, 2023.
- National Fire Protection Association, (N.F.P.A.), “652 Standard on the Fundamentals of Combustible Dust,” https://www.nfpa.org/codes-and-standards/6/5/2/nfpa-652 January 2019, Accessed January 2024.
- National Fire Protection Association, (N.F.P.A.), “654 Standard for the Prevention of Fire and Dust Explosions from the Manufacturing, Processing, and Handling of Combustible Particulate Solids,” https://www.nfpa.org/codes-and-standards/all-codes-and-standards/list-of-codes-and-standards/detail?code=654 January 2020, Accessed August 11, 2023.
- National Center for Biotechnical Information, National Library of Medicine, PubMed Central, “A comparative study of walking-induced dust resuspension using a consistent test mechanism,” https://pubmed.ncbi.nlm.nih.gov/24605758/ Published 2014 Dec;24(6):592-603. doi: 10.1111/ina.12107. Epub 2014 Apr 9, Accessed August 11, 2023.
- National Center for Biotechnical Information, National Library of Medicine, PubMed Central, “Potential Explosion Hazard of Carbonaceous Nanoparticles: Screening of Allotropes,” https://www.ncbi.nlm.nih.gov/pmc/articles/PMC4959120/ Published Combust Flame. 2016 May; 167: 218–227. doi: 10.1016/j.combustflame.2016.02.010, Accessed August 11, 2023.
- National Center for Biotechnical Information, National Library of Medicine, PubMed Central, “Understanding the pathogenesis of occupational coal and silica dust-associated lung disease,” https://www.ncbi.nlm.nih.gov/pmc/articles/PMC9724915/ Published online 2022 Jul 13. doi: 10.1183/16000617.0250-2021, Accessed August 1, 2023.
- U.S. Chemical Safety Board, (C.S.B.), and Hazard Investigation Board, “Call to Action: Combustible Dust,” https://www.csb.gov/assets/1/20/call_to_action_-_final.pdf Published October 24, 2018, Accessed August 11, 2023.
- U.S. Chemical Safety Board, (C.S.B.), and Hazard Investigation Board, “Combustible Dust Safety,” https://www.csb.gov/assets/1/6/csb_cdl_fact_sheet_-_combustible_dust.pdf Published April 2018, Accessed August 11, 2023.
- U.S. Chemical Safety Board, (C.S.B.), and Hazard Investigation Board, “Dust Incidents 2006-2017,” https://www.csb.gov/assets/1/17/csb_dust_incidents.pdf?16406 Published October 2018, Accessed August 11, 2023.
- U.S. Department of Labor, Mine Safety and Health Administration, PROGRAM POLICY LETTER NO. P13-V-11, “Program for Regular Cleanup and Removal of Accumulations of Coal and Float Coal Dust, Loose Coal, and Other Combustibles,” https://www.msha.gov/p13-v-11 Published December 18, 2013, Accessed August 11, 2023.
- U.S. Department of Labor, Occupational Safety and Health Administration, (O.S.H.A.), “Combustible Dust in Industry: Preventing and Mitigating the Effects of Fire and Explosions,” https://www.osha.gov/publications/shib073105 Published November 12, 2014, Accessed August 11, 2023.
- U.S. Department of Labor, Occupational Safety and Health Administration, (O.S.H.A.), “Classification of Combustible Dusts under the Revised Hazard Communication Standard. [1910.1200; 1910.1200(d)],” https://www.osha.gov/laws-regs/standardinterpretations/2013-12-27#11 Published December 27, 2013, Accessed August 11, 2023.
- U.S. Department of Labor, Occupational Safety and Health Administration, (O.S.H.A.), “Hazard Communication Guidance for Combustible Dusts,” https://www.osha.gov/sites/default/files/publications/3371combustible-dust.pdf Published OSHA 3371-08 2009, Accessed August 11, 2023.
- U.S. Department of Labor, Occupational Safety and Health Administration, (O.S.H.A.), OSHA Notice “DIRECTIVE NUMBER: TED-01-00-015 SUBJECT: OSHA Technical Manual – Section IV, Chapter 6, Combustible Dusts,” https://www.osha.gov/sites/default/files/otm_secIV_chap6.pdf Published February 10, 2020, Accessed August 11, 2023.
- Wikipedia, Wikipedia Foundation Inc., “Ohmmeter,” https://en.wikipedia.org/wiki/Ohmmeter Published July 28, 2023, Accessed August 5, 2023.
- Wikipedia, Wikipedia Foundation Inc., “Dust Explosions,” https://en.wikipedia.org/wiki/Dust_explosion Published June 27, 2023, Accessed August 5, 2023.
- Zheng, S., Du, W., Zhao, L. et al. Effect of Relative Humidity on Resuspended Particles Caused by Human Walking. J. Shanghai Jiaotong Univ. (Sci.) 25, 365–371 (2020). https://doi.org/10.1007/s12204-020-2176-1
Looking for a reprint of this article?
From high-res PDFs to custom plaques, order your copy today!