Compliance at heights: Fall Protection equipment inspection and recertification
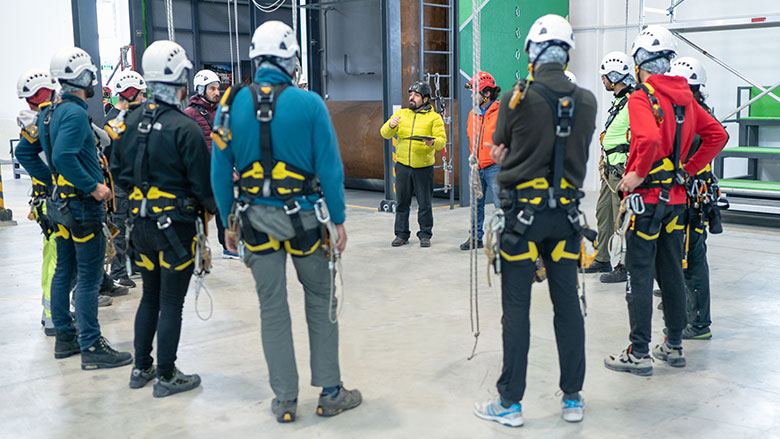
Getty Images
In the challenging field of work-at-heights, compliance with inspection and recertification standards isn’t just about ticking boxes — it's pivotal for ensuring worker safety and organizational resilience. Are you fully in the loop about these vital regulations?
Understanding fall protection inspection standards
Let’s examine the different inspection standards that are fundamental for maintaining equipment integrity and ensuring worker safety:
Pre-Use Inspections: Before each use, fall protection must be inspected for wear, damage, or defects. The meticulous eye of the user can catch immediate risks, making this step non-negotiable for every equipment piece, every time.
Annual Inspections: All fall protection equipment must undergo comprehensive annual inspections. Professionals review these devices for signs of stress, wear, and functionality, thus ensuring their readiness for the year ahead.
Semi-Annual Checks in California: In the State of California, the Code of Regulations requires an even tighter schedule, with inspections mandated every six months. This heightened frequency aligns with the state’s strong commitment to worker safety.
Suspended Access Anchorage 10-Year Recertification: For suspended access equipment, the inspection timeline stretches longer. Every ten years, anchorage for such devices requires recertification, a process steeped in thorough assessment and evaluation.
While inspections are crucial, documentation is an often neglected yet essential aspect of the overall process.
Documentation matters
Many organizations lack proper documentation for their fall protection equipment. This oversight isn't just administrative but poses significant risks some may not be aware of. Here’s why documentation matters:
Equipment History: Documentation outlines fall protection service history, prior inspections, repairs, and overall condition. Without this data, it’s difficult to assess the equipment's reliability and compliance status which can lead users to make uneducated decisions about the safety of a piece of equipment.
Cost Implications: Lack of documentation can lead to immediate expenses from urgent repairs or replacements, leading to hidden costs and potential downtime and delays. Decisions made without historical data not only incur unexpected expenses but also risk compromising long-term safety and compliance.
Compliance Assurance: Thorough documentation is fundamental to ensuring that fall protection equipment adheres to strict compliance standards. It serves as tangible proof of compliance, thereby safeguarding organizations from potential legal and financial ramifications linked to non-compliance.
The above requires a commitment to thorough record-keeping from the beginning. Adopting a systematic approach to documentation ensures a traceable history for every equipment piece. Such proactive documentation practice eases the inspection process and fosters informed decision-making, safeguarding both employees and organizational assets.
Looking for a reprint of this article?
From high-res PDFs to custom plaques, order your copy today!