Six ways to improve warehouse safety when you’ve got moving machinery on deck
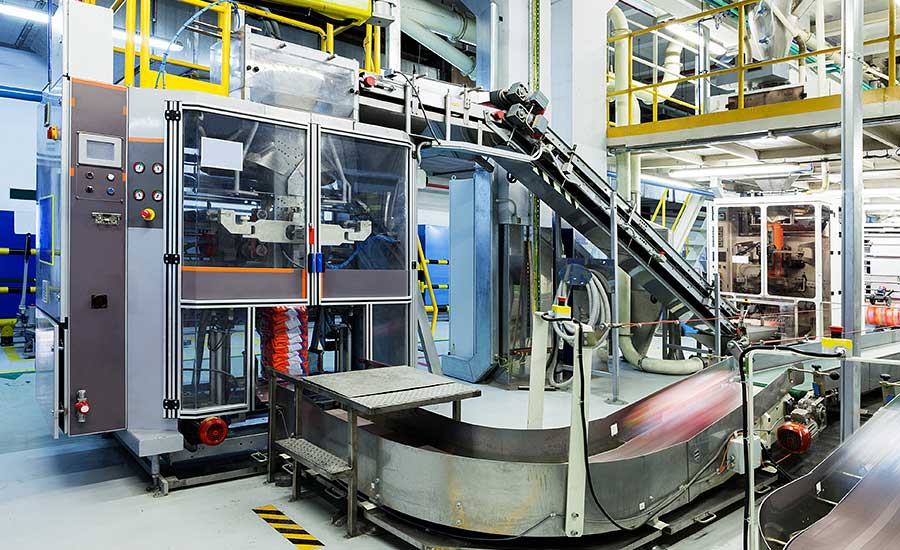
Nowadays, nearly everyone orders online and receives a package within a day or two. But how many of us stop and think about the man-hours and processes that have moved in sync to make this fast delivery possible?
The rapid growth of e-commerce and the expansion of global sourcing has seen an increased demand for labor, which is in short supply. Companies are struggling to meet deadlines, and workers are being tasked to do more. Increasing automation helps the process but brings forth its risks — worker safety in warehouses with moving machinery and loading equipment does take a hit. According to the National Safety Council (NSC), the total cost of work injuries in 2020 was $163.9 billion.
It is essential to ensure the safety of workers and equipment in warehouses. The US Bureau of Labor Statistics reported 16 fatalities per year on average in the U.S. warehousing sector and an injury and illness rate of 5 out of every 100 warehouse workers.
The Occupational Safety and Health Administration (OSHA) monitors worker safety in warehouse operations. It does not have any separate regulations for warehouse safety but they are regulated under the broader standards for general industry in 29 CFR 1910. OSHA issued 454 citations worth $1.8 million to warehouses and storage facilities between October 2020 and September 2021.
Modernization of warehouses and inherent risks and challenges
Warehouses are prone to injury risks. Some common causes of warehouse accidents include fall hazards from spills, uneven surfaces, or obstructed walkways, accidents involving forklifts, loading machinery, repetitive motion injuries, vehicle collisions, and fire and explosions from flammable materials.
Equipment like autonomous forklifts, vehicles, and robots increase efficiency gains, but accident risks also rise.
Traditional autonomous equipment, such as pallet movers and material transport cars, are confined to fixed paths—today's automation technology utilizes the most efficient path based on the real-time location of obstacles. And this can lead to collisions.
Also, the e-commerce boom has led to storage woes. Amazon recorded a 20% increase in injury rates between 2020-2021. Overall, workers at its facilities suffered 400,000 injuries.
In 2019, Target employees expressed concerns that labor shortage due to cuts in backroom storage workers had led to more injuries for workers on the job.
Tips and suggestions for a safe warehouse environment
A warehouse is a complex place where man and machine have to work in harmony for optimal performance. To minimize the risk of injury, employers should implement safety programs that include regular training, equipment maintenance, and inspections to identify and address hazards.
Workflow and workload changes
Proper training in safety measures and engagement of workers is recommended. Otherwise, it can lead to accidents from fatigue and loss of concentration.
The U.S. Bureau of Labor Statistics or BLS reports that overexertion; contact with objects or equipment; slips, trips, and falls account for more than half of all nonfatal injuries and illnesses involving days away from work.
Behavioral-led safety changes
This stems from the idea that most accidents are caused by human behavior rather than equipment failure. Hence companies need to implement strategies that focus on the workers to improve safety in a specific environment or situation. These changes can include safety training and education, positive reinforcement and incentives, and a culture of cooperation and trust between the management and workers.
Attracting the right talent
The storage and logistics industry is undergoing a crisis. The new generation of workers does not find logistics work attractive or lucrative. There is a dire need for a trained collar force due to the introduction of new technology and automation. It is estimated 2.1 million critical jobs will remain unfilled by 2030.
To find the right mix of supervisory experience and technical know-how, employers should follow a multifaceted approach.
Need for safety protocols and processes
There are several risks in a warehouse with moving machinery and heavy equipment. A comprehensive safety protocol can minimize human errors:
a) Follow warehouse safety standards under OSHA protocols
b) Have in-house safety plans that include training and strategies to follow along with an emergency exit plan
c) Warehouse safety checklists and safety drills should be done regularly
d) Preventive maintenance of equipment should be done. The warehouse surfaces should be foolproof and designed to prevent slips, trips, spills, or uneven surfaces. Forklifts, pallet jacks etc., should be adequately maintained and handled. Proper PPE kits should be provided wherever needed.
Digital safety management systems
Going digital in safety management leverages machine learning to identify hazards and respond. These are designed to help organizations manage safety-related data. The systems provide real-time monitoring and alerts, as well as generate reports and analysis to help identify trends and areas for improvement
Communication and information
Safety standards and signs should be posted everywhere. Clear and consistent communication between management, supervisors, and workers can ensure awareness of the potential hazards of working with heavy-loading machinery and equipment. It can also help with incident reporting and investigations, allowing for timely intervention and correction of safety issues
Conclusion
A safe environment should be inherent to a company's philosophy, enabling workers to perform efficiently. Workplace injuries do not only harm a person but have larger consequences for the family, the co-workers, and the company.
Overall, implementing and regularly reviewing safety measures can help prevent accidents and injuries and ensure the safety of employees and visitors.
Looking for a reprint of this article?
From high-res PDFs to custom plaques, order your copy today!