Learn the value of valve safety trains
Avoid equipment explosions
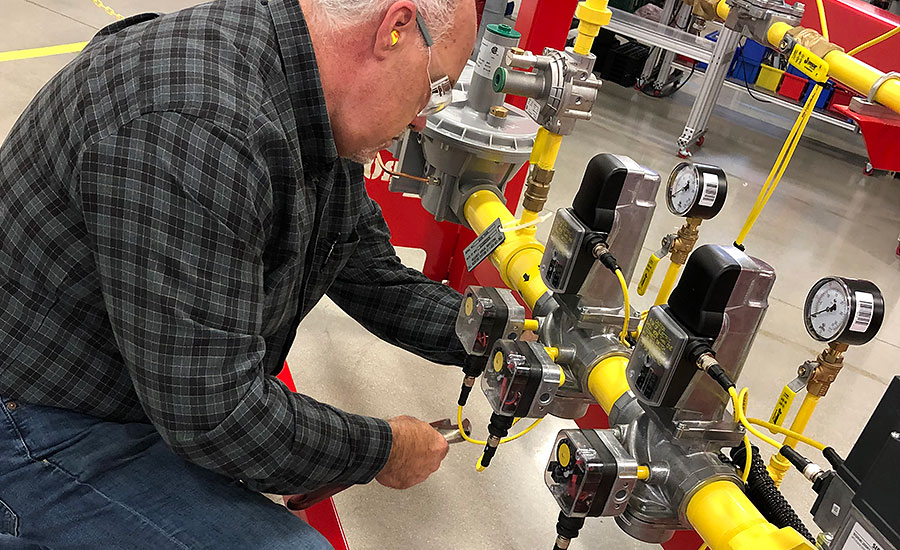
Does your manufacturing facility have a smoke stack? If it does, your facility also likely contains a valve safety train, commonly known in industrial circles as a “gas train” or a “fuel train.” This complicated series of piping and components requires annual inspections, accurate recordkeeping, and preventive maintenance to avert serious safety and productivity issues.
If you aren’t sure what a valve safety train is, you’re not alone. Combustion safety systems are commonly one of the most misunderstood pieces of equipment on the plant floor. As a result, the valve safety train rarely receives the consideration it should from safety professionals.
Control the ratio of fuel and air
It isn’t necessary for a safety professional to know every engineered component of a valve safety train, but you should be aware of what it does and why it demands your organization’s attention. Essentially, a valve safety train controls the flow of fuel into thermal processing equipment. By controlling the desired ratio of fuel and air, the connected burner then properly oxidizes the mixture, safely releasing the energy needed to heat your furnaces, boilers, HVAC heaters, thermal oxidizers and other equipment. In turn, the thermal process equipment performs critical production tasks such as drying gypsum boards, roasting and baking foods, heat-treating metals, fluid heating, and pollution control.
Owing to the presence of hazardous vapors and gases, poorly designed or inadequately maintained trains have led to catastrophic explosions, fires, asphyxia and burns, multi-million dollar loses, injuries and fatalities. A recent study of equipment explosions over the last decade discovered more than 20 incidents that resulted in nearly 50 injuries and fatalities. Thankfully, you can significantly reduce the potential for accidents by asking your plant manager these five simple questions:
1) Does the valve safety train receive an annual inspection?
The entire combustion safety system must be inspected at least annually to ensure compliance. NFPA 86 standards provide guidelines to establish these measures, stating, “The user has the responsibility for establishing a program of inspection, testing, and maintenance with documentation performed at least annually.” This applies to both new installations and modifications.
Annual testing is typically required by insurance agencies, but other (often overlapping) codes and standards may need to be adhered to beside NFPA, for example, ANSI, ASME, NEC, and the EPA. Oil-fired burners must comply with UL-296 Standard for Oil Burners, UL-726 Standard for Oil-Fired Boiler Assemblies, or UL-2096 Standard for Commercial/Industrial Gas and/or Oil-Burning Assemblies with Emission Reduction Equipment.
If your organization does not possess the expertise, a qualified contractor can perform annual inspections. The contractor will test, assess, maintain, and replace necessary components of the gas train, giving your organization a system that is code compliant. In addition, accurate recordkeeping by both the contractor and your maintenance team will allow you to follow trends in train performance.
2) Is the combustion system being correctly purged?
A purge cycle ensures that flammable vapors or gases that might have entered the equipment are cleared. This is important to make sure conditions are safe before intentionally lighting the fuel. Three basic requirements must be satisfied: combustibles feeding the process have been isolated; purge airflow is maintained; and purge time is completed.
Interlocked safety switches on the valve safety train ensure fuel is not entering the system when off. Purge airflow may be verified by using a flow-metering device or by measuring a fixed drop in pressure. The final requirement is verifying the purge timer, which is set for the time it takes to clear the system of combustible mixtures. The purge time is determined by the volume of the equipment and is at least four system volumes. Controls continuously monitor the purge airflow and timing. If anything is interrupted, a restart and a new full purge must be performed.
3) Are any safety components missing?
Valve safety trains are complex and comprised of a series of components, each dependent on the last. Even the most basic combustion safety system will feature safety shut-off valves, manual shut-off valves, high- and low-pressure switches, pressure taps, and in-line strainers. Add to this regulators, valve leak-test systems, diagnostic gauges, and pilot accessories and you quickly recognize the potential for missing parts either by design or accident. Your plant manager’s maintenance records should indicate if alterations to the original equipment were made.
The sediment trap is one frequently missing component of the valve safety train. Sediment traps should be installed beneath incoming vertical drops to capture large debris and pipeline condensate. Sediment traps effectively prevent contaminants from getting into the gas safety equipment and are required by NFPA, but many manufacturers do not include them unless specified.
Gas-pressure switches are another frequently non-compliant device. Found in pairs, these switches monitor and ensure the fuel pressure remains within a safe operating window. Often though, these switches are bypassed, improperly set, or incorrectly installed.
An untrained maintenance team member may inadvertently bypass or adjust a switch to get equipment running immediately. Switches that are bypassed or set to impossible pressures provide no protection whatsoever. And these switches must be electrically sealed to preclude explosive vapors from flowing backwards through the wiring system.
4) Is the valve train vented or ventless?
Unless valve safety train components are listed as “ventless,” vent lines are necessary. Simply installing vent piping is often insufficient. Vent lines must be correctly engineered, installed, and routed to appropriate and approved locations to be effective. Even when vent lines are properly installed, building pressures can vary sufficiently that may prevent optimal burner performance. Vent pipes have also been known to fill with spiders, bees and other nesting insects. Once plugged, the pipes will impede the escape of gasses, leading to a potentially combustible gas build-up inside the facility.
In short, vent lines are another potential failure point. Vents must be inspected regularly by maintenance staff for leaks or blockages. When given the choice, always go with ventless components.
5) Are emissions being controlled?
Emission compliance is a major focus in many industries and geographical regions, such as California. Is your plant compliant with the appropriate regulations? If not, agencies may issue hefty fines or shutdown production completely until modifications are made. Sometimes, a simple burner tuning will ensure a system operates within requirements. At other times meeting new Environmental Protection Agency (EPA) or revised local requirements necessitate modifications to existing valve safety trains, since installing a low NOx burner often creates the need for improved fuel-control too.
Summary
Learning about and acting upon the potential dangers of valve safety trains and scheduling annual inspections helps reduce risks and improve safety in your organization. Find the valve safety trains in your plant and have a look at them. Can you find evidence of inspection, such as documentation, stickers in the control box or other supporting paperwork? Do the shut-off valves have fittings for testing? Or are they fitted with dirty and corroded test plugs? If you cannot find evidence of a recent annual inspection, do not risk becoming a statistic. Instead, have a conversation with your plant manager or maintenance team lead.
Looking for a reprint of this article?
From high-res PDFs to custom plaques, order your copy today!