NFPA 70E’s focus on preventing human error
All about human performance, error precursors & risk
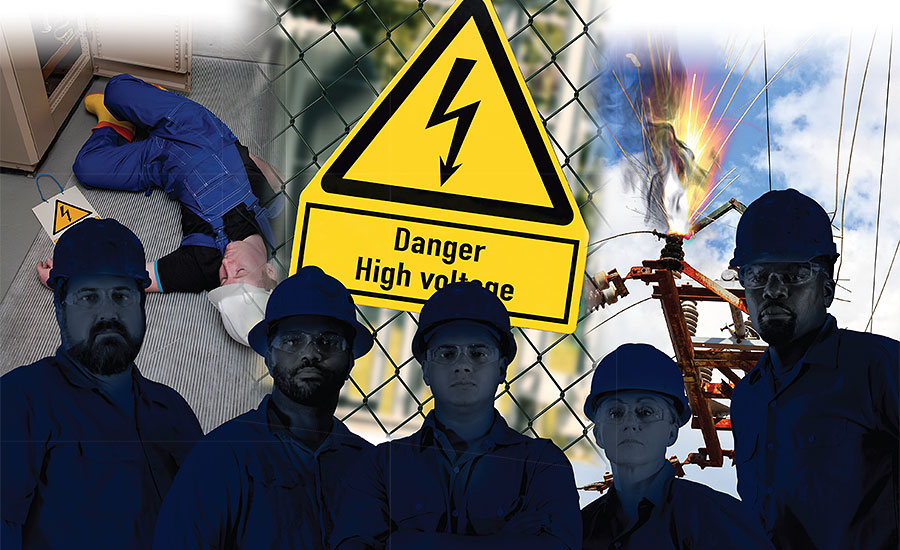
The 2018 print edition of NFPA 70E Standard for Electrical Safety in the Workplace® is 104 pages. Updated every three years by the 70E technical committee, this comprehensive standard covers the latest information about the effects of shock, arc flash, arc blast, and direct current (dc) hazards, and recent developments in electrical design and personal protective equipment.
NFPA states that “the standard continues to evolve to address risk assessment and introduces human factors, such as human error, as part of that assessment. Annex Q, Human Performance and Workplace Electrical Safety, is included to provide (non-mandatory) guidance.
NFPA 70E 2018 is in effect bringing human performance, human factors and preventing human error to “the masses.” Its specific audience is the electrical industry, but human performance concepts, definitions and tools in Annex Q can be used by any organization in any industry.
“Workers, supervisors, managers and VPs can all have human performance issues,” says Mike Doherty, an electrical safety consultant and contractor who works with the electrical safety training and consultancy company e-Hazard. “Everybody has human performance issues at times. This standard is the tip of the spear. In time, everyone will be working far more comprehensively with human performance concepts and tools.”
Coming soon
In fact, the next update of the ANSI-ASSP Z10 standard on occupational safety and health management systems will include material on human performance, also called “the New View of Safety” and “HOP – human and organizational performance.” ASSP, the American Society of Safety Professionals, and the National Safety Council have launched educational programs on human performance.
“Everyone is all over it”
Human factors and human performance with the aim of preventing human error has its roots in three high-risk industries: health care, nuclear power (originally nuclear-powered submarines) and aviation. This aspect of managing safety and health certainly is applicable to high-risk electrical work, with its potential for serious injuries and fatalities (SIFs) due to electrocution, shock, arc flash and blast incidents and severe burns. Its use in the electrical utility industry has “exploded,” says Doherty. “Everyone is all over it.”
The question is: are “the masses” ready for the type of human performance principles and tools contained in 70E 2018’s Annex Q? ISHN interviewed numerous electrical safety and human performance experts, and most answered “no,” with the caveat that, “You have to start somewhere” and Annex Q is but the first of the standards that will raise awareness of the potential for human performance/human factors to prevent near-misses, errors, and SIFs.
The human factors gap
In 2019, the unwieldy “package” of human performance-human factors-human error-HOP-the New View-Safety II principles, terminology and tools bifurcates the professional safety and health community. A number of multinationals and high-risk enterprises wrestling with continuing serious injuries and fatalities despite their world-class safety and health management systems, are “all over it.” But most professionals are uninitiated or perhaps just beginning to catch on. Here’s what we heard from experts:
- David Varwig, a human performance improvement (HPI) specialist, has given several recent HPI presentations. At one, he says “questions were surprisingly low. It must have been somewhat overwhelming, especially the concepts and terminology.” Another session he says was sparsely attended, in part “because there is no compelling urgency to learn more about something that most people don’t even know what it is.”
“At major conferences, human performance workshops, speeches and sessions are not very well attended,” says Rob Fisher, president of Fisher Improvement Technologies. “Often the only people who are there are the ones who are already trying to use the concepts.” - “Many of my plant level clients have not purchased 70E 2018 and have not read Annex Q,” says industrial hygiene and safety consultant Dan Markiewicz. “Their response is mostly muted. They do electrical and arc flash training, label boxes, integrate lockout-tagout procedures, and require arc flash-rated PPE. That seems to be enough. I don’t expect much movement from my clients.”
- “Small electrical contractors, respectfully, don’t have anything to do with 70E,” says one electrical safety expert. “You have one owner, maybe four or five guys, they’re working 14 hours a day, seven days a week, 20-percent of their clients won’t pay up. They’re certainly not looking at human performance and 70E.”
- “Human factors is a bridge too far for almost all the folks,” says consultant Ed Perz of Perz Consulting. “I’ve had investigators reluctant to use human factors for better causation determination because they were confused and found the forms and checklists intimidating.”
- “You can’t just decide today you’re going to implement HOP,” says ORCHSE Strategies consultant Rich Fairfax, a former high-ranking, longtime OSHA official. “It is a long and a slow process. Small businesses and contractors are completely driven by the bottom line. In my experience, most look at safety and safety culture as affecting their bottom line and it’s not something they want to deal with – until there is an accident.”
Defining human performance
Very briefly, this is what many businesses and safety and health professionals are missing out on. NFPA 70E 2018’s Annex Q defines human performance as risk management that addresses organizational, leader and individual performance as factors that either lead to or prevent errors and their events. The goal is to identify and address human effort and its negative consequences.
Basic principles of human performance outlined in Annex Q (which some HP experts believe are outdated) are:
- People are fallible; even the best people make mistakes.
- Error-likely situations are predictable and preventable.
- Individual performance is influenced by organizational processes and values.
- People achieve high levels of performance through encouragement and reinforcement by others.
- Incidents can be avoided by understanding the reasons for mistakes and apply lessons learned from past incidents.
Information processing
Now here’s where Annex Q, and the entire HP-HOP-HF-SIF model gets complicated. Following the five principles, Annex Q gets into information processing and attention, how the brain processes information in a series of interactive stages. Where and to what we intentionally or unintentionally direct our concentrations. Sensory inputs. Encoding, storage and thinking. And retrieval and acting based on the synthesis of attention, encoded information, thinking and decision-making. Annex Q here references material from the 1980s and 90s, which some experts find outdated and even misleading.
Performance modes
Human performance modes and associated errors are next taken up in Annex Q. Humans operate either by the rules, (rules-based mode), by their own knowledge (knowledge-based mode), or by the use of very familiar skills (skills-based mode). Errors in these modes can include misinterpreting rules, decision-making based on incomplete or inaccurate information, inattention to applying skills, and as familiarity with a task increases, perceptions of risk decrease.
Error precursors
Annex Q next addresses error precursors, dividing them into task demands, work environment, individual capacities, and human nature. The aim is to be proactive, identify error precursors before an incident, and reduce risk through various human performance tools. There is a long list of precursors, including rushing, memory lapses, multi-tasking, unclear goals, distractions, confusing displays, personality conflicts, lack of knowledge, poor communication, unsafe attitudes, habit patterns, complacency and mental shortcuts.
Tools to reduce errors
Tools to address these precursors and reduce their risks include pre-job briefings, job site reviews, post-job reviews, procedure use and adherence, self-check (stop, think, act, review), stopping when unsure, flagging and blocking (using markers, labels or devices), and having workers repeat back instructions to the leader for clarity.
“There is the need for extreme clarity in job briefings,” says Mike Doherty. “Anyone can do a job briefing. You want to execute a quality job briefing with no murkiness or vagueness.”
Red flags
Nineteen human performance red flags are listed in Annex Q, ranging from cumbersome risk management processes, complacency due to past successes, lack of supervisory delegation, and individuals making snap, risky judgments.
The importance of culture
Annex Q ends with a discussion of workplace culture, stating, “The reduction or elimination of electrical incidents requires all members of the workplace to cultivate and consistently exhibit a culture that supports the use of human performance tools and principles. This includes establishing a blame-free culture that supports incident reporting.”
Author and consultant David Marx has influenced the health care industry with his concept of a “Just Culture” – one that encourages safety cultures to be less punitive yet still accountable. This hits a nerve with a number of human performance experts.
“My pet peeve is that when human performance talks about lack of attention to detail or not stopping when unsure, everyone spins this to focus only on the worker rather than all accountable in the safety managed system,” says Doherty .
“The concepts like making more of an effort not to blame the worker are good,” says Rich Fairfax, “but I see a lot of companies approaching human performance through a behavior-based safety approach.” BBS has evolved and broadened its focus, but for decades was criticized for singling out worker behaviors as the cause of risks.
“I do worry the language is focused on human error and that can lead to misguided thinking,” says author and consultant Colin Duncan. “A better focus is on performance variability and its role in system reliability.”
Overemphasizing the “human” element
There is danger in putting too much emphasis on the “human” component of human performance, human factors and human errors. David Varwig recalls in the early days when the nuclear industry used human performance tools, confused and overwhelmed workers — when they made an error they couldn’t hide — would say, “Oh well, chalk it up to my being human. I guess I need to tell others how I screwed up and what they need to do so it doesn’t happen to them.”
Varwig and others hope history doesn’t repeat itself as human performance tools gain traction and reaches a wider audience through standards like NFPA 70E.
Looking for a reprint of this article?
From high-res PDFs to custom plaques, order your copy today!