United Piping goes 2 million man hours without a lost-time injury
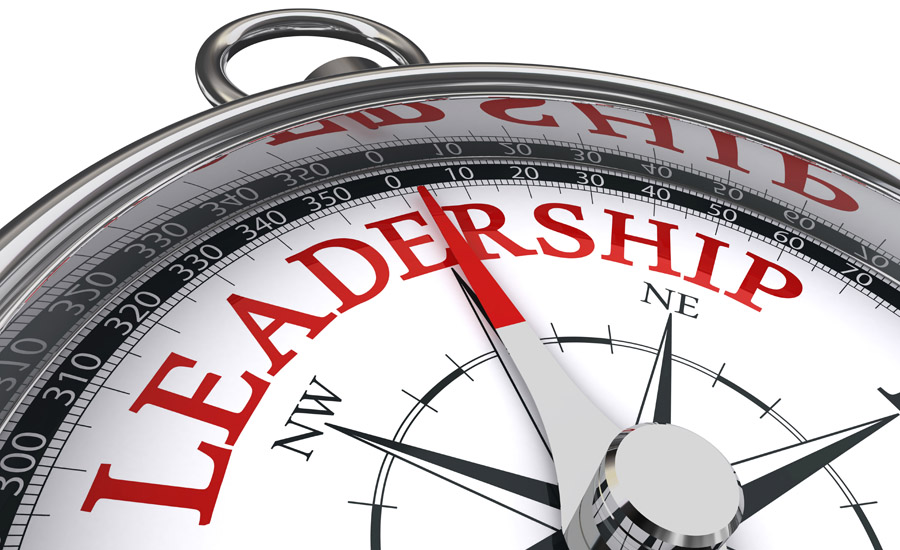
In March, 2019, United Piping, Inc, a pipeline construction company based in Duluth, MN and founded in 1997, surpassed a milestone – two million man hours worked without a lost-time injury. Key to this achievement in a hazardous industry is UPI Piping’s strong culture of safety values and practices.
The company states on its website: “At United Piping Inc. (UPI) it is a moral obligation to provide each and every employee a safe place to work. UPI employees are highly trained and experienced in all applicable safety and environmental regulations to ensure pipeline safety and environmental safety. We do our best to minimize our environmental impact and maximize personal safety.
“UPI employees are held to the highest safety standard. As part of our commitment to safety, we have an incentive program to keep safety in the forefront of our employees’ minds. We also encourage employees to submit safety opportunities when they observe a situation in which we can improve.
We also work to ensure the safety of our crews through UPI’s “Think Three” campaign: prevent hand injuries, safely lift and handle material, and prevent slips, trips and falls. Employees can find the campaign at job sites and it is supported by the Safety Department.” All new employees go through extensive training, including safety.
Here is an exclusive interview ISHN conducted with Mike Villa, UPI manager of safety:
How many employees does UPI have?
300 employees.
What is the size of the UPI safety and health department? How many full-time staffers?
There is myself at headquarters and eight field safety leaders who are dedicated, full-time to safety.
Does UPI use any of the new safety mobile apps or smart devices?
A year ago we started using an app, a small unit that goes in the windshield of all company vehicles. When the vehicle is in motion, the device shuts down all phones and uses preset GPS for podcasts and music for drivers to listen to.
The intent is to avoid distractions, distracted driving. A first it was a big change, now everyone has taken to it just fine.
Why does UPI say safety is a moral obligation, not a compliance or regulatory issue?
We feel from leaders on down, safety is simply good business, and a moral obligation for company and employees
UPI’s core value of caring. What does that mean, and where did the value originate from?
UPI’s three values of caring, integrity and respect come from employees in the past several years. We conducted interviews and hired an outside agency to craft our vision and mission statement. We hired outside because we have a great safety culture and culture in general, and UPI wanted to memorialize and document that to move forward.
Fabrication, excavation, on-site installations, maintenance – what are the primary safety hazards in this work?
Driving is the number one hazard; another hazard is working near or on roadways, when closing down roadways. Other hazards include open system work exposed to flammable vapors, ton of excavations, and confined spaces.
What safety training do your employees receive?
When we hire we do safety onboarding with the training department or field safety leaders. We will show videos, PowerPoints; there is hands-on training that highlights hazards and tasks. Operator Qualification training is required by DOT. It has modules for blasting, pipeline coating and painting, excavating and backfill line locating -- all are regulated by DOT. Our customers transport across state lines so we are regulated by DOT. Operator qualification training is for everyone in the field, about 225 workers.
With a 25,000-sq. ft. fabrication facility, regional offices in IL, MI and PA, and serving clients across the country, how does UPI make safety practices consistent everywhere?
Every year we hold foremen training for foremen and supervisors that runs two to three days. This event keeps things consistent; we go over new practices, a bunch of everything, safety included. We also hold one to three safety training events each year in Duluth and Chicago to make sure everyone is on same page; we cover lessons learned from events, regular training for excavations, etc.
What makes UPI’s top-notch safety culture possible? What are the key essentials?
The number one, factor: senior leaders are setting tone and making the commitment. This filters down to field supervisors. You lead by example.
What are the keys to sustaining a top notch safety culture?
Once you feel you have a good one, you can never can let your guard down. Leaders must stay engaged and listen to employees. Many of the best ideas come from field. We like to say safety is bottom up and top down. Employees can mentor; they can stop work; they are empowered
What type of safety incentive program does UPI use to keep workers engaged in safety?
We call it our “Safety Opportunity” program. It was started in 2011 and revamped in 2016. It allows and encourages employees to identify unsafe behaviors and hazards, document those, have a conversation about hazardous behavior, document it on the Safety Opportunity form, and then turn into me. I assign points based on hazards mitigated -- the greater the hazard, the greater the mitigation and the greater the points awarded. Points show up on pay stubs and can be used to acquire products from a safety catalog
How does UPI combat pressure to not report or hide injuries in order to keep the record hours of no lost-time injuries going?
There’s no pressure. The program has never been about any form of punishing anyone. We will never do that because then you are hiding the root cause. We receive 200 to 500 safety opportunity forms a month.
UPI employees are held to the highest safety standard. What does this mean? How are workers held accountable for their safety performance?
We truly don’t believe in punishment. We will use discipline when needed, but employees are held accountable by peers, the culture, their foremen. The culture is driven down by leaders. Employees are held accountable by leaders and peers.
How does UPI get employees to buy into the Commitment to Zero injuries in the field, since employees know luck and unforeseen circumstances make zero incidents almost impossible?
You need buy-in, plus the Commitment to Zero is believed in and supported by leadership. We really have had only one non-preventable incident; on a Sunday a tornado that ripped through a worksite. No one was injured The buy-in for zero is simply part of our culture.
Describe the UPI “Think Three” campaign – why is focus on hand injuries, lifting, and slips, trips and falls?
“Think Three” was developed in 2017 after reviewing cases from 2004 to 2016. Hand injuries, slips, and unsafe material handling accounted for 80 percent of recordables. Hand injuries took the top spot. History will repeat itself unless you do something. This is an awareness campaign in part, a poster campaign with posters and stickers. It is incorporated into the Safety Opportunity program, which includes a focus on hand injuries, slips, trips and falls, and material handling.
We also emphasize fire prevention and mitigation, environmental containment under equipment, spill kits and so on.
Employees mitigate 90-95 percent of all hazards. The hazards are addressed right then and there by the employee in the field, not the field safety officer or the foreman or supervisor.
How does UPI decide its yearly safety goals? What are the goals for 2019?
Goals are ultimately are decided by senior leaders, safety leaders, and superintendents based on past performance trends. Zero recordable injuries is the most important goal for 2019. Another goal: having 4.5 safety opportunities turned in for 1,000 hours worked, we’re at 6 or something close to that now. Our third goal is to reduce first aid incident frequency rate by 25 percent. Year to date we are on track for all goals.
Describe UPI senior leaders’ role in your safety culture.
Number one, the safety department has a budget. If we need an expense, and if it’s justified, I get no pushback.
Also our leaders are visible in the field, and really, really support the right and responsibility for employees to stop unsafe work.
Leaders are active in our Safety Day events and foremen training, active in the Safety Opportunity program.
If I review an exceptional Safety Opportunity, every week or two I’ll copy senior leaders. They will call or hand-write an encouraging letter to the individual. Also every month a Safety Opportunity report goes to them so they can track from 30,000 feet how the program is going.
Looking for a reprint of this article?
From high-res PDFs to custom plaques, order your copy today!