4 safety lessons from a serious forklift accident
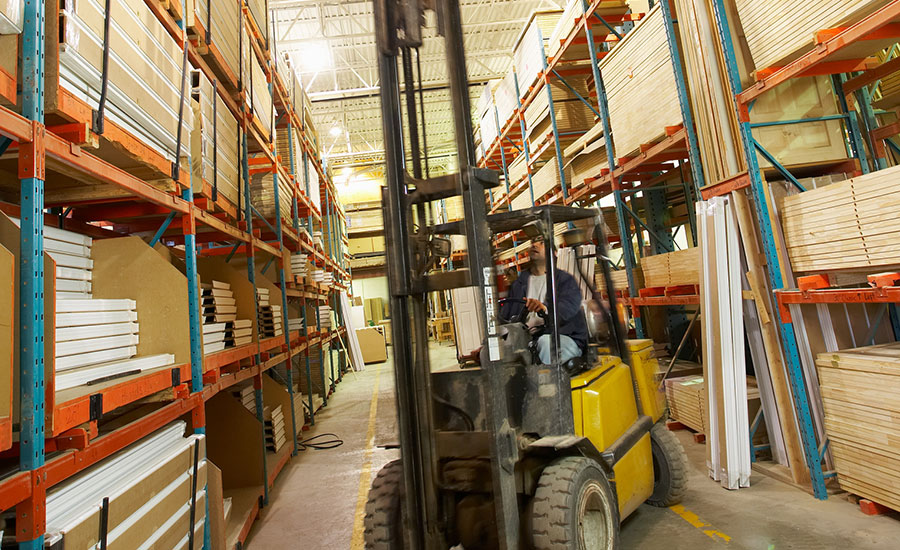
An employee of a Pennsylvania company had his leg amputated after it was run over – twice – by a forklift driven by a fellow employee. That July 2015 incident resulted in lawsuits against several companies and ultimately, in a $9 million settlement.
Here are four things you can learn from that incident.
1. Multiple parties must enforce safe operating rules
Emmitt Johnson, an employee of Mill Corp., was operating the forklift involved in the incident at a Newman & Company-owned warehouse in Philadelphia. Bridge View Paper Company, United States Recycling and Corestaff Inc., a staffing agency, comprised the other defendants in the case.
The court documents said Johnson did not look where he was going while reversing the forklift because he was preoccupied with counting bales of stacked contents while driving.
However, there were other faults; Johnson did not alert others by using the forklift's horn, and he failed to stop the forklift before reversing around a corner. Coverage of the case reports that Johnson admitted he violated all basic forklift safety rules in the moments leading up to the incident.
The number of defendants in the case, coupled with the various safety rules that were violated, highlight the fact that all parties involved with hiring or managing industrial workers must ensure those employees receive training about workplace safety. More important, they need to do anything in their power to make sure staff members follow the rules.
Despite the settlement, there is inconclusive evidence that one or more of the parties involved failed to provide Johnson with training or verify that he followed best practices for safety. However, this incident is a clear reminder that safety training and monitoring are collective efforts and not the sole responsibility of a single party.
2. Don't overlook forklift safety for pedestrians
Forklifts are not dangerous when people follow proper safety procedures. There are many different kinds of forklifts that can accommodate aspects like terrain and warehouse space. Individuals must follow safety standards for each of them. Besides the forklift safety rules for operators, you also need to cover pedestrian safety for forklifts in any training provided.
That means teaching people who are on foot how to stay aware of their surroundings when working in environments with forklifts. For example, there is a four-foot safety zone recommendation for pedestrians around forklifts. The wide turning radius means people who are farther away must remain exceptionally careful, but the recommended zone stops body parts from getting run over by the machines.
The defendants stated Jones walked into the path of the forklift and did not alert Johnson to his presence. What happened afterward illustrates why forklift safety training should not only extend to operators, but to everyone who works around forklifts.
3. Companies should provide ongoing training to all employees — especially ones with histories of mishaps
Frequent feedback helps workers understand when they're doing well and where room for improvement exists. It's essential for companies to respond promptly when people don't follow workplace rules. In a situation where it's necessary to bring up an issue with a worker, always do so in private and create written documentation of what happened in a meeting.
The court material said Johnson's record showed he was not concerned enough about safety. The legal coverage did not mention that Johnson's employer failed to react appropriately due to his history. Nonetheless Jones’ injury is a reminder of how all companies need to have a consistent dialogue with workers about the necessity of safe behaviors.
Since Johnson had exhibited safety shortcomings before this incident, that would give his employer an even more compelling reason to provide him with ongoing feedback. Moreover, if he continued to display a lack of regard for safety procedures, disciplinary action should have been taken.
4. Safety training should be up-to-date and relevant
Legal documents mentioned the safety training Johnson received was "inadequate" but the coverage does not disclose more details. Even that limited information indicates that industrial companies must work hard to get resources for their workers that are current and relevant to the job performed. For example, the safety training given to a forklift operator would differ from what an assembly line member receives.
Moreover, specific safety training about individual pieces of equipment or tasks should accompany more generalized requirements, such as to always wear personal protective equipment while at work.
Lessons from all incidents
The life-changing injury Jones suffered is unfortunate, but it shows how it's possible to learn from all events — both positive and negative.
Looking for a reprint of this article?
From high-res PDFs to custom plaques, order your copy today!