Metal fabrication shop safety tips
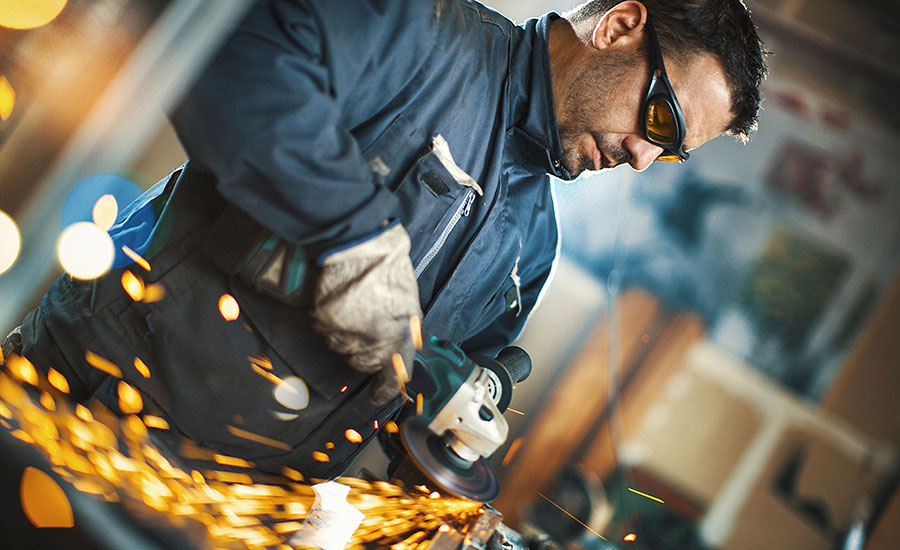
Credit: Getty Images
Metal fabrication is an integral part of many different industries, and it can be one of the most dangerous due to the tools and techniques necessary to complete each task. Metal shop injuries are often extreme and can be even fatal in some situations. Why is metal fabrication safety so important? What can shop owners and supervisors do to ensure their factory floors are as safe as possible?
Common safety problems
A company that doesn't focus on creating a safety culture or providing the correct personal protective equipment and training is failing its workers. Accidents in the metal shop frequently cause loss of limb or even death. What are some of the most common fabrication safety concerns?1
- No safety guards: Most fabrication equipment comes with safety guards installed to prevent injuries, as well as an emergency shutoff switch and sensors to keep employees safe. Removing these safety measures makes the equipment inherently more dangerous, even if it saves a little bit of time.
- Lacking or ill-fitting personal protective equipment (PPE): Personal protective equipment will vary from job to job — someone working with caustic chemicals will need different PPE than someone who's sandblasting. Someone using sand to sandblast2 might need different PPE than someone using steel shot. Companies that don't provide and maintain PPE that fits properly are putting their employees at risk.
- Insufficient training: Expecting employees to work on a piece of equipment they haven't been trained on is a recipe for disaster. Training should be ongoing. Don't expect a single training session to be sufficient, regardless of how often the employee uses that particular piece of equipment.
- No safety culture: Safety might be the primary responsibility of management and supervisors, but everyone from the highest-paid CEO to the newest fabricator needs to be involved in keeping the workplace safe. Without a culture that revolves around safety, accidents and injuries can happen.
- Rushed, harried or stressed workers: Employees need to be in the right state of mind when they're working on the fabrication floor. If they're stressed out about a deadline or rushing to complete an order on time, they're more likely to take shortcuts or make mistakes that could result in an injury.
- Poor housekeeping: Heavy equipment isn't the only risk on the production floor. Poor housekeeping — dirty floors that get slippery, garbage on the ground that could create a tripping hazard or unattended spills, for example — can create safety hazards.
Safety should be on everyone's mind on a metal fabrication production floor, from the moment they clock in until they leave for the night. Newer equipment is starting to make that focus a little bit easier to maintain.
Built-in safety features
Many new pieces of equipment come from the factory with worker safety in mind. Take a power-press, for example — a high-powered machine used to shape sheets of metal. It presses downward with massive force, and the most common injury that occurs when using one of these machines is amputation.
New power presses are equipped with sensors3 that will not allow the machine to complete a press cycle if it detects a problem. If there's a hand or other body part in the way, the press will not move. These sensors use light. If the beam of light is broken, the equipment goes into safety mode and can't be used again until the problem is corrected.
This advancement doesn't just help keep workers safer — it also helps improve productivity by preventing the inevitable downtime that follows an on-the-job injury. If a production floor only has one power-press, an injury could take that integral machine offline for hours or days during a worker’s compensation investigation.
These same beams of light can be used to mark off the safe perimeter surrounding a piece of equipment to prevent an employee from accidentally wandering into a dangerous area while a machine is in use. The principle is the same — if someone breaks a beam, the device will stop working until the problem is corrected.
The right direction
Metal fabrication has been a part of the manufacturing industry for a long time. The tools and techniques have changed, but the need for shaped metal in everything from automotive manufacturing to construction has not.
Consistent training, establishing a culture of workplace safety and ensuring each machine is still equipped with its safety guards are all steps in the right direction. Supervisors may be buying the safety equipment, but keeping the production floor safe and productive is everyone's responsibility.
Sources
Looking for a reprint of this article?
From high-res PDFs to custom plaques, order your copy today!