Welding safety quick tips
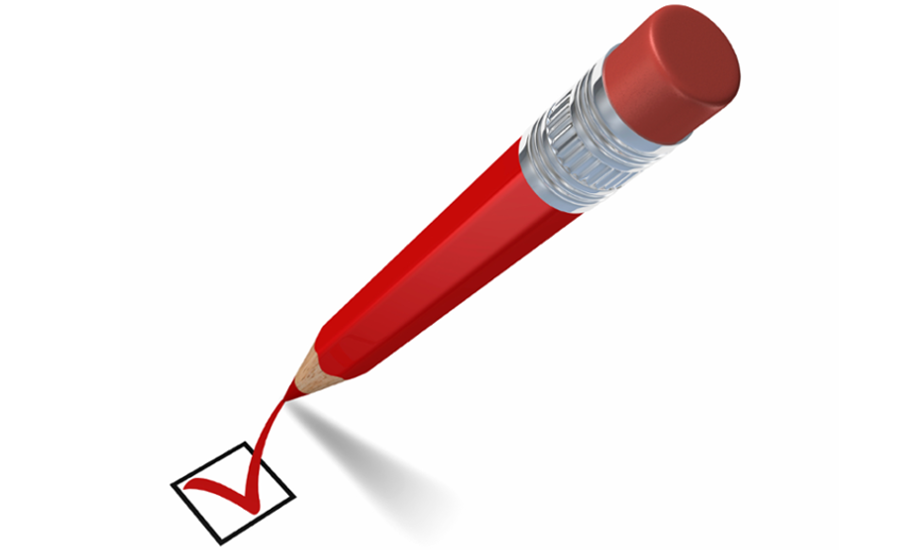
Welding is the most common method of joining metals in industry today. When welded, two pieces of similar metals are fused together by the use of heat, pressure or both. Once completed, the welded joint is as strong as or stronger than the pieces from which the joint is formed.
Welding Hazards and NIOSH’s Hierarchy of Controls
Impact, penetration, harmful dust, smoke, fumes, heat and injurious light radiation are all potential hazards associated with welding. Welding “smoke” is a mixture of very fine particles (fumes) and gases. Depending upon what is being welded, many of the substances in the smoke can be extremely toxic. The intense heat of welding and sparks can cause burns. Eye injuries have resulted from contact with hot slag and metal chips. The intense light associated with welding can cause eye damage. Ultraviolet light from an arc can cause “welder’s flash” and also skin burns. There is also a danger of electric shock. If combustible or flammable materials are nearby, the heat and sparks produced by welding can cause fires or explosions. The use of compressed gas cylinders poses some unique hazards to the welder as well.
NIOSH’s Hierarchy of Hazard Controls is a widely accepted method used by many to determine feasible and effective hazard control solutions. This concept is taught to managers in industry to be promoted as standard practice in the workplace. Following the hierarchy normally leads to the implementation of inherently safe systems, where the risk of illness or injury has been substantially reduced. It is depicted as a pyramid with five levels:
Elimination: Eliminating the hazard, or physically removing it, is the most effective hazard control, such as eliminating welding.
Substitution: Involves replacing something that produces a hazard (similar to elimination) with something that is less hazardous, such as replacing the base welding metal with something less toxic.
Engineering Controls: Engineering controls do not eliminate the hazard, but rather isolate people from the hazard, such as local ventilation at the source of the hazard.
Administrative Controls: Administrative controls change the way people work. Examples include procedural changes, employee training and installation of signs and warning labels.
Personal Protective Equipment (PPE): PPE is the last control and is worn to minimize exposure to a variety of hazards. PPE is considered the least effective means of controlling hazards. Examples associated with welding are respirators and flame-resistant clothing.
Welding Safety Precautions
OSHA provides basic fire prevention and protection precautions to follow in the welding, cutting and brazing standard found in 29 Code of Federal Regulations (CFR) 1910.252(a). Highlights include:
- A responsible individual must inspect the area and identify precautions to be taken preferably on a written Hot Works permit
- Fire extinguishers must be ready for immediate use
- A fire watch lasting at least 30 minutes after the welding or cutting operations is required if more than a minor fire might develop
- All combustibles must be moved 35 feet away or properly protected or shielded
Prohibited areas for welding include
● Areas unauthorized by management
● Areas where sprinklers are impaired
● Areas in explosive atmospheres
● Areas near storage of large quantities of readily ignitable materials
Types of Welding
Gas welding: Two metals are joined by melting or fusing their adjoining surfaces. This is done by directing a gas flame over the metals until a molten puddle is formed. The energy for gas welding comes from the combustion of a fuel with oxygen or air. A few of the most popular fuels are acetylene, MAPP gas and hydrogen. Since gas welding is slower and easier to control than electric arc welding, it is often used in applications such as general maintenance work, brazing and soldering.
Arc welding: Two metals are joined by generating an electric arc between a covered metal electrode and the base metals. Heat is produced by the arc, which in turn, melts the metal and mixes the molten deposits of the coated electrode. The arc energy is provided by a power supply unit that furnishes direct or alternating current. The electrodes carry the current to form the arc, producing a gas that shields the arc from the atmosphere, and add metal to control the weld shape. When an arc is struck using a coated electrode, the intense heat melts the top of the electrode. The drops of metal from the electrode enter the arc stream and are deposited on the base metal. The equipment needed for electric arc welding is a power supply, electrode holder, ground clamp, protective shield and welder’s protective clothing.
Oxygen and arc cutting: Metal cutting in welding is the severing or removal of metal by a flame or arc. The most common cutting processes are:
Oxygen cutting: Metal is heated by gas flame, and an oxygen jet does the cutting
Arc cutting: Intense heat of electric arc melts away the metal
Personal Protective Equipment (PPE)
Eye and face protection:29 CFR 1910.252(b)(2) states the requirements for eye protection. Helmet, hand shield, goggles and safety glasses or combination of these are acceptable protection in various applications. All filter lenses and plates must meet the test for transmission of radiant energy prescribed in ANSI/ISEA Z87.1-2015, American National Standard for Occupational and Educational Personal Eye and Face Protection Devices. According toOSHA 29 CFR 1910.252 (b)(2)(ii)(B), “Helmets and hand shields shall be arranged to protect the face, neck and ears from direct radiant heat from the arc.”Welding helmets with filter platesare intended to help protect users from arc rays and from weld sparks and spatters that strike directly against the helmet. They are not intended to protect against slag chips, grinding fragments, wire wheel bristles and similar hazards that can ricochet under the helmet. Spectacles, goggles or other appropriate eye protection must also be worn to protect against these impact hazards.
When arc cutting and arc welding with an open arc, OSHA requires operators to use helmets or hand shields with filter lenses and cover plates. Nearby personnel viewing the arc must also be protected. Safety glasses with a Shade 2 lens are recommended for general-purpose protection for viewers.Protective clothing: 29 CFR 1910.252(b)(3) refers to the PPE Hazard Assessment in 29 CFR 1910.132. This requires the employer to identify the hazard and appropriate PPE needed to protect the employer from the hazards.
Consensus standard ANSI Z49.1-2012, Safety in Welding, Cutting, and Allied Processes, provides guidance in the safe setup and use of welding and cutting equipment, and the safe performance of welding and cutting operations. Paragraph 4.3 provides more direction on clothing selection for welding tasks. “Clothing shall be selected to minimize the potential for ignition, burning, trapping hot sparks, or electric shock.” It also offers more specific selection guidelines for clothing, gloves, leggings, capes, sleeves, ear plugs, and caps.
Ventilation
Chapter 5 of ANSI Z49.1-2012 provides guidance on ventilation for welding. Ventilation refers to changes of room air as often as necessary to prevent welders and other workers from breathing high levels of airborne contaminants. Adequate ventilation depends on the following factors:
- Volume and configuration of the space where the welding operations occur
- Number and type of operations that are generating contaminants
- Concentrations of specific toxic or flammable contaminants being generated
- Natural air flow rate where operations are taking place
- Location of the welders’ and other workers’ breathing zones in relation to contaminants or sources
Paragraph 5.4 identifies two types of ventilation: natural or mechanical. Natural ventilation is considered sufficient when necessary precautions are taken to keep the welder’s breathing zone away from the air contaminants and when sampling of the atmosphere shows that concentration of air contaminants are below allowable limits.
If operations do not fall within the natural ventilation guidelines, mechanical ventilation is required. Mechanical ventilation options generally fall into three basic categories:
- Local exhaust
- Local forced air
- General area mechanical air movement
Local Exhaust
This system consists of fixed or moveable exhaust hoods positioned as near as practicable to the work that are able to maintain a capture velocity of 100 feet per minute to keep air contaminants below the allowable limits. The hood and housing may have to be repositioned by the worker to get maximum benefit from this means of ventilation. Hoods generally remove the fumes and contaminated air through ducting and filtration before being exhausted to the outdoors or recirculated into the work area. General mechanical ventilation may be necessary in addition to local forced ventilation to make up for the air that is being lost.
Local Forced Air
This system, typically a fan, is placed so air is moved horizontally across the welder’s face.
General Mechanical Ventilation
This system is generally made up of items like roof exhaust fans, wall exhaust fans, and similar large area air movers. This system is not usually a satisfactory way by itself to control contaminants in the breathing zone of a welder; however, it is often helpful when used in addition to local ventilation.
Chapter 5 also addresses concerns about recirculation, low allowable-limit materials, confined spaces, adjacent persons, brazing furnaces and contaminants containing:
- Fluorine compounds
- Zinc and copper
- Cleaning compounds
- Chlorinated hydrocarbons
- Asbestos
Fumes and gases from welding and cutting cannot be easily classified. The quantity of fumes and gases is relative to a combination of the metal being worked, consumable material being used depending on the type of welding being done, contaminants in the atmosphere, and the area the welding is taking place in. Once these are all known personal air sampling can be done to verify the concentration levels of toxic fumes and gases.
Reference OSHA’s 29 CFR 1910 Subpart Q for guidance when performing the following operations:
- 29 CFR 1910.252 General Requirements for all Welding
- 29 CFR 1910.253 Oxygen-fuel gas Welding and Cutting
- 29 CFR 1910.254 Arc Welding and Cutting
- 29 CFR 1910.255 Resistance Welding
Commonly Asked Questions
Q. What is a fume plume?
A. A fume plume is the clearly visible column of fume that rises directly from the spot of welding or cutting. Welders and cutters should take precautions to avoid breathing this area directly. Ventilation can direct the plume away from the breathing zone. (Fume removal is most effective when the air flow is directed across the face of the welder, rather than from behind.)
Q. How do I know what hazardous materials exist in the base metal including residual chemicals on the base metal or consumables like the gas or wire I may be using?
A. Check the Safety Data Sheet (SDS). The suppliers of welding materials must provide a SDS or equivalent documentation identifying the hazardous materials, if any, used in welding and cutting products.
Q. What are the storage requirements for oxygen and acetylene and other fuel gas cylinders?
A. Oxygen cylinders should be stored 20 feet or more from fuel gas cylinders or separated by a noncombustible barrier at least five feet high with a one-half-hour fire resistance rating.
Q. What is MAPP gas?
A. MAPP gas is a product that was developed as a fuel for welding, brazing, cutting, flame hardening and metallizing operations. It has many of the physical properties of acetylene, but lacks its shock sensitivity, and therefore, can be stored and shipped in lighter containers. MAPP gas is the result of rearranging the molecular structure of acetylene and propane. It also has a very distinct odor so any leakage can readily be detected.
References
29 CFR Subpart Q – Welding, Cutting and Brazing
(Rev. 12/2018)
Source: W.W. Grainger www.grainger.com
Looking for a reprint of this article?
From high-res PDFs to custom plaques, order your copy today!