Tesla's journey to be the world’s safest factory — 10 takeaways
Tesla raises the bar
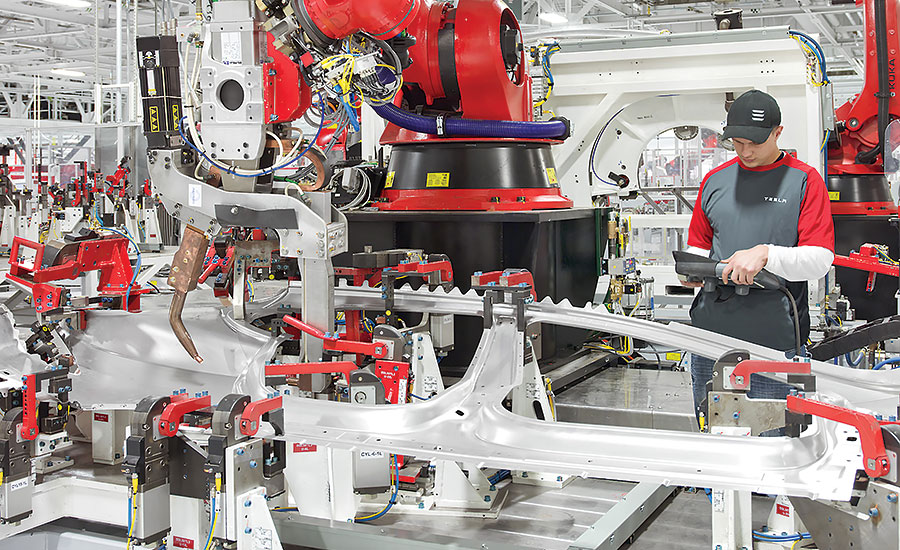
How would you feel working as the head of safety and health for one of the world’s most scrutinized companies?
Your CEO is one of the most talked-about executives in the world. How many CEOs make the cover of Rolling Stone?
Your company is only 15 years old. It has been mass-producing a very unique product for only six years. Your business has never been profitable.
The workforce at your main factory has grown from 1,000 to 10,000. The global workforce is about 45,000.
Many employees face potential life-altering injuries and fatalities. It’s a dangerous business.
Wall Street has watched your company stock lose almost one-third of its value in one month ending in early September. Meanwhile, almost 500,000 customers are waiting for pre-ordered products.
Welcome to the world of Tesla, maker of sleek electric sedans and SUVs. Where the EHS staff talks about “really cool” and “super cool” things. They call their chairman and CEO by his first name – Elon. Elon Musk “is a systems thinker, very practical, a problem-solver, this is a new kind of leadership for me,” says Laurie Shelby, vice president of environmental health and safety.
The VP of EHS loves human performance. Expects human error. Talks of failing safely. Talks continually about being proactive, about engagement, listening, watching and learning from “associates.”
The safety bar is set high, very high. Tesla has said at different times it wants to have the safest factories in the world, the safest on Earth, and in particular, to have its Fremont, California, main assembly plant be the safest auto manufacturing factory in the world.
The manufacturing hub
The Fremont facility has made headlines in recent years for numerous reasons. Musk has been known to sleep in a small alcove at the center of the factory. The Washington Post has called it a madhouse robotic city with 10,000 employees and hundreds of contractors. It houses more than 1,000 high-powered German robots on the assembly line for Tesla’s Model 3 lithium-ion rechargeable battery-powered sedan.
Musk has said “car business is hell.” Production bottlenecks have delayed ramping up output of the Model 3, key to the company’s profitability. And several years ago the Fremont plant was accused of shoddy injury and illness recordkeeping, hiding injuries, and overworking employees, which Tesla vehemently protests as being overblown, biased reporting.
The factory also builds Tesla Model S and Model X vehicles, producing 7,000 total vehicles in June of this year. If Tesla can produce 350,000 per year, it should enable the company to become profitable for the first time, according to Tesla’s second quarter, 2018 update.
The Fremont factory spans 370 acres of barren industrial land 38 miles south of San Francisco. It was built by General Motors in 1962, and has 5.4 million square feet of manufacturing and office space. The plant was shuttered in 2009 after a joint GM-Toyota venture ended.
Fremont’s mayor viewed the site as dead. Tesla, founded in 2003, took possession of the factory in 2010. Initially, it was ten times the size Tesla needed. Model 3 production is projected to reach 50,000 to 55,000 vehicles alone in the third quarter of 2018, and Tesla has announced plans to double the size of the facility with about 4.5 million square feet of space. The only carmaker in California, Tesla has invested more than $3 billion in the Fremont factory.
Actions louder than words
Tesla officials wouldn’t divulge to ISHN for this exclusive story the Fremont factory’s EHS budget. But actions speak louder than words when it comes to safety. Laurie Shelby, CIH, CSP, was hired as the VP of EHS last October after a career at Alcoa that saw her rise from an EHS regional auditor to VP of EHS Primary Products. Shelby and members of her team meet every other week with Musk. The Fremont factory now employs about 40 full-time EHS specialists who are embedded in the factory’s nine departments, as well as about 30 hazardous waste technicians. EHS specialists are on a first-name basis with associates, according to safety experts who have been invited to tour the plant, give recommendations, and spoke with ISHN on the condition they would remain anonymous.
Work Right NW, a Washington state-based company, has been contracted to provide on-the-floor athletic coaches/trainers who help associates deal with heat stress, fatigue, and musculoskeletal issues by providing hydration, stretching and other exercises, and general wellness advice, such as diet and rest.
Safety and health infrastructure
Tesla has a global EHS Council that meets every two weeks and face-to-face quarterly, according to a company spokeswoman. The core of the Council is comprised of the EHS VP – the Council administrator -- Centers of Excellence functional leaders, the EHS attorney, and EHS regional leaders. There’s no safety silo syndrome here. The chief security officer, sustainability leader, quality leader, communications leaders, HR, and operations managers attend meetings as needed.
The company’s EHS infrastructure includes Centers of Excellence with global reach for ergonomics; occupational health and wellness; environmental affairs; systems, learning and communications; and safety and contractors. The centers are communication hubs, researching, establishing and deploying best practices, standards and guidelines for EHS risks.
Safety teams made up of hourly and salaried associates hold regular meetings, walk the floors conducting audits and asking questions, validating controls, finding and fixing hazards, and investigating incidents and near-misses.
Here are ten key elements of Tesla’s EHS processes:
1. Transparency
When Tesla did their own evaluation of injury and illness recordkeeping several years ago and found discrepancies, “I was impressed that they voluntarily said, ‘We’ve got to ’fess up to the errors, bite the bullet and move on’,” says an outside consultant who has visited the Fremont site multiple times. He recommended a third-party review of the recordkeeping, which was done last spring by ORCHSE. “They found one minor discrepancy out of thousands, which is remarkable,” he says. A second outside consultant agrees: “I found they have a good, solid handle on recordkeeping. They have a dedicated staff that deals with any injury or illness issues. They have a way to go, but they’re on top of it.”
2. Senior leadership
Elon Musk is a world-famous workaholic and micro-manager. He’s an engineer, a systems thinker, and he’s out on the floor, visible. In the midst of a union-organizing effort several years ago Musk was troubled by injuries and employee complaints, according to a visiting consultant. “He wanted to know why people were getting hurt. Why they weren’t mission-driven,” he says. “He was asking the right questions.”
“Elon’s out on the floor making sure he’s engaging with associates,” says EHS VP Shelby. “Our executives are expected to be on the floor. Our leaders are ‘servant leaders.’ That’s Tesla’s culture. I love it. I work for our associates. Elon makes that very clear to all of our leaders.”
Operations leaders and line employees are expected to own safety. “They get it,” says a consultant who has spent time with operations executives. “It’s not the classic ‘the safety department is responsible for safety.’ I talked for an hour with the VP of operations and he knew all the right answers. He knew the name of the last employee who got seriously hurt. He said, ‘I own safety, that’s mine. I own hazard assessments. I own risk, they’re my risks’.”
EHS VP Shelby is a widely-respected professional, schooled at Alcoa in the Paul O’Neill philosophy that good safety is good business. “Safety and production can’t be in competition,” she says. “They go hand-in-hand, and are integrated.”
“Laurie’s a good leader who will fend for her staff; go to the mat for them if she has to,” says a veteran EHS expert who has known her for years.
3. Engagement
Shelby continually brought up the issue of engaging the workforce in her interview with ISHN. “If you’re not out there understanding how production works, you really can’t integrate safety into production. You’ve got to really listen to employees, watch and learn. They understand how the hazards will ebb and flow. Look at the way work is performed. Talk to associates. Ask, ‘What’s the worst thing that can happen, and if it does, what keeps you safe?’ Are the controls good enough?”
Engaging employees in safety issues is a challenge for all professionals, and it can be especially testing in the middle of a unionization drive and labor-management tensions, as has been the case at the Fremont plant. “You know, you have some people saying, ‘We’re not going to participate. Safety is not our job.’ There’s always work to be done on engagement,” says a consultant who has toured the Fremont factory.
4. Human performance
“I love human performance because it really changed how I thought about injury prevention and control,” says Shelby. “We’re humans so we’re going to make mistakes. We’ve got to put controls in place so when humans do make mistakes, they fail safely. It’s a game-changer. You realize that errors are going to happen, and you find really strong controls. Preventing people from making errors is still important. But we can try to engineer out every hazard and humans will still find a way to potentially go around controls.
“When an incident does happen, our leaders are very good at not focusing on the person,” says Shelby. “It’s so easy to say, ‘Gosh, why did that person do that?’ Our leaders drive at what failed, not who failed. It’s huge when you can get off that ‘people only’ focus. Our leaders don’t accept human error as the root cause. That’s huge.”
5. Ergonomics
Ergonomic-related injuries and illnesses account for by far the majority of the Fremont factory’s recordable incidents. Michael Kirschner, Tesla’s senior program manager of the ergonomics department, uses several strategies to reduce musculoskeletal disorders. One is to build ergonomics into the vehicle, especially the Model 3. “We used a CAD program to predict how workers will work with the architecture of the car.” The Model 3 was originally designed with input from his three-person ergonomics team to reduce assembly-related stresses, strains, and awkward postures and positions.
Body movements are monitored using the proprietary myViSafe™ wearable sensor suit designed by dorsaVi. “You can look at high-risk body postures, track people’s body mechanics during the day for trends, and take that data to engineer out high-risk activities,” says Kirschner.” “I use the data for engineering controls. For example, say I’m installing something on the roof of cars. Assembly that once required workers to have their arms raised above their shoulders 80 percent of the time could be monitored and then rebalanced so arms are above shoulders only 60 percent of the time. The Work Right coaches on the floor currently use the sensor data to teach better body mechanics and stretching.”
6. Training
One of the challenges Tesla faces to reach its ultimate goal of having the safest factory on Earth is that everything is new. Work at the Fremont factory goes back only six years. The workforce has ballooned in size ten times. One consultant says some of the new hires come from retail backgrounds, not manufacturing, since the Bay Area is not a manufacturing powerhouse.
“Many of the employees are new,” says a consultant who has conducted risk communication and OSHA compliance training workshops at the Fremont plant. “To many employees, EHS has never been an issue. They come out of retail. So there’s a learning curve.”
Training that emphasizes building resilience in workers is a key tactic. Says Kirschner: “Resilience is making sure employees are physically able to do the work. We have a 30-, 60- and 90-day new hire onboarding program. Within the first 60 days we like to see associates trained on four different processes to be able to rotate and work different body parts, to have variance in their work day.”
7. Fatigue management
“We’re working very closely with our HR partners to reduce fatigue,” says Shelby. “It’s an issue closely linked to HR. “Touch points” – where the Work Right athletic trainer/coaches talk one-on-one with employees – are opportunities to ask about fatigue and make sure there are rest breaks and plenty of hydration breaks. Tesla wants to see daily touch points, with trainers asking, “How’s your day going? Anything bothering you?”
“We are reasonable to requests when people need time off,” says Shelby. “We have some training about fatigue, how to recognize it. In a blog, she describes Tesla’s new return-to-work program. An injured employee who comes back to work in a less demanding role will have their pay remain the same. If Tesla is unable to accommodate an injured employee within the company, it now temporarily places them in local non-profits such as YMCAs, libraries or food pantries and they receive their regular compensation.”
8. Finding and fixing hazards
“All professionals want to be more proactive,” says Shelby. “We all want to spend more time on leading indicators. One way we do this, on a global basis, is a ‘find it, fix it’ program. We ask all our associates, all our leaders, everybody, to find the smallest hazards so we can fix them and get ahead of them. Associates can fix hazards themselves that they find; if they can’t, the hazard report is loaded into our ‘find it, fix it’ database and we track it until closure. When we do close out, employees get an email informing them of the hazard abatement. If the fix is still not right, employees can reopen the report.”
9. Dealing with production pressures
The Fremont factory is under intense pressure to ramp up production to become profitable and satisfy stockholders’ and customers’ expectations. How to avoid the classic “production versus safety” conflict?
“Safety and production need to be at the same table, next to each other,” says Shelby. “They need to be talking. Safety wants cars out the door delivered to our customers just as much as production. When production wants to speed up a line or make a change, safety is right there with them at the table. We talk about what controls are needed to be able to do that.
“Sometimes you slow down to speed up. You make those corrections, get those controls in place, and then the speed-up occurs. We also engage employees and get their ideas about how to make small changes to avoid accidental production stops. The age-old story that safety is slowing us down is not true. Safety can speed you up. For that to happen, safety and operations just can’t be separate departments. Embedding our EHS specialists in operations departments is a big help.”
10. Dealing with intense public scrutiny
“I should have expected this amount of scrutiny when I came to work for Tesla and for Elon. It’s a level I haven’t experienced in the past,” says Shelby. So how does a professional keep calm in the eye of a media storm?
“First and foremost, we don’t get defensive,” says Shelby. “Everybody has a job to, and everybody has metrics driving them to do their job. We don’t get hung up on media stories. We just keep doing what we’re doing. We’re not perfect. We’re not where we want to be. But we’re improving and learning.
“It’s frustrating when the media focuses only on lagging indicators. It takes you down a rabbit hole. Everyone here is proactive in their thoughts.”
Part of not being defensive is being open to outsiders. Tesla has invited former OSHA officials to the Fremont factory “for feedback on how we can continue to improve,” says Shelby. An outside consultancy reviewed the factory’s injury books. And Tesla has gone out and joined ORCHSE, a consultancy with more than 100 large corporate clients. “We are benchmarking with ORCHSE for North America and the auto industry. We’re constantly benchmarking. It’s really important for everyone to benchmark in order to improve,” says Shelby.
“I’ve given them recommendations and suggestions,” says a consultant. “They’re going in the right direction. They’re committed and dedicated to improving. They want to be world class. I think they’ll get there.”
One of the keys will be holding Tesla’s current EHS team together, according to an advising consultant. “They’ve got the right team. Continuity has got to be the number one focus. You need it to sustain improvements. To drive safety blocking and tackling basics – hazard assessments, baseline industrial hygiene surveys, job safety analyses -- deeper and deeper into the organization. “The consultant’s words proved prescient. In early September, Tesla’s chief accounting officer left after a month on the job, saying the level of public attention placed on the company and the pace of the company’s culture exceeded his expectations.
All part of the challenge of becoming the world’s safest factory.
Looking for a reprint of this article?
From high-res PDFs to custom plaques, order your copy today!