OSHA to poultry industry: Time to prioritize safety
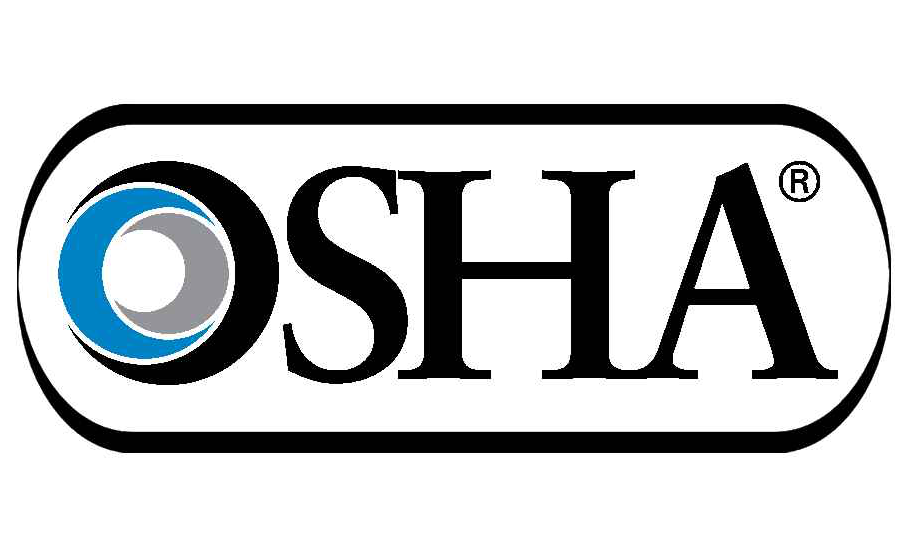
In a recent address to attendees of the National Safety Conference for the Poultry Industry, Deputy Assistant Secretary of Labor for Occupational Safety and Health Loren Sweatt expressed the hope that a “turning point” was just ahead in the sometimes-rocky relationship between OSHA and the industry.
From Sweatt’s remarks:
I have met with several of you regarding the state of the agency’s relationship with the poultry industry and how we can continue to improve that relationship. My message to you today is that the door is open to continuous improvement on how the agency interacts with you as the regulated community, either through education and training, cooperative partnerships, or enforcement.
Yes, I said enforcement. The Secretary has made it clear that he expects the agency to fully and fairly enforce the law. I have made it clear that the expectation is for the agency to do this professionally, respectfully, and by the book.
Relationship with Poultry Industry
I recognize that OSHA’s relationship with your industry has had challenges.
I am hopeful that this meeting will represent a turning point – the opportunity to work together to protect your most valuable asset – your workers.
The simple fact that you are here demonstrates the proactive approach you and your companies are taking to address worker safety and health. Everyone in this room understands their responsibility to protect workers – otherwise you wouldn’t be sitting here. So, I’d like to ask for your help to reach out to the people not in this room, who may not prioritize safety as they should.
Working with your peers, I hope you will help carry the message that while employers are responsible for the safety and health of their workers, OSHA is here to help. Sharing best practices and educational resources through industry events is a start. Reaching out to smaller producers or others who are less active in your trade associations will make inroads that the agency cannot make alone.
Part of that assistance could take the form of an alliance, similar to the one in development with the U.S. Poultry and Egg Association, National Chicken Council, and National Turkey Federation. An alliance can promote information sharing in a collegial environment. Working together we can tackle the issues facing this industry. Worker lives and livelihoods depend on our ability to jointly prevent injuries and illnesses.
Issues
Medical Management
As part of OSHA’s enforcement at poultry plants, the agency has reviewed medical management programs focusing on structures, processes, and outcomes.
Employers generally rely on three different models of in-plant medical management. Some contract out all medical services. Some conduct complete in-house care where doctors, nurses, and other professionals are hired by the company directly. Others have hybrid systems of clinical and administrative staff with different oversight chains.
OSHA has seen very different content and quality in onsite workplace clinics, nursing stations, and health units for medical management. Examples include staff who provide clinical services beyond State licensing rules and professional scopes of practice. Many facilities failed to clearly distinguish administrative and clinical oversight, leading to poor clinical outcomes.
It is troubling when facilities fail to follow their own established protocols, and even more challenging when these protocols fail to meet national standards at all. Both of these practices lead to poor clinical outcomes for workers.
Guidance to address these issues is in development and I look forward to sharing that with you when it’s complete.
Amputations
Another concern in this industry is amputations. An examination of OSHA’s severe injury reports places the poultry industry among the highest in reported amputations.
According to the Bureau of Labor Statistics, amputations are declining. However, data from Michigan, Massachusetts, and Illinois, suggests that there is underreporting for amputations ranges from 50% to 80%, or a data quality problem. As a result, the true rate of amputations in the poultry industry remains unclear.
Recent analyses of OSHA's Severe Injury Reports and the Amputations National Emphasis Program showed that OSHA inspections are associated with higher reporting of amputations, suggesting that employers inspected by OSHA are more likely to report injuries.
We hope to work with you to address this problem, either through the alliance or in some other way. These types of injuries can be prevented, but if they do occur, they should be reported.
Peracetic Acid
An issue we have heard a lot about is peracetic acid (PAA). Peracetic acid, as a disinfectant, has seen increased use in the food processing industry. As you know, it is highly reactive and effective, breaking down quickly in the disinfection process.
These characteristics make it a desirable disinfectant for poultry processing. But, it also creates challenges in trying to measure atmospheric PAA concentrations or assess worker exposure to the chemical while in use.
OSHA’s preferred method for air sampling is an easy-to-use, solid, and stable sampling media.
Recently, OSHA’s chemists have been working on a sampling method using a liquid media that is yielding promising results. I am told this could provide a validated method to sample workplace air PAA concentrations which, of course, would be shared as soon as possible.
Powered Industrial Trucks / Forklifts
I noticed that powered industrial trucks is a topic you will be discussing. According to BLS, there were 72 forklift-related fatalities in 2016. And, another 7,000 workers were injured – that’s 19 forklift incidents every day!
Any industry that uses forklifts should know how to protect its workers from harm. In June, I participated in the fifth annual Forklift Safety Day. OSHA released a new Quick Card targeting safe forklift operation. The card offers basic tips such as ensuring that operators are trained on the types of trucks used and workplace-related conditions, wearing a seatbelt, never exceeding the rated load, as well as ensuring the load is balanced.
OSHA has many other resources available to identify hazards associated with powered industrial trucks, including the Public Warehousing and Storage course offered through the OSHA Training Institute Centers.
The spring regulatory agenda indicates that a Request for Information to update the powered industrial truck standard is being drafted. Given that the consensus standards mentioned in the existing regulations are from the same year we landed a man on the moon, I think we can all agree it is time for an update.
I encourage all of you to actively participate in this rulemaking. Your professional expertise, will help ensure the effectiveness of any final rule.
Workplace Violence
Workplace violence is another important topic that I saw on your agenda.
Many of our recent steps to address workplace violence have been focused on healthcare settings. However, workplace violence is an issue that can occur in any workplace, including yours. On August 1, the agency hosted some of the premiere medical leaders for a day long discussion of workplace violence in the healthcare setting. I believe this collaborative model is how the agency should tackle these issues.
The agency has crafted workplace violence guidelines, a roadmap for prevention, and created a web tool to show what prevention looks like. These guidelines and resources can be useful in any setting. We also have a Fact Sheet that offers general prevention information. Another internal focus has been ensuring Internet resources are easily available and accessible. If you have suggestions on how to improve that interface, please let me know.
Emphasis Program
Since 2015, the most frequently cited standards in your industry have been Lock Out/Tag Out, Process Safety Management (PSM), machine guarding, and electrical (both general and wiring). Recent reviews of the Poultry emphasis program in the Southeast region reemphasize Lock Out/Tag Out and machine guarding violations as the most frequently cited standards. Other hazards that continue to be a problem include electrical, noise, chemical exposures, ergonomic, and medical management.
For those curious folks, it is the agency’s intention to continue the Regional Emphasis Programs.
Cooperative Programs
OSHA’s Cooperative Programs – alliances, partnerships, SHARP, and VPP – are excellent ways for employers, employees, and associations to work together with OSHA on meaningful safety and health initiatives.
As I have mentioned, we are in discussion with the U.S. Poultry and Egg Association, National Chicken Council, and National Turkey Federation on a national Alliance for the poultry industry.
OSHA previously had Alliances with the National Chicken Council and National Turkey Federation to focus on ergonomics and machinery hazards. We look forward to working with the industry about a new Alliance.
In addition to alliances, OSHA has many other compliance assistance resources available. The On-Site Consultation Program, works with small employers to identify hazards and help comply with OSHA regulations. It is important to note this service has a firewall between the enforcement-side of the agency.
This program provides free and confidential workplace inspections and works with the employer to find and fix hazards, achieve compliance, and improve safety and health programs.
I encourage any small employer to request a free consultation – to have someone partner with you to identify and fix hazards before an OSHA inspection.
The Voluntary Protection Program or VPP is another valuable asset for employers. I am pleased to note six poultry sites are members of VPP. VPP sites undergo intensive audits of the company’s safety and health program. It is a collaboration between management, workers, and unions (where there is representation).
Companies participating in VPP have exceptional safety and health programs, and are exempt from programmed inspections. There are basic requirements for participation in VPP. One primary requirement is for all active sites to maintain injury and illness rates below the national industry average.
One of those sites – Butterball’s site in Huntsville, Arkansas (which is covered by OSHA’s PSM standard due to the quantities of ammonia used in their refrigeration system) – has implemented a redundant ammonia, pressure relief system. This is important as it allows repairs to be made on one system, if necessary, while the other remains functional. This facility also goes above basic preventive maintenance by requiring damaged pressure relief valves in their refrigeration system to be replaced as opposed to being repaired.
In 2016, this particular VPP site reported Total Case Incident (TCIR) and Days Away Restricted Activity (DART) rates of 100% below those reported by BLS. Which means zero days away or restricted reportables.
I should also note that three of the six poultry VPP sites are Cargill sites. I see that later this afternoon Mick Berning from Cargill will be discussing Safety Leadership for Management. I hope Mick would agree that becoming a VPP site is something that every workplace should strive towards. I encourage everyone here to explore that possibility.
Whistleblower
Worker protection extends beyond compliance with regulations. It includes a worker’s right to raise safety and health concerns without fear of retaliation. In fact, companies with effective safety and health programs actually find it helpful to encourage employees to report their concerns.
Think about it: Would you rather hear about a potential problem from your employee, or from a government inspector? Or, worse, not hear about it at all, and then suffer a mishap, an injury, or even a fatality?
We encourage you to ensure that yours is a workplace where employees feel comfortable bringing issues to your attention – it is truly in everyone’s best interest.
Outreach
As I mentioned, examining ways to improve the accessibility of information about available resources is a key project. You will notice redesigned webpages, and an update of content. Taking a strategic approach, we are carefully considering the varied audiences, and how they can best access and use our materials.
We are taking this approach beyond our website to all of the materials we create, to include Fact Sheets and Quick Cards.
In fact, we just released a new safety and health Quick Card last week that addresses the solutions to common hazards at poultry processing plants. This Quick Card is more focused on the industry needs and written in plain language. It is available in both English and Spanish, and designed for employers and supervisors to give to plant workers.
Please take a look and let us know what you think about the new Quick Card, and if there are other materials you would like to see (or perhaps even in different formats).
If you are not on the QuickTakes mailing list, you should consider it. We have more than 220,000 subscribers and continue to grow at a steady pace. This free newsletter provides the latest information about agency actions, events, new resources, training, and enforcement activities. This is a great place to learn about things like new Quick Cards or alliances. You can sign-up on the OSHA website.
OSHA is active on social media with more than 11,000 Twitter followers. If you don’t already, please follow our Twitter handle @OSHA_DOL, as well as the Department of Labor’s accounts on Facebook and LinkedIn.
Conclusion
Again, thank you for inviting me to participate today. I look forward to working closely with you to address the safety and health issues in your industry. I hope this will build a solid working relationship.
Thank you again to everyone participating in this week’s Safe + Sound activities. For anyone not participating, I encourage you to check out our website to see the types of events being held. You can also find resources that you can use every day in your workplaces to improve safety and health.
I am privileged to work with over 1,900 men and women across the country dedicated to worker safety. I am truly honored to have been appointed to this position.
What we do collectively each and every day – the continuous dedication to safety improvements – truly matters when it comes to making workers safer. It is important to designate days for conferences like this and weeks for events like Safe + Sound, but I have said before and I will say again to you, safety is not just one day, it is a life time.
Looking for a reprint of this article?
From high-res PDFs to custom plaques, order your copy today!