Steel Constructions for the World — Welded in Clean Atmosphere
SCHACHTBAU Nordhausen Stahlbau GmbH benefits from several Airtowers for air purification
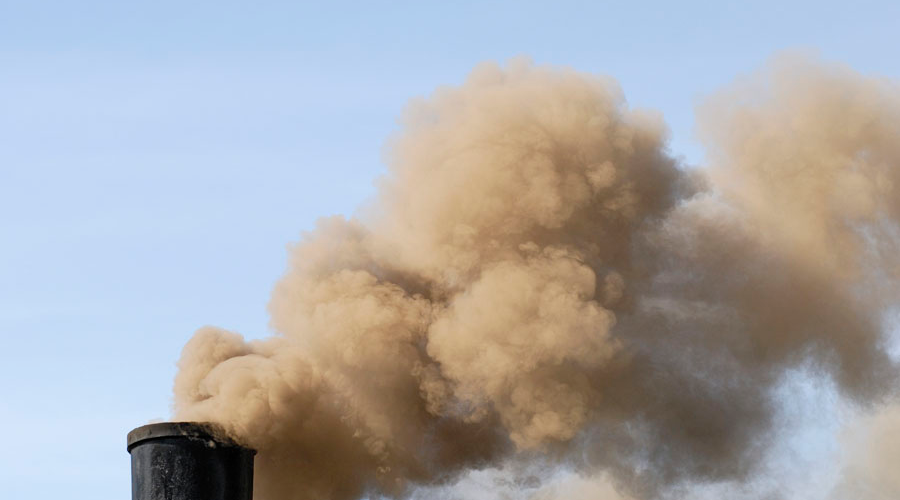
The SCHACHTBAU Group, headquartered in Nordhausen (Northern Thuringia, Germany), looks back on a tradition spanning more than 110 years of business in the sectors of mining industry, machine-building, steel construction, plant technology and building industry. Starting as a technology supplier for the specialist mining sector, the company evolved into a globally acting business with more than 900 employees in several branches.
Design and construction of the first large-scale refrigeration plant “System Gebhardt” back in 1898 marked the beginning of the company’s success story. Solutions for the mining industry, e.g. cutter heads for tunnel boring machines, turned SCHACHTBAU NORDHAUSEN into a sought-after supplier in that business.
As this industry declined in the early 1990s, the company tapped into new areas of business. Owned by Bauer Group since 1992, the company continuously developed the areas of machine-building and steel construction. The firm bundled its business activities on the construction of road and railroad bridges, dams and purification plants, as well as hall constructions. Meanwhile, more than 200 new building and restoration projects have been successfully installed in the area of road and railroad traffic, e.g. prestressed concrete bridges, steel bridges and steel composite bridges. In a recently finished project, an about 394 feet (120 meters) long network arched bridge close to the North Cape has been erected. As of late 2017, this bridge spans the Bøkfjord and thus links Norway to Russia — at a weight of roughly 600 tons.
Figure 1: Main part of the arch bridge for a traffic project at the North Cape – to fill a gap of 120 meters
![]() |
![]() |
The Nordhausen operations of SCHACHTBAU treat thousands of tons of steel each year; not just the standard alloys S235 to S460, but also S690, S960 and stainless CrNi steels. Since welding is the prior-ranking joining process, the general management system assigns highest priority to the DQS certification according to DIN EN ISO 3834-2 regarding welding requirements. The same high priority applies to the certification of its Occupational Health and Safety Management System acc. to OHSAS 18001:2007. Sheet metal is welded up to a thickness of 7.87“ (200 mm).
Each day, 60 welders and 10 welding engineers are working on a wide variety of projects. Of course, welding quality is of paramount priority.
All welding seams shall be able to pass X-ray and ultrasonic inspections, as they must withstand highest levels of strain for several decades. Protocols and documentation of the performed work and related inspection results are partly kept on file for 50 years.
Each welder must therefore deliver to the highest levels of quality – even for welding seams of several hundred meters in length. Standard welding methods are MIG, MAG and WIG.
The work takes place in large halls measuring up to 328 x 82 feet (100 x 25 meters). For ideal treatment, the parts are put into appropriate positions to ensure accessibility and work in ideal position. If needed, larger parts are lifted and moved by crane. Naturally, those processes emit large amounts of welding fumes, which are very detrimental to the health of employees.
Figure 2: Large structural steelwork for the ‘Hafenbahn Magdeburg/Germany’
Until quite recently, a fixed tubing system has been installed below the hall ceiling for extraction. After 25 years of operation, this installation neither implements state-of-the-art extraction technology, nor can it meet relevant regulatory requirements regarding pollution limit values. Modern solutions for air pollution control supersede former large-area extraction plants of low efficiency. Modifying existing extraction plants would not have made sense, neither from a financial, nor from an air handling point of view. Since the new German general dust limit values for granular bio steady types of A‑dust (1.25 mg/m³ according to TRGS association standard) are in effect, a new solution was required to effectively purify the polluted air. Even though the welders were supplied with fresh air, they had to bear an extremely sticky hall atmosphere in summer. In addition, employees not tasked with welding (e.g. transport staff, supervisors or planners) were directly exposed to welding fumes.
The use of filtration towers has been considered optimal. SCHACHTBAU got in touch with six different suppliers; three of them have been evaluated in detail. The selection process took one and a half years. “From the beginning we decided to focus on a flexible, holistic and independent solution”, said Frank Malchau, production manager at SCHACHTBAU NORDHAUSEN Stahlbau GmbH. “According to our calculations, the investment in filtration towers turned out to be considerably less expensive than a modification of the existing hall and plants.”
Figure 3: ULT Airtower for air purification in production halls
Today six Airtower filtration towers provide for purified air. On conclusion of the selection process, Airtowers turned out to be the most efficient solution of all evaluated filtration towers. On the one hand, they generate the lowest costs per cubic meter of purified air. The selected optional energy efficiency package makes sure, that the towers only start-up, when the dust concentration exceeds a certain limit value. A pollutant sensor measures emissions and the extraction plants power-up and shut-down automatically.
On the other hand, the filtration towers offer a high degree of flexibility. Depending on current needs, they can be moved to any location in the production hall.
The Airtowers operate according to the layer ventilation principle, which is regarded the best form of air recirculation, recommended by the German Employer’s Liability Insurance Association. Contaminated warm air is sucked down and purified. Achieving a filtration degree of more than 99.6%, the plants not only ensures highly purified air. Once recirculated into the work places, the air is even used to heat the production halls. “In winter, our heating is no longer in use“, says Frank Malchau.
Figure 4: Clean air around the filtration tower – on the left side rising welding fumes are discernible
The optimal positioning of the towers was determined in co-operation with the system vendor. To dimension the Airtower plants optimally, not only the building envelope has been carefully examined. In addition, the work processes have been considered in great detail. Zje Airtower vendor not only determines number and size of the plants but recommends ideal installation positions to its customers. Finally, it is ULT’s mission that customers will always undercut the latest limit values. Considering work processes and material flows, the best installation positions have been determined in close cooperation with the production planning and scheduling department of SCHACHTBAU Nordhausen.
“We take close interest in our employees’ health”, says Frank Malchau and summarizes: “Since the installation of those filtration towers we noticed a significant decline in our rate of sick leave.” Finally yet importantly, the plastic housing of the Airtower systems is considered an advantage. “Minor collisions with the towers may occur during material transports within the production hall. Due to the flexible housing this doesn’t lead to severe damages. So no repair efforts are required”, explained Frank Malchau.
To put it short: regarding the extraction and filtration plants, SCHACHTBAU NORDHAUSEN did not raise any complaints. “All of our goals and requirements concerning the selection of air purification systems are met.” Frank Malchau added with a smile: “The investment perfectly paid off. We are very happy – no reservations.”
Looking for a reprint of this article?
From high-res PDFs to custom plaques, order your copy today!