A driver’s mistake causes toxic release, endangers community
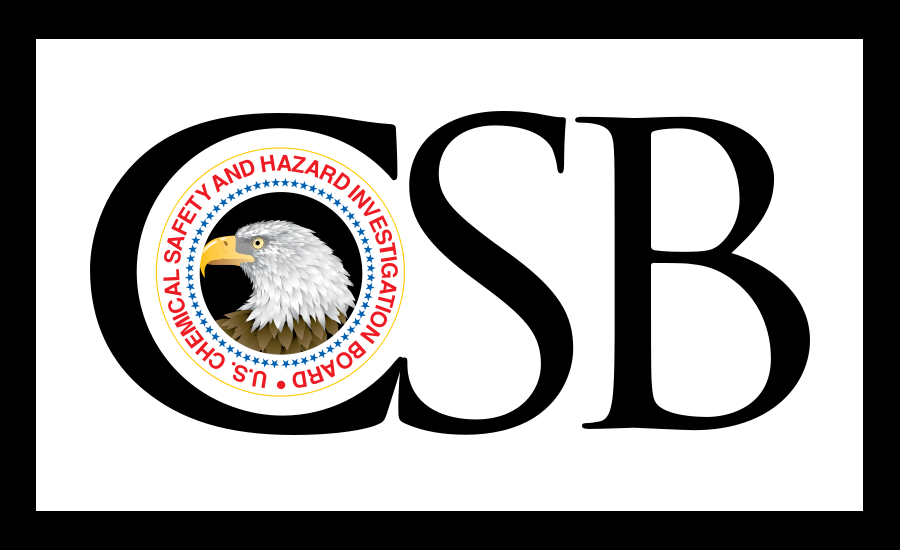
A chemical release that sent 140 people to the hospital was caused by a truck driver who mistakenly connected the hose for one chemical to the line for another. The Oct. 21, 2016 incident in Atchison, Kansas provides valuable lessons in chemical safety, according to the U.S. Chemical Safety Board (CSB), which used it as the basis of a case study titled “Key Lessons for Preventing Inadvertent Mixing during Chemical Unloading Operations.”
The release occurred at the MGPI Processing Plant, which produces distilled spirits and specialty wheat proteins and starches.
How it happened
The CSB’s investigation found that on the morning of the incident, a tanker truck arrived at the MGPI facility to deliver sulfuric acid. A facility employee escorted the driver to the locked loading dock and unlocked the gate to the fill lines and the sulfuric acid fill line.
But unknown to the operator, the sodium hypochlorite fill line was also unlocked. And the two lines, which were only 18 inches apart, looked similar but were not clearly marked. The driver inadvertently connected his truck’s sulfuric acid hose to the sodium hypochlorite line and sulfuric acid began flowing inside.
As a result of the incorrect connection, thousands of gallons of sulfuric acid from the tanker truck entered the facility’s sodium hypochlorite tank. The resulting mixture created a dense green cloud that traveled northeast of the facility until the wind shifted the cloud northwest towards a more densely populated area of town.
Those who sought treatment at local hospitals included both workers and members of the public. Authorities issued shelter-in-place and evacuation orders for thousands of local residents.
Key issues
The CSB’s investigation examined several key issues including the design of chemical transfer equipment, automated and remote shut off systems, and chemical unloading procedures.
Chairperson Vanessa Allen Sutherland said, “High risk operations, like the delivery and handling of hazardous chemicals, require strict adherence to safety protocols. An inadvertent mixture can result in a chemical reaction with extremely dangerous consequences. Our findings reaffirm the need for facilities to pay careful attention to the design and operation of chemical transfer equipment to prevent similar events.”
- The CSB’s final report includes 11 key lessons and outlines clear safety improvements that can be implemented at similar facilities across the country. Among these are facilities should evaluate chemical unloading equipment and processes and implement safeguards to reduce the likelihood of an incident, while taking into account human factors issues that could impact how facility operators and drivers interact with equipment.
- Facility management should evaluate their chemical transfer equipment and processes and, where feasible, install alarms and interlocks in the process control system that can shut down the transfer of chemicals in an emergency.
Lead Investigator Lucy Tyler added, “Facilities need to work collaboratively with their chemical distributors to conduct a risk assessment and develop and agree upon procedures for chemical unloading to ensure responsibilities are clearly defined.”
CLICK HERE to view the CSB’s safety video detailing the events leading to the release and featuring interviews by the CSB’s lead investigator and Chairperson.
Chairperson Sutherland said, “Every day facilities throughout the country receive bulk amounts of chemicals by cargo tank motor vehicles. Industry needs to review their own safety practices to ensure that such every delivery is executed safely.”
The CSB’s report issues safety recommendations to the companies involved in the incident as well as the County’s department of emergency management. The recommendations focus on proper guidance regarding unloading procedures, planning, and training for personnel as well as emergency responders. The case study also reiterates an existing recommendation for ventilation guidance for control buildings.
Looking for a reprint of this article?
From high-res PDFs to custom plaques, order your copy today!