Attention to engines can prevent many plane crashes
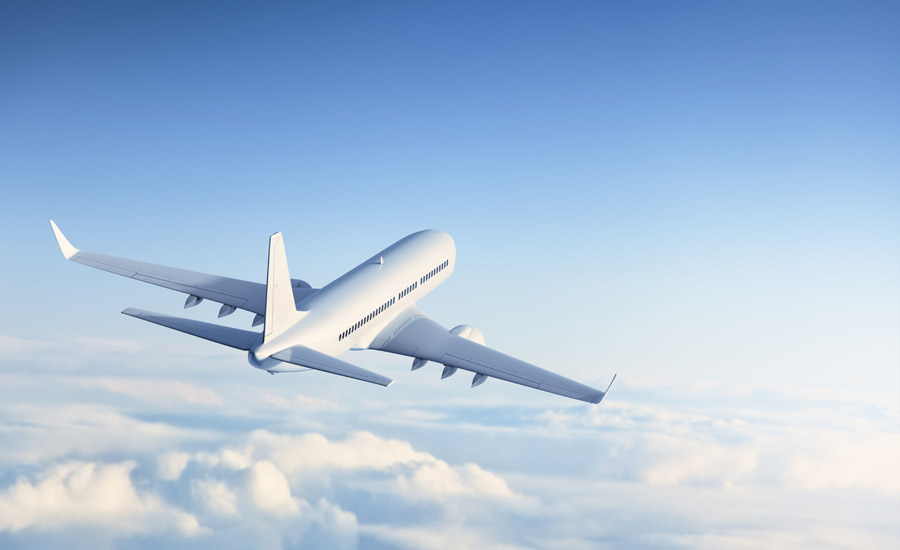
Most general aviation fatal accidents are caused by in-flight loss of control – and many those are caused by factors related to engine failure. Between 2001 and 2010, engine maintenance errors were identified as a contributing factor in 35 of 70 randomly-selected accidents. The Federal Aviation Administration (FAA) would like to help decrease that number.
Is Your Engine Up to Snuff?
The FAA recommends that pilots ensure their plane’s safety by paying close attention to proper engine maintenance, post-maintenance, advanced pre-flights, and engine performance monitoring.
Good Maintenance Practices:
- Get to know your airplane, and your mechanic
-Work with your mechanic to make sure the aircraft is operated and maintained properly. Review inspection results and talk to your mechanic about any applicable Airworthiness Directives and Service Bulletins. - Don’t ignore regular maintenance
-You can’t simply pull off to the shoulder when you are in an aircraft. You need to have all parts of the airplane functioning, and functioning well. - Comply with all manufacturer-recommended service intervals.
- Fifty-hour oil changes are recommended for most normally-aspirated piston engines.
- Turbo-charged engines should undergo oil changes more frequently.
- Check the oil filter with each oil change
-Checking the oil will tell you a lot about engine health. Several samples will create a trend. - At every other oil change, do a compression check and check magneto timing, spark plugs, and the exhaust system.
Advanced Preflight After Maintenance:
Maintenance-related problems — and the pilot’s failure to catch them — can lead to disastrous consequences.
- After maintenance, be sure to conduct a preflight that goes above-and-beyond the normal before you take flight again.
- Look at your aircraft’s maintenance history. Develop an extra checklist, as necessary, and use that checklist every time your aircraft has had maintenance.
- Become familiar with flight controls or systems prior to maintenance, so you can spot abnormalities later.
- Review ALL of your aircraft’s records, including receipts, work orders, FAA Form 337s (Major Repair and Alteration forms), and approval for return to service tags (8130-3 Forms). Also, locate any Supplemental Type Certificate (STC) data.
- Talk to your mechanic about the work that he or she did on your aircraft. Pay close attention to the components or systems that underwent repair.
- Be prepared to abort takeoff if something goes wrong, or doesn’t feel right.
Engine Performance Monitoring:
- You’ll get immediate feedback from airspeed indicators, attitude indicators, angle of attack indicators, manifold pressure gauges, RPM gauges, and G-force meters. You will be able to tell if design limitations have or are about to be exceeded. This information is available – real time – on every flight.
- Engine diagnostic equipment comes in many different forms. One version is the external, hand-held test kit that attaches to ignition plugs and determines system functionality. A good test kit can check engine compression, magnetos, ignition leads, engine timing, and more.
- Engine data management systems come in a variety of forms and are offered by many different companies. These devices monitor your engine while you focus on flying the aircraft. They can meter your mixture and exhaust gas temperature (EGT) to optimize lean-of-peak operations. Some systems even offer interpretive software and/or provide professional analysis of your data.
- A digital/electronic engine control (D/EEC) regulates the function of the injection system to ensure the engine provides the power that it needs. An engine control unit reads several sensors, and then adjusts the engine through a series of actuators. Sensors include ones for airflow, engine cooling, throttle position, and fuel flow.
The FAA and the general aviation (GA) community’s national #FlySafe campaign is designed to educate GA pilots about the best practices to calculate and predict aircraft performance and to operate within established aircraft limitations.
Looking for a reprint of this article?
From high-res PDFs to custom plaques, order your copy today!