Rockford Systems combats hydraulic press and press brake injuries with upgraded encoder-based safety control system
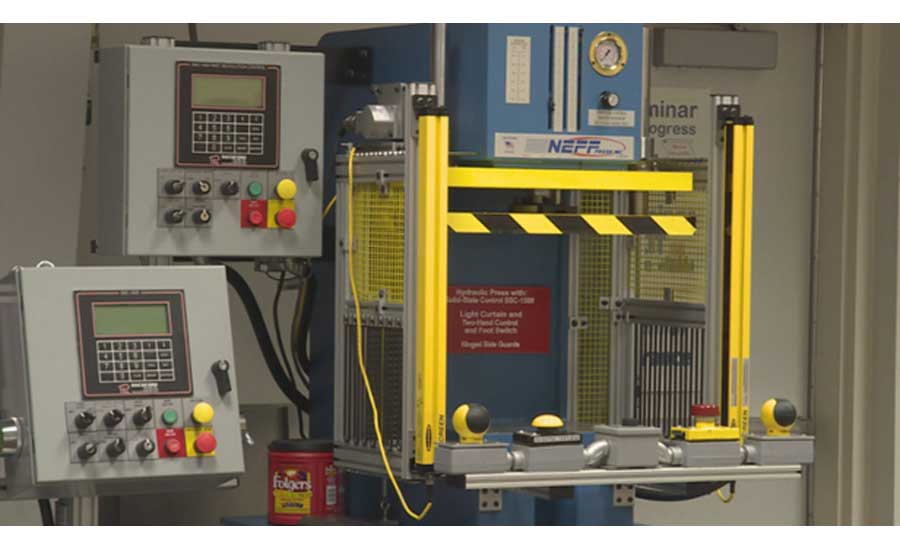
According to the Occupational Safety and Health Administration (OSHA), 49 percent of injuries from hydraulic power presses and press brakes result in the amputation of the operator's hand or fingers. Other bodily injuries include strangulation from loose clothing, and severe lacerations caused by material movement.
To turn the tables on press injuries Rockford Systems today introduced the second generation of its SSC1500 control system upgraded with encoder-based positioning technology. The SSC1500 Gen 2 is perfect for press OEMs and for replacing relay-based control systems in older machinery. The SSC1500 Gen 2 is available in two packages, one for hydraulic presses (FTL072) and the other for press brakes (FTL073).
By incorporating the encoder-based positioning feature, this best-in-class control system allows the press operator to set the stop positions for the ram from an LCD keypad display, eliminating the time-consuming process of manually adjusting limit switches. The incremental rotary encoder provides motion-related data, along with ensuring exact positioning of the ram with tolerances as good or better than using hard limits for the bottom of the stroke. As an additional safety feature, the SSC1500 Gen 2 has an external monitoring function assessing the state of the relays on every stroke to prevent potential failure. This feature is enabled when interfacing external relays for the down circuit.
Other upgrades exclusive to the press brake model are a selectable B-gate function to safeguard the operator from injury in the downstroke, along with job settings and bend programming options as standard.
CONTROL OPERATIONS
SC1500 Gen 2 controls allow press operators to run the slide down at high speed, stopping just above the workpiece at the point of hazard. Once the workpiece is properly positioned in the die, the operator could resume allowing the slide to finish the cycle through the bottom of the stroke in slow speed. This slow-speed action through the bottom of the stroke, avoids the fast whip-up action of the workpiece, protecting the operator
The SSC1500 Gen 2 is designed and built to comply with OSHA 29 CFR 1910.217, and ANSI B11.1 and B11.19.
For more information, visit www.rockfordsystems.com.
ABOUT ROCKFORD SYSTEMS
Headquartered in Rockford, Illinois, Rockford Systems, LLC delivers innovative machine safeguarding solutions for organizations working with industrial machinery. As a trusted adviser since 1971, Rockford Systems helps organizations interpret and apply complex Occupational Safety and Health Administration (OSHA) regulations and American National Standards Institute (ANSI) machine safety standards for a broad array of industrial applications. In addition, Rockford Systems provides complete Turnkey Machine Safeguarding Solutions, including machine safeguarding assessments, machine risk assessments, customized build-to-spec integration, over 10,000 safeguarding products, expert installation services, training and technical support, and ongoing compliance validation. Rockford Systems has improved the profitability of many of North America's largest companies by increasing compliance, reducing worker risk, enhancing productivity and decreasing costs.
Looking for a reprint of this article?
From high-res PDFs to custom plaques, order your copy today!