How one company turned its safety program around
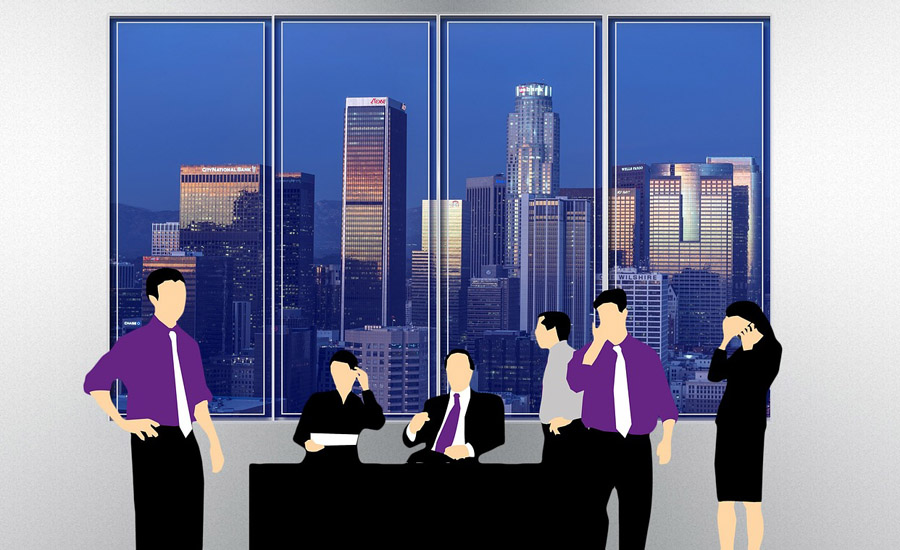
A Michigan company that couldn’t purchase workers’ compensation insurance because its injury rates were so high has radically changed its approach to safety, resulting in a significant reduction in its accident and incident rates and cost savings of about $30,000 a year.
Arnold Center Inc., a vocational rehabilitation services business that helps customers fulfill their employment needs, provides trained employees for in-house and off-site production in assembling, packaging, inspecting, sorting, and recycling.
No insurance company wanted their business
"At one point in Arnold Center's history, we found ourselves in the precarious position of not being able to purchase workers' compensation insurance on the open market due to an unusually high experience modifier," said Arnold Center Safety Director Greg Knopp. In 2007, the Center’s Experience Modifier Rate (EMR) was as high as 1.2, and no insurance company wanted its business. Because of its high EMR and expensive workers' compensation premium, the company knew that it needed to immediately work on improving their safety programs and remove the financial burden to their bottom line and their employees. In the meantime, an insurance agent assisted Arnold Center to obtain insurance through Michigan's risk pool. Even though the company was able to obtain the insurance, the agent reprimanded them for having a poor safety program.
Dealing with the high cost of workers' compensation and high injury rates was a wake-up call for Arnold Center to adjust their attitude and make safety a priority. In their search for a solution to a safer and healthier workplace, Arnold Center contacted the OSHA On-site Consultation Program – which they previously heard about via various media, seminars, and cold call visits. In 2007, Arnold Center began to work with the Michigan Occupational Safety and Health Administration (MIOSHA).
OSHA's On-site Consultation Program offers free and confidential safety and occupational health advice to small and medium-sized businesses in all states across the country and in several territories, with priority given to high-hazard worksites. On-site Consultation services are separate from enforcement and do not result in penalties or citations. Consultants from state agencies or universities work with employers to identify workplace hazards, provide advice on compliance with OSHA standards, and assist in establishing injury and illness prevention programs.
The Solution
June 9, 2008, MIOSHA conducted the first walkthrough of Arnold Center's worksite. The consultants identified several issues with the employer's Hazard Communication program and personal protective equipment. During the hazard correction process, Arnold Center implemented an in-house safety committee to work with Michigan OSHA, Consultation, Education, and Training (CET) Services consultants and workers' compensation representatives to find a solution and correct the identified hazards right away. Arnold Center's biggest challenge during the improvement and implementation to their health and safety management system was the overhaul and redesign of their safety program; the second biggest challenge was training their Safety Program personnel.
It was also at this point that Arnold Center willingly accepted their failure with the previous health and safety management system and realized that they needed to take control of their future. Arnold Center's team began the process of constructing a safer and healthier worksite with the assistance and dedication of their insurance agent and two extraordinary MIOSHA consultants. One key strategic implementation was the monthly safety meetings that vested staff with responsibilities to develop innovative safety practices that were followed up with On-site Consultation visits to confirm hazard corrections. With this new business practice and guidance from MIOSHA, the company became progressively proactive in their commitment to safety.
Another strategy that had a remarkably significant impact on Arnold Center's quick turnaround and progress was the invitation of external auditors to annually scrutinize the facilities and safety practices. The inspectors from various disciplines provided health- and safety-related recommendations which the employer dubbed action items. Their safety team meticulously addressed each action item by establishing policies and procedures and taking remedial action as appropriate. This structured and deliberate approach to safety improvement was a very effective way of ensuring the employer reaped the full rewards of the program.
The Impact
Over a span of just a few years, the employer's inspection recommendations became fewer and fewer as did the frequency of employee injuries. The EMR dropped to well below the industry's average. Arnold Center's EMR gradually decreased over the years from a high 1.2 in 2007 to a 0.82 in 2012, 0.77 in 2013, and 0.80 in 2014. The employer was able to reduce their EMR to as low as 0.77. Subsequently, Arnold Center's workers compensation premiums were reduced from being in the high risk pool to being self-funded. Soon, self-funded workers' compensation collaborates were seeking to join the employer's group.
Since the first consultation visit, Arnold Center's business practices have changed for the better. The employer instituted a monthly safety meeting which required collaborative efforts. They became more proactive in identifying hazards instead of reacting to high injury rates. As a result of their proactive approach to improving safety, Arnold Center realized a cost savings of about $30,000 per year. Overall, the employer has seen many successes, ranging from cost saving on their insurance premium to improved injury rates.
Arnold Center believes that their reduction of accidents and incidents is the direct result of their participation in the On-site Consultation Program. In 2013, Arnold Center's Total Recordable Case (TRC) rate was 2.8, and their Days Away from Work, Job Restriction or Transfer (DART) rate was 0. In comparison, BLS reports the national average for their industry in 2013 was TRC 5.5 and DART 2.9. In 2014, their TRC was 2.8 and their DART was 2.8. In comparison, BLS reports the national average for their industry in 2014 was TRC 5.7 and DART 3.2. In 2015, their TRC was 0.0, and their DART was 0.0. In comparison, BLS reports the national average for their industry in 2015 was 5.2 (TRC) and 2.8 (DART).
As Arnold Center's safety program continued to improve and become one of the best in their district, the MIOSHA CET consultant challenged the employer to work toward the prestigious Michigan Safety and Health Achievement Recognition Program (SHARP) award. SHARP recognizes small business employers who have used OSHA On-site Consultation Program services and operate an exemplary injury and illness prevention program. Acceptance of worksites into SHARP from OSHA is an achievement of status that distinguishes a company amongst its business peers as a model for workplace safety and health.
Arnold Center jumped at the challenge. Under the consultants' tutelage, the employer was awarded the Michigan SHARP award in May of 2009. Building on the success of the Arnold Center – Gladwin location, less than 2 years later, the company's Midland, Michigan, facility was also accepted into SHARP. Since 2009, the employer has maintained their SHARP compliance at two locations: Midland and Gladwin. In September 2016, the employer renewed their SHARP status. "We are very proud to receive this distinguished award," said Arnold Center Safety Director Greg Knopp. "It validates what is truly a team effort and commitment to make safety at the Arnold Center the number one priority. Thank you, MIOSHA for recognizing our team's dedication."
What's next for this safety conscious company? MIOSHA encouraged and challenged the team at Arnold Center to up the ante and aim for the Michigan Voluntary Protection Program (MVPP) Star Award, to which the team responded, "bring it on!"
Additional information about OSHA's On-site Consultation Program and other small business resources is available at www.osha.gov or 1-800-321-OSHA (6742).
Looking for a reprint of this article?
From high-res PDFs to custom plaques, order your copy today!