How to find the best footwear fit for specific hazards
The sole of construction
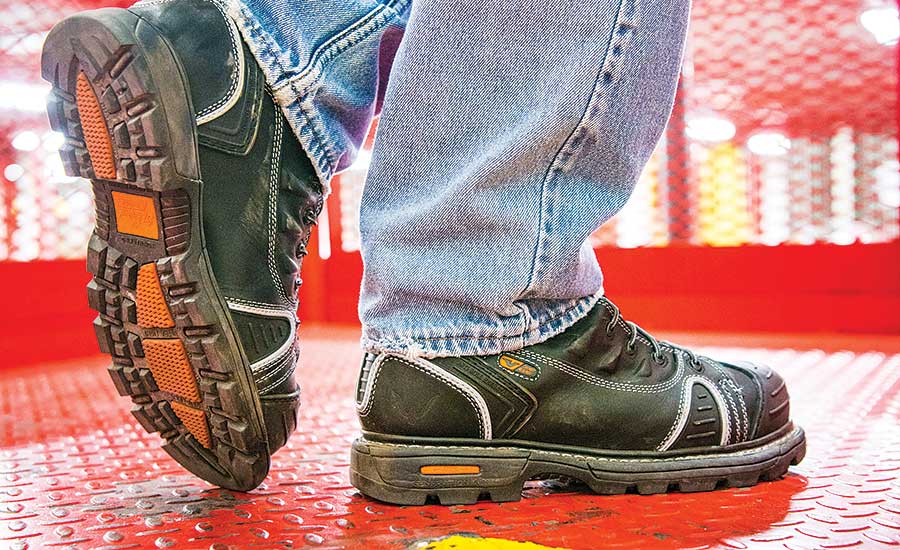
Have you ever wondered what the difference is between safety footwear that costs less than $100 and those that cost more than $300? While elements like quality of leather, name brand and where it was made factor into the final cost, the largest differentiator is the quality and type of construction.
Construction is the method by which the outsole is attached to the upper part of the shoe. Today, there are more than 800 known ways to attach an outsole to a shoe, but most are variations of four basic methods of construction. Different methods of construction offer different benefits in flexibility, weight, comfort and durability.
OSHA requirements
If an employer chooses to use personal protective equipment (PPE) in the workplace, like safety footwear, the Occupational Safety and Health Administration (OSHA) requires the companies to perform a PPE hazard assessment per 29 CFR 1910.132(d)(1):
“The employer shall assess the workplace to determine if hazards are present, or are likely to be present, which necessitate the use of personal protective equipment (PPE).”
If hazards are found, the employer may then have to provide the appropriate PPE to protect employees if engineering or administrative controls cannot eliminate the hazard. In the case of protective footwear, OSHA states in 29 CFR 1910.136 that employers must ensure each affected employee uses protective footwear that meets the criteria stated in the standard. Having a firm understanding of the construction will aid in the selection of appropriate safety footwear.
Footwear construction methods
Before diving into the four basic methods of construction of safety footwear, an understanding of the anatomy is needed first. The main structural components of safety footwear are:
- The outsole is the bottom of the footwear that comes in direct contact with the ground. It provides a measure of protection, and this is dependent upon the material from which it is constructed. Outsoles are made of a variety of materials with different tread designs.
- The midsole is the middle layer -- or layers -- that go on top of the outsole.
- The insole is the comfort layer that goes on top of the midsole and comes in direct contact with the wearer’s foot.
- The upper is the leather or canvas that is seen above the sole when a shoe is worn. While the upper can be broken down into many key items such as the vamp, the heel and the eyelets, as a whole, it is everything which covers the foot.
The four basic construction methods are:
- Welted: One of the oldest constructions and regarded as very sturdy and durable. There are a few variations such as the Blake and Goodyear methods, but the basic concept is the same. The welt (a strip of leather or plastic) is stitched to the upper and midsole. The outsole is then attached with adhesive to the bottom and may also be stitched through the welt.
- Cement: The least expensive, fastest, and most common method. The outsole is attached to the upper with strong adhesives which make the shoe lightweight and flexible.
- Opanka: Hand sews the upper, the sock lining and outsole in a single process. This construction allows for very flexible and comfortable fit and creates a cushioning effect.
- Heat Sealing: Also known as injection molding or vulcanizing. This method involves the upper being placed in a mold and a liquid synthetic soling material being injected which fuses or directly attaches the sole to the upper to produce a tough, watertight bond. This method is lightweight and the outsole is very long-wearing which extends the life of the footwear.
Outsole materials
Several different soling materials and compounds are used today. Different compounds offer different benefits. Five of the more common materials and benefits are:
- Rubber (RBR): The most widely used soling compound and made with the widest range of properties. Work sole versions have additives like nitrile or neoprene to enhance oil and chemical resistance. RBR is the best soling material available for maximum slip resistance and high heat resistance, and it can be formulated to high abrasion specifications. RBR can also be produced in dense/solid versions or blown lightweight versions. It can also withstand heat up to 570°F.
- Polyurethane (PU): A closed-cell blown material that has inherent properties of excellent oil and chemical resistance, except alkalis. Work sole compounds can be formulated with a high-abrasion factor for long wear and in dual-density versions to provide a high-abrasion bottom with excellent midsole cushioning. It has lower heat resistance in a range of 250 to 300°F. PU provides some slip-resistance properties.
- Thermoplastic Urethane (TPU): Has excellent abrasion and resistance to oil and chemicals. Most often used as a sole bottom material because of excellent wear properties. It has a lower heat resistance like polyurethane and fair slip resistance.
- Ethyl Vinyl Acetate (EVA): A blown open cell plastic based material with extreme lightweight properties. Ideal for its cushioning properties and is most often used as a midsole material. Good oil and chemical resistance but poor abrasion resistance, so it is most often combined with a polyurethane or rubber sole bottom.
- Polyvinyl Chloride(PVC): A plastic vinyl-based material that can be used for work soles or used as an additive to rubber for better abrasion and ozone resistance. Excellent abrasion and good cushioning as an outsole but susceptible to cracking in cold and has a low heat tolerance. Good slip resistance, but not as slip resistant as rubber.
Slip resistance
According to the National Floor Safety Institute (NFSI), 24 percent of slips, trips and falls are caused by improper footwear selection. An initial step in helping to prevent slips, trips and falls is selecting the correct style and sole designed for the work being done.
Consideration should be given to the type of flooring and type of contaminant (water, oil, grease, dust, etc.). Where water and other contaminants may be present, a less aggressive tread design with a greater amount of surface contact may be a better option. Slip-resisting tread designs consist of smaller patterns with sharp leading edges that act as a squeegee for better grip.
Currently, there is no one globally adopted standard for sole-slip testing. Since the 1980s, approximately 30 test methods have been developed by various organizations. Some are designed to assess footwear according to reference surfaces, while others assess ground and floor surfaces compared to a reference material. Due to so many differences in testing methods, they do not provide comparable results.
Some of the more common test methods are: ISO 13287-2012, SATRA TM144-2011, SATRA STM603, and ASTM F2913-11. Any of these test methods are generally accepted to rate soles and soling material by measuring the coefficient of friction (COF). Test results are rated on a scale of 0.0 (no slip resistance) to 1.0 (excellent slip resistance).
Ideally, to obtain comparable and relevant values, tests should be performed using a single method, with a surface and contaminant that resembles your work environment.
Conclusion
While no shoe or boot can claim 100 percent effectiveness, having a good understanding of footwear construction methods, sole materials and slip resistance properties will aid in proper selection of footwear to match the hazards present in your workplace.
Looking for a reprint of this article?
From high-res PDFs to custom plaques, order your copy today!