Inspect walking-working surfaces to identify hazards
Eliminate slip-ups
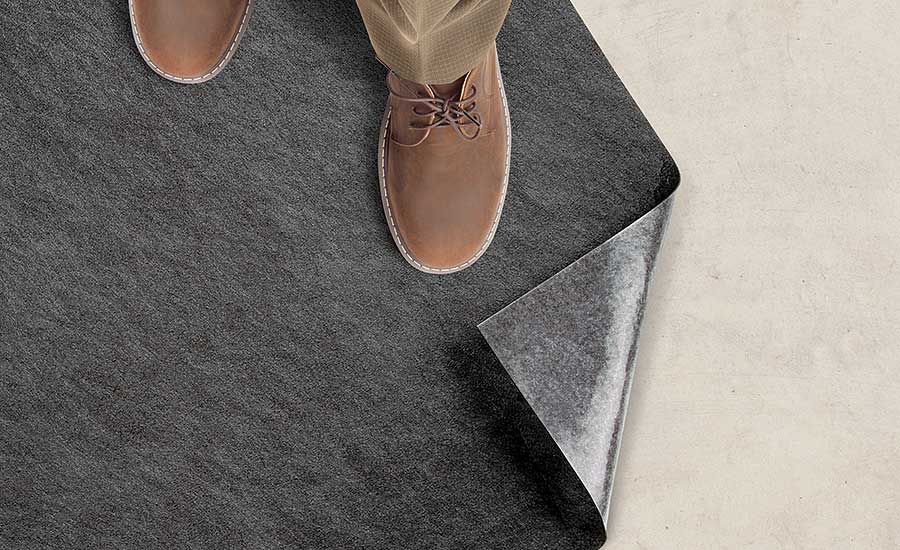
To help reduce same-level slip, trip and fall incidents, OSHA recently a provision to the walking-working surface rules for facilities to conduct regular inspections of all walking-working surfaces. This, coupled with the new requirement to fix any hazards that are found will help prevent slip, trip and fall incidents.
The new rule, which became effective January 12, 2017, will help to ensure that floors, aisles and other surfaces remain in good repair and are unobstructed to help prevent slip, trip and fall incidents. It will also require unsafe conditions, such as slippery surfaces, loose tiles, wrinkled carpeting, protruding nails and other obstructions be eliminated, not just acknowledged.
Regular inspections
Facilities have been required to have clean, dry floors for decades. Where this isn’t possible, floor mats, raised platforms or other control methods have also long been a requirement to help prevent slip and fall injuries [29 CFR 1910.22(a)]. Under the new rule, these requirements remain in effect.
However, there has never been a formal requirement to inspect walking and working surfaces to ensure compliance. The new rule adds “regular” inspections to help facilities maintain all walking-working surfaces in a clean, dry condition [29 CFR 1910.22(d)].
Facilities do have the liberty of determining how frequent those inspections need to be for each area of their facility. This reflects the understanding that some areas of a facility are used more often than other areas and that various types of walking surfaces may require more attention than others.
Carpeted meeting rooms and office areas that are in good condition and are cleaned regularly may only need a monthly inspection. The employee entrance which has a freshly polished floor will almost certainly require more frequent attention.
Evaluating the floors in each area of the facility and reviewing how often each area is used will help to determine inspection frequencies. Other variables, such as the age and condition of the floors in each area should also be taken into consideration and reviewed from time to time. In general, newer surfaces shouldn’t require as much attention as older ones. As a surface ages, inspections may need to become more frequent.
All inspections should verify that each walking-working surface is clean and dry, as far as that is feasible. But, other inspection items may vary for each area. For example, outdoor inspections may include having adequate provisions for snow removal and ensuing that sidewalks do not have any height variations greater than 1/4 inch. An inspection of a vinyl tile-covered hallway may include looking for loose or cracked tiles. Inspections in production areas that include wet processes may include having sufficient quantities of absorbents to clean up leaks and spills or squeegees to keep aisles clear.
Checking all areas
Because slip, trip and fall incidents can occur anywhere, all areas of the facility are subject to inspections, including production areas; aisles and hallways; outdoor areas; parking lots and common areas such as lobbies, cafeterias and breakrooms.
OSHA has specifically added the requirement to ensure safe access and egress routes [29 CFR 1910.22(c)]. These routes include aisles, ramps, stairways, ladders or any other means that employees use to get to work areas.
In addition to being kept clean and dry, all walking-working surfaces need to be kept free of obstructions that could cause a slip, trip or fall incident. These can include loose nails on wooden flooring, cracked and uneven concrete and carpets that buckle, curl or do not lay flat. Any object that protrudes into a walkway may also be considered an obstruction.
Guarding and eliminating hazards
Walking-working surface hazards may be identified during regular inspections. When this is the case, it is important to have processes in place for the information to be channeled to the right person or department for the hazard to be eliminated. In facilities that have well-established safety committees, assigning a committee member or subgroup to follow up on all variances can help to make sure that any hazards noted on inspection forms have been corrected.
Employees who work in various areas may also point out hazards that may not be obvious or that may be overlooked during regular inspections.
Unfortunately, walking-working surface hazards may also come to light as the result of an incident. Just as the findings from an incident should have a process for channeling and eliminating hazards, processes should also be established to find the root cause of an incident and eliminate that hazard.
No matter how a walking-working surface hazard comes to be identified, OSHA now requires it to be immediately eliminated or guarded until it can be corrected so that employees cannot walk on the surface and become injured [29 CFR 1910.22(d)(2)]. If the correction or modification affects the structural integrity of a walking-working surface, a qualified person must make the correction or modification [29 CFR 1910.22(d)(3).
Identified hazards may range from something as small as a coffee spill in a hallway to something much larger that affects the structural integrity of the walking surface. Employers may use temporary barricades, traffic cones, caution tape, guard rails or any other method that effectively prevents employees from walking over the surface until the hazard is eliminated.
Slips, trips and falls to the same level are among the top three leading causes of employee injuries. Establishing regular inspection schedules, putting processes in place to correct and eliminate those hazards and guarding them until those corrections can be made will eliminate the root cause of these common injuries.
Looking for a reprint of this article?
From high-res PDFs to custom plaques, order your copy today!