Five potential welding safety hazards to avoid
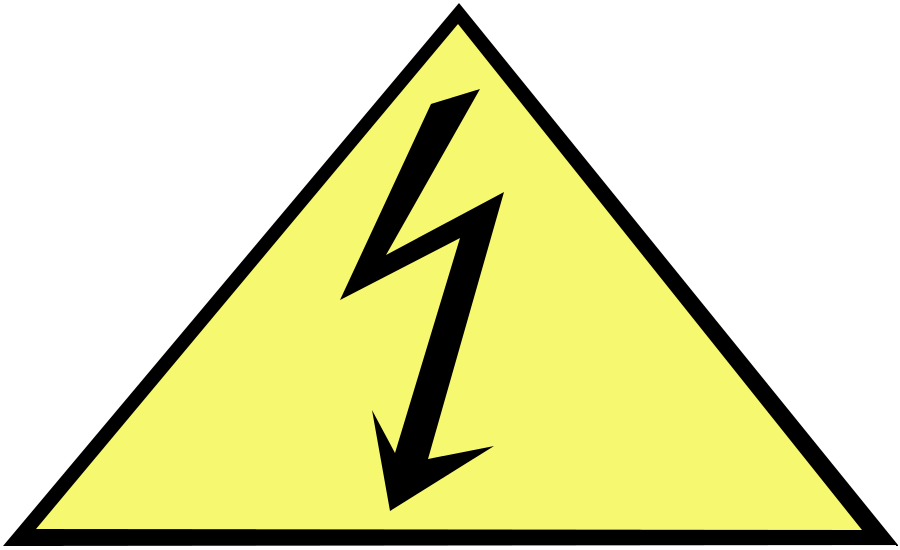
1 Electric shock
Electric shock is one of the most serious and immediate risks facing a welder. Electric shock can lead to severe injury or death, either from the shock itself or from a fall caused by the reaction to a shock.
Electric shock occurs when welders touch two metal objects that have a voltage between them, thereby inserting themselves into the electrical circuit. For instance, if a worker holds a bare wire in one hand and a second bare wire with another, electric current will pass through that wire and through the welding operator, causing an electric shock. The higher the voltage, the higher the current and, thus the higher the risk for the electric shock to result in injury or death.
The most common type of electric shock is secondary voltage shock from an arc welding circuit, which ranges from 20 to 100 volts. Bear in mind that even a shock of 50 volts or less can be enough to injure or kill an operator, depending on the conditions. Due to its constant change in polarity, alternating current (AC) voltage is more likely to stop the heart than direct current (DC) welders. It is also more likely to make the person holding the wire unable to let go.
To avoid secondary voltage shock, welding operators should wear dry gloves in good condition, never touch the electrode or metal parts of the electrode holder with skin or wet clothing and be sure to insulate themselves from the work and ground, keeping dry insulation between their body and the metal being welded or ground (such as a metal floor or wet surface).
Welding operators also should inspect the electrode holder for damage before beginning to weld and keep the welding cable and electrode holder insulation in good condition, because the plastic or fiber insulation on the electrode holder prevents contact with the electrically “hot” metal parts inside. Always be sure to repair or replace damaged insulation before use. And remember, stick electrodes are always electrically hot, even when welding is not being done and the voltage is the highest.
2 Fumes and gases
Overexposure to harmful complex metal oxide compounds from consumables, base metal and the base-metal coatings is a real risk, so it’s important to keep your head out of the fumes and use enough ventilation and/or exhaust to control your exposure to substances in the fume, depending on the type of rod and base metal being used.
The specific potential health effects which relate to the welding consumable product being used can be found in the Health Hazard Data section of the Safety Data Sheet available from your employer or the consumable manufacturer.
Welding areas require adequate ventilation and local exhaust to keep fumes and gases from the breathing zone and the general area. In most situations, employers will provide a ventilation system- such as a fan, and an exhaust system or fixed or removable exhaust hoods- to remove fumes and gases from the work area.
All welding operators should be aware that there are ACGIH threshold limit values (TLV) and OSHA permissible exposure limits (PEL) for the substances in welding fume. These limits specify the amount of a substance in your breathing air to which welding operators can be exposed every day they work over the course of their career. Welding operators should wear an approved respirator unless exposure assessments are below applicable exposure limits.
An industrial hygienist takes an air sample in the worker’s breathing zone to determine whether a worker’s exposure is below the exposure limits.
If the air in your breathing zone is not clear, or if breathing is uncomfortable, check to be sure the ventilation equipment is working and report concerns to a supervisor so your exposure to substances in the welding fume can be checked. This is especially important when welding with stainless steel or hard-facing products. To prevent exposure from coatings such as paint, galvanizing, or metal platings on base metals, clean the base metal before beginning to weld. See a doctor if symptoms from overexposure persist.
3 Fire & explosions
The welding arc creates extreme temperatures, and may pose a significant fire and explosions hazard if safe practices are not followed. While the welding arc may reach temperatures of 10,000 degrees Fahrenheit, the real danger is not from the arc itself, but rather the intense heat near the arc and the heat, sparks and spatter created by the arc. This spatter can reach up to 35 feet away from the welding space.
To prevent fires, before beginning to weld, inspect the work area for any flammable materials and remove them from the area. Flammable materials are comprised of three categories: liquid, such as gasoline, oil and paint; solid, such as wood, cardboard and paper; gas, including acetylene, propane and hydrogen.
4 Injuries from insufficient PPE
Personal protective equipment (PPE) helps keep welding operators free from injury, such as burns – the most common welding injury – and exposure to arc rays. The right PPE allows for freedom of movement while still providing adequate protection from welding hazards.
Leather and flame-resistant treated cotton clothing is recommended in welding environments. This is because synthetic material such as polyester or rayon will melt when exposed to extreme heat. Welding leathers are especially recommended when welding out of position, such as applications that require vertical or overhead welding.
Avoid rolling up sleeves or pant cuffs, as sparks or hot metal will deposit in the folds and may burn through the material. Keep pants over the top of work boots – don’t tuck them in. Even when wearing a helmet, always wear safety glasses with side shields or goggles to prevent sparks or other debris from hitting the eyes. Leather boots with 6-to-8-inch ankle coverage are the best foot protection; metatarsal guards over the shoe laces can protect feet from falling objects and sparks. It will not be pleasant if a hot piece of spatter finds its way inside your clothing or shoes.
Heavy, flame-resistant gloves should always be worn to protect from burns, cuts and scratches. As long as they are dry, they also should provide some protection from electric shock. Leather is a good choice for gloves.
Helmets with side shields are essential for protecting eyes and skin from exposure to arc rays. Make sure to choose the right shade lens for your process – use the helmet’s instructions to help select the right shade level. Begin with a darker filter lens and gradually change to a lighter shade until you have good visibility at the puddle and weld joint but it is comfortable and does not irritate your eyes. Helmets also protect from sparks, heat and electric shock. Welder’s flash from improper eye protection may cause extreme discomfort, swelling or temporary blindness, so don’t take any risks – wear a helmet at all times during welding.
To protect ears from noise, wear hearing protection if working in an area with high noise levels. Doing so will protect your hearing from damage, as well as well prevent metal and other debris from entering the ear canal. Choose ear plugs or ear muffs to protect the ears.
5 Other safety considerations
Welders working in a confined space or in an elevated area may need to take extra precautions. In any welding situation, welding operators should pay close attention safety information on the products being used and the material safety data sheets provided by the manufacturer and work with their employer and co-workers to follow appropriate safe practices for their workplace.
Good common sense is also key. If opening cans of electrode, keep hands away from sharp edges. Remove clutter and debris from the welding area to prevent tripping or falling. And never use broken or damaged equipment or PPE. To keep up with the most recent safety practices, welding operators should utilize resources from the American Welding Society (AWS), OSHA and welding manufacturers, such as Lincoln Electric’s online Interactive Safety Guide. By following these safe practices and using common sense, operators can stay safe and keep production moving with no lost-time accidents.
Source: Lincoln Electric
Looking for a reprint of this article?
From high-res PDFs to custom plaques, order your copy today!