Advances in glove protection, dexterity, durability & comfort
The revolution is at hand
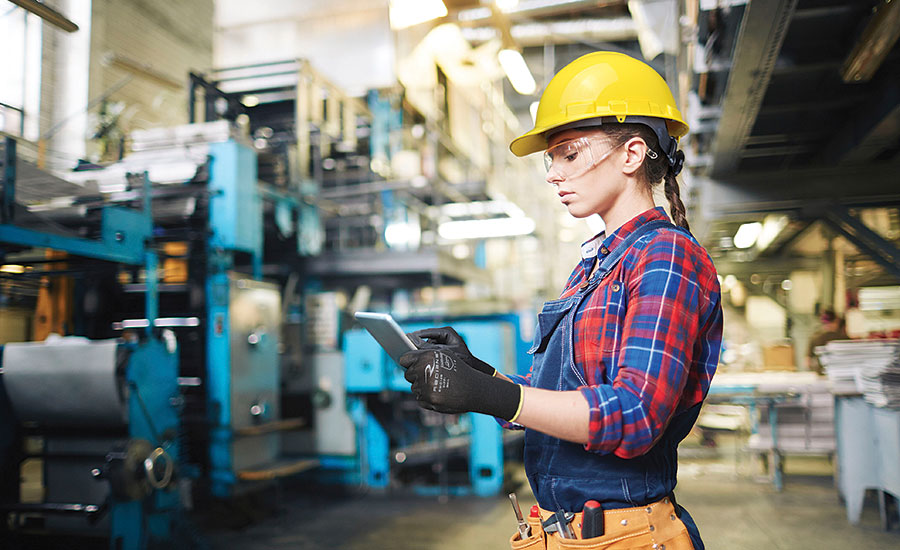
According to a study conducted by the U.S. Bureau of Labor Statistics (BLS), 70 percent of workers suffer from hand injuries simply because they don’t wear hand protection. Workers complain that work gloves aren’t comfortable and prevent dexterous hand movements, often slowing down their productivity. “The other 30 percent of workers,” says the BLS, “wear gloves that are “inadequate, damaged or wrong for the type of hazard.”
Fortunately, these statistics will improve in the coming years because technological advances will revolutionize hand protection by providing extra protection, dexterity, durability and comfort.
Potential for variety of injuries
In today’s work environment, hand injuries are the second leading cause of work-related injury— back and neck sprains and strains take first place. The most common causes of hand injuries are blunt trauma followed by cut and laceration injuries from a sharp object, which account for one-third of hand injuries.
Because our hands have an intricate structure and a complex anatomy, the potential for a variety of injuries exists. Human hands are truly amazing and are definitely worth protecting properly. The cost of a hand injury can far exceed the cost of a hand protection safety program.
The BLS reports that today the average hand injury claim exceeds $6,000 coupled with a typical worker’s compensation claim of $7,000 for a total of $13,000.
OSHA’s top eight hand injuries
OSHA dictates that employers must use PPE to provide additional protection against hazards that can’t be completely eliminated through other measures. According to OSHA, 70.9 percent of arm and hand injuries could have been prevented with PPE, specifically safety gloves. The hand injuries that employers need to protect against include:
- Burns
- Bruises
- Abrasions
- Cuts
- Punctures
- Fractures
- Amputations
- Chemical Exposures
Prevention
How can employers help prevent the eight hand injuries listed above? They can (1) evaluate jobsite risks, (2) teach employees about the hazards, and (3) provide the proper hand protection for the application.
1. Evaluate jobsite risks by asking the right questions:
- What engineering and work practice controls need to be in place to help prevent hand and
- finger injury?
- What tools and equipment will your workers use?
- Does the equipment have built-in safeguards to protect against pinching when exposed to moving machine parts? Are there barriers between your workers’ hands and the saw blade?
- Are your workers wearing jewelry that can get caught in machinery? Thousands of employees are injured every year when a ring or bracelet gets caught in a moving machine part.
- Does the worker have to handle heavy equipment or machinery where fingers and hands are easily crushed?
You can always consult with a safety specialist, safety engineer, or product manager to help you evaluate the potential areas and risk factors that can lead to hand and finger injury at your jobsite.
2. Teach & train: One of the best ways to behaviorally teach and train is to role play or simulate a hand injury. Tape up an employee’s dominant hand with gauze then instruct him or her to perform a couple of simple work tasks and a personal task like texting. The simulation drives home how debilitating a hand injury can be and will help increase compliance.
Have a glove show & tell: Display several different types of gloves and talk about the specific application for the glove. Reiterate the importance of using the right glove for the right task. As was mentioned earlier, 30 percent of hand injuries are a result of using the wrong or inadequate glove for the job.
3. Outfit workers with hand protection specifically designed for the hazards of the jobsite:
OSHA says, “It is essential that employees use gloves specifically designed for the hazards and tasks found in their workplace because gloves designed for one function may not protect against a different function even though the glove may appear to be an appropriate protective device.” Below are three types of safety gloves, all of which have revolutionized hand protection.
3 gloves that are revolutionizing hand protection
Cut-resistant gloves: The use of cut-resistant gloves has increased considerably. Glove fabrics and coatings have been improving at a fast and furious pace; thus, cut-resistant gloves are thinner, more comfortable, and provide greater protection.
Those who work around sharp blades or who are exposed to risks of cuts and lacerations, will need to wear cut-resistant gloves. The gauge and cut level required will depend on the specific task.
Impact Resistant Gloves: Impact resistant gloves, also known as anti-impact gloves, feature dense thermal plastic rubber pads or overlays strategically located along the top of the hand and along fingers to help protect from crushing blows.
TPR provides maximum cushioning while not interfering with dexterity. Workers in oil drilling, automotive, and heavy manufacturing environments benefit greatly from TPR technology.
Coated gloves: Numerous types of coated gloves are available today, which include foam coated, high-visibility coatings, PU palm coated, crinkle latex coated, and the list goes on.
Prominent features of coated gloves include seamless design, breathable knit back, elastic cuffs, and a variety of gauges. When wearing coated gloves, workers are also able to move their hands more freely and easily in cold conditions. Plus, coated gloves give additional skin protection from harmful chemicals and oils.
Coated gloves are ideal for jobs that require a high degree of touch-sensitivity, dexterity, and a superior grip.
In 2017 the number of hand and finger injuries should drop significantly as compliance and proper glove specifications improve through technology, innovation, training and motivation. Let’s all work together in 2017 to reduce the number of hand injuries that plague our jobsites.
Looking for a reprint of this article?
From high-res PDFs to custom plaques, order your copy today!