The five Ws of chemical inventory management
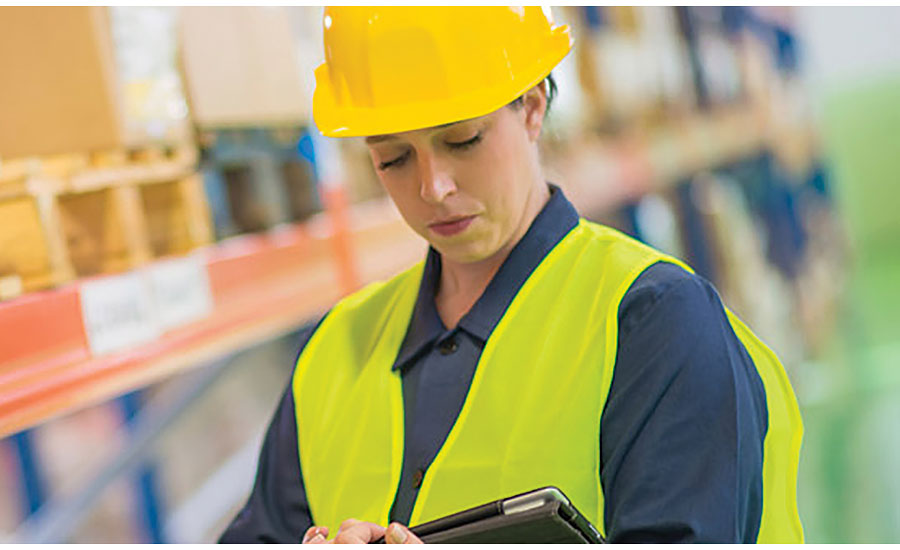
Imagine the owner of a small repair shop regularly purchases two cases of the same brake fluid every month. One month, the shop consumes every container and hurriedly buys an emergency case of a different brand of brake fluid, without collecting a Safety Data Sheet (SDS) for the new material. After using two bottles, the remainder of the case remains in the warehouse, forgotten and unused. The shop EHS manager, unaware of the purchase, has no SDS to show the compliance officer during the next regulatory inspection, and the small repair shop incurs a $1,000 fine for not collecting and storing the SDS for a forgotten, dusty box of brake fluid. This amount might not seem significant for large corporations, but for a small business, one penalty could be detrimental. Applied on the corporate level, the same scenario could incur hundreds of thousands of dollars in fines and penalties for non-compliance.
Keeping a proper and updated inventory is crucial to the success of any business — not only to avoid penalties but to maintain operational safety and business development. Effective Chemical Inventory Management begins with the acknowledgement of what materials are currently on site and responsibilities associated with the materials. Exploring the five Ws of chemical inventory management helps drive best practices for your organization and provides a safe and secure foundation to meet safety standards.
Why is chemical inventory management important?
Companies often use electronic or manual methods of recording inventory data and, shockingly, some companies assume the risk of having no standard method of inventory management at all. However, inventory is crucial in four areas of any industry:
Workplace safety. The Department of Labor reported 3 million work-related injury and illness cases in 2014. Keeping a safe and secure working environment for employees and the surrounding community should be paramount to any organization.
Regulatory compliance. Next to fall protection, HAZCOM standards incurred the second most frequently violated OSHA standards in 2015. As of August 2016, each serious violation can accompany a penalty of up to $12,471. Compliance includes state and federal responsibilities, up-to-date SDS lists and awareness of hazards associated with materials on site.
Contractual obligations. Chemical inventory management enables manufacturers and suppliers the opportunity to govern and report any breach in material agreements during production.
Business strategies. Campaigns such as environmentally friendly initiatives can be impacted by proper inventory as organizations drive strategic initiatives in information-based innovation.
What should organizations know before beginning an inventory?
While preparing for inventory, personnel should be informed of three requirements: what items are needed, what must be inventoried and which materials need a SDS. Personnel conducting the inventory should be equipped with necessary PPE to protect from hazardous materials, devices to log data and flashlights to access all areas within a facility.
Every unique material within the facility must be counted. For example, not only do red and blue paint containers from a single manufacturer require unique logs but red paint from different manufacturers also require separate logs. When recording materials, specialists capture data such as the area located or stored, product name, manufacturer and product codes to provide adequate information to further examine each material.
Where is inventory conducted?
The simple answer is… everywhere. Best practices begin with the area containing the most materials, working methodically clockwise or counter-clockwise throughout each area and spiraling to the center. This technique couples with investigating the four Cs: every Corner, Cabinet, Closet and Container in a chemical area or facility.
Who should be involved in chemical inventory?
Inventory is an ongoing task that requires leadership buy-in for policy and process development, technology for efficient data collection and communication within the organization among buyers and EHS managers to monitor product variations or regulatory changes that might affect inventory results or compliance.
Faced with the task of surveying a facility, many organizations find inventory cumbersome and daunting. A team of trained, experienced specialists are best suited to undertake the mission—not only examining the facility for materials, but recording necessary data to document materials and acquire relevant SDSs.
When should organizations conduct full inventories?
A full inventory should be conducted every 12-18 months. A wash, rinse and repeat method helps maintain proper records, ensure operational safety and engage proper risk management.
Reconciliation services enable specialists to compare inventory results with an organization’s current SDS documents to determine which documents are needed to provide a safe and compliant workplace. Maintaining an inventory properly and reconciling it with documentation establishes a programmatic workflow that sets business up for success in an ever-changing industry.
Looking for a reprint of this article?
From high-res PDFs to custom plaques, order your copy today!