3D printers hold potential, but control measures are critical
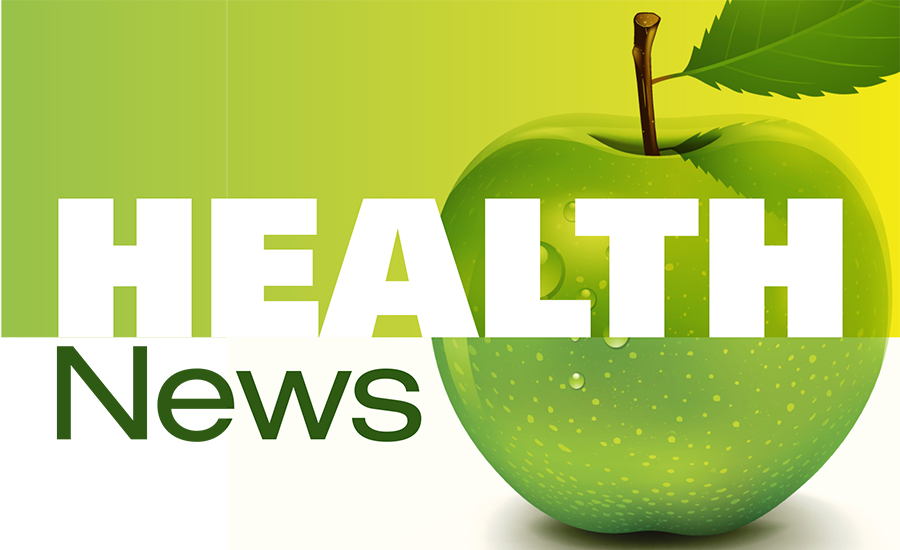
An industrious college student recently made the news for straightening his own teeth with braces that he made on his school’s three-dimensional (3D) printer. From braces, hearing aids, and prosthetics, to military equipment, the list of products that 3D printers can make relatively easily and cheaply continues to expand. The National Institute for Occupational Safety and Health (NIOSH) warns, though, that as with all new technologies, it is important to identify and address potential workplace health and safety risks.
To understand how 3D printing works, picture plastic Lego blocks, which snap together to form all kinds of elaborate 3D structures. Similarly, the most common type of desktop 3D printer technology joins thin strands, or filaments, made of plastic or natural materials, such as corn. Following a computer-generated image, the 3D printer uses heat to melt and place layers of filament on top of one another to form a precise 3D replica of the image.
As desktop 3D printers become more affordable, they are used more often in offices, public libraries, colleges, and even private homes. Most of these settings do not have controls, like ventilation, to prevent or minimize exposure to emissions.
Previous studies showed that laser printers emit microscopic particles and chemicals from the printers themselves, the paper, and the plastics used in the toner. NIOSH investigators continue to study the possible health effects related to these particles and wanted to find out whether 3D printers have similar emissions.
Working with university partners, NIOSH investigators measured emissions from a desktop 3D printer in a specially designed test chamber that simulates real-world conditions. They found that the tested desktop 3D printer released high numbers of particles as it printed. The emissions peaked a few minutes after printing began, and they did not return to baseline until about 100 minutes after printing ended.
The emissions also varied by filament type and color. Filaments made from natural materials like corn emitted smaller particles than plastic filaments did. This could be because the oil-based plastic particles were more likely to form clumps, according to the investigators. Calculations showed that the risk of the particles lodging in the lungs was 3 times higher for the small particles made from natural substances compared with the larger plastic particles. Color also affected particle size, with natural corn-based filaments in the color true red emitting the smallest particles, on average. In contrast, blue plastic filaments emitted the largest particles.
Investigators found that using the manufacturer-supplied cover on the printer decreased the number of particles by two times, but the reduced number was still high. These findings underscore the importance of using controls to reduce emissions from desktop 3D printers in non-industrial settings. To reduce emissions, the investigators recommend five specific steps:
- Always use the manufacturer’s supplied controls (full enclosure appears more effective at controlling emissions than a cover).
- Use the printer in a well-ventilated place, and directly ventilate the printer.
- Maintain a distance from the printer to minimize breathing in emitted particles, and choose a low-emitting printer and filament when possible.
- Turn off the printer if the printer nozzle jams, and allow it to ventilate before removing the cover.
- Use engineering measures first, such as manufacturer-supplied equipment and proper ventilation, then use materials with lower emissions. Finally, wear protective equipment, such as respirators.
The peer-reviewed Journal of Toxicology and Environmental Health published the study.
Looking for a reprint of this article?
From high-res PDFs to custom plaques, order your copy today!