Minimizing construction risks from employee turnover
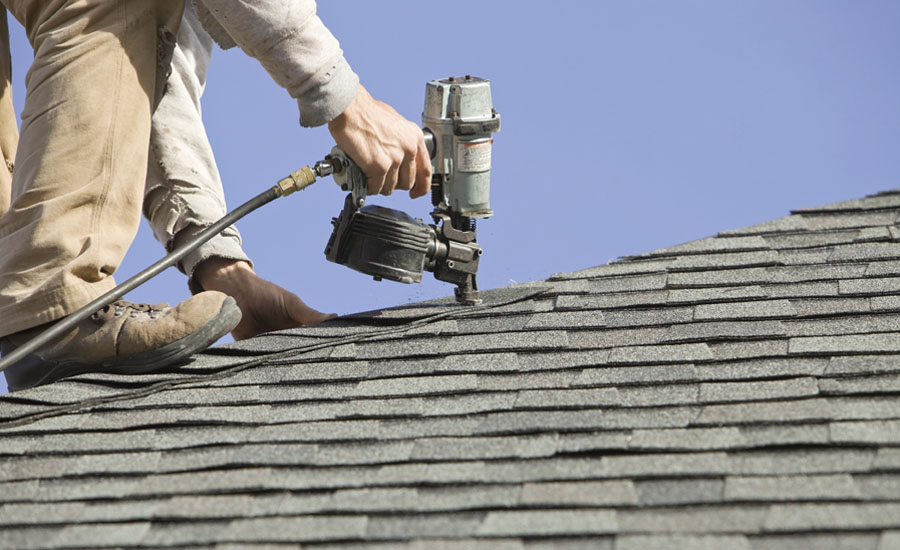
Photo credit: Getty Images
It cannot be stressed enough that safety should be paramount on the construction jobsite.
Unfortunately, some things work against safety; employee turnover is one of them.
The turnover in construction was about 20% in 2014, which is actually under the national average across all professions but is high for the industry. For workers 25 years old and under, that turnover rate reached 38%. As with every other industry, an improving economy makes it easier to switch to a better paying job.
Causes and Costs of High Turnover in Construction
By its nature, construction tends to be a transient business where the employees are hired on a project-by-project basis, more like temporary or contract workers than full-time employees. They cannot be assured the workplace will be the same from one day to the next, and their workmates change often. Constant change makes it difficult to maintain safety standards.
Add to this the fact that construction workers are more likely to be injured in the first 30 days on the job. For most people, the first month on a new job is hectic enough. Add heavy equipment and materials and the possibility of getting hurt before complete orientation becomes much higher.
The upshot of this is that the cost of turnover, both direct and indirect, comes to about 20% of an unskilled employee's annual pay and benefits package. That isn’t the worst of it. These same costs rise to 150% when talking about skilled workers.
Direct Costs
· Termination
· Replacement
· Transition costs
Indirect Costs
· Loss of production
· Reduced performance levels
· Unnecessary overtime
· Low morale
High Turnover Exacerbates Common Safety Issues
You are already aware of the most common safety issues on a construction site: falls due to lack of safety equipment and training. The desire to control costs and make a profit can lead to unwise cost-cutting. The result can be unnecessary accidents and injuries, a higher number of insurance claims, and other costs.
To add to the misery, the hiring standards may be lowered to find workers, putting younger and much less skilled workers at risk. Younger supervisors may be unfamiliar with safety requirements and remain unaware of the industry's new emphasis on risk management.
Solutions to High Turnover and Safety Issues
The first step is to cultivate effective leadership at all levels of your business that can build a culture of safety across all functions of the company. Develop leadership skills that far exceed minimum standards. Your leadership must foster a positive work environment and drive discretionary effort to increase safety training and awareness.
Your employees need to be able to count on that leadership to hear and handle their concerns fairly and promptly. They should be guided through adequate training and remain engaged in ongoing safety efforts. Let your employees see what the impact of safety has on budgeting, scheduling, quality, and the work environment. Make them partners in workplace safety.
Stay ahead of the curve with continuous safety improvement:
- Plan appropriately to address existing and potential safety issues.
- Let all employees know about safety standards and planned controls.
- Emphasize to management and supervisory staff the importance of observation and enforcement of compliance.
- Empower the workers themselves to intervene when needed to help protect fellow workers.
To maximize awareness, review the safety programs and processes on a regular basis to make improvements.
Training is crucial, especially for those in management and supervisory roles. These are the leaders on the frontline of risk management. They link the directives of upper management and the employees those directives impact. Contractors should conduct management orientation and training in all responsibilities regarding policies and procedures facilitating occupational safety and health.
Demonstrate Your Commitment to Safety
Write down the rules and procedures, and then post them where everyone can see them. Train those supervisors onsite so they are familiar with this specific project’s needs. When you are hiring and evaluating supervisors include the ability to follow protocol as one of the key skills required for the position.
The same goes for other employees. Make sure everyone understands the safety procedures before they begin working on the project. The direct impact will be a cost reduction that correlates with the reduction of accidents and morale will improve significantly.
Safety on a construction site is paramount, but high employee turnover represents a step backward from that goal every time a worker is replaced. Those first 30 days are the most dangerous. By working to retain employees their chances of injury and fatality and the number of insurance claims you file will be vastly reduced.
Looking for a reprint of this article?
From high-res PDFs to custom plaques, order your copy today!