ASSE comments on OSHA Safety and Health Program Management Guidelines
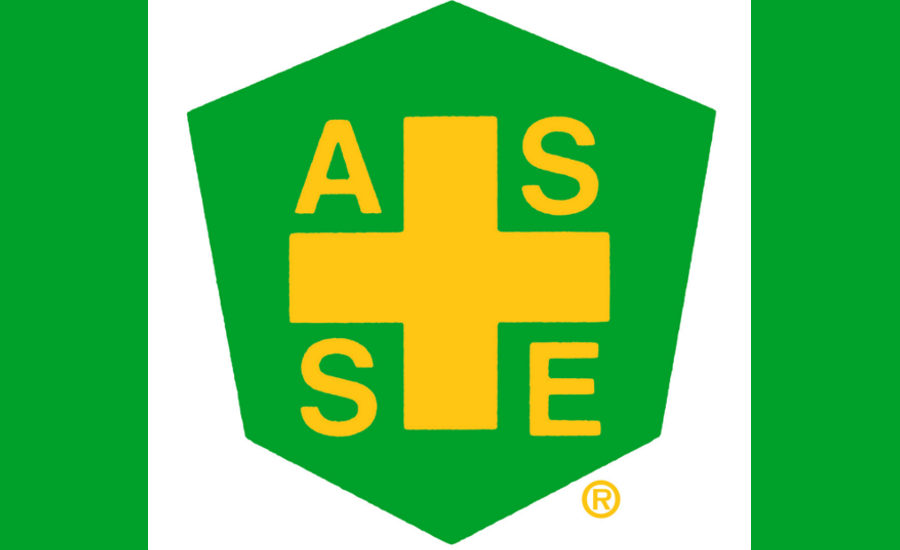
Letter from American Society of Safety Engineers (ASSE) President Michael Belcher, CSP to Dr. David Michaels, Assistant Secretary, Occupational Safety and Health Administration (OSHA):
The ASSE congratulates OSHA for revising and updating its Safety and Health Program Management Guidelines. ASSE is disappointed that this Administration did not complete rulemaking to consider requiring every employer to adopt a safety and health management program. Nevertheless, if a standard could not be accomplished, OSHA has done the right thing by taking the time and considerable effort to update its 1989 Guidelines.
In 2016, we know much more about safety and health management systems than was known three decades ago. New occupational safety and health challenges have emerged. Better resources for employers to implement management systems exist. Several effective voluntary consensus standards are now available to employers to help them implement systems. OSHA’s draft gives the safety and health community a timely opportunity to come together to build a lasting document that can advance acceptance of a game-changing tool to save lives and reduce injuries and illnesses in US workplaces. ASSE is committed to partnering with OSHA to find effective ways to spread the message of good news these updated Guidelines have for all employers and workers.
As ASSE has often said, safety and health management systems represent the highest expression of our members’ professionalism. Safety and health professionals develop and implement management systems to help the most successful US employers enjoy significant reductions in deaths, injuries and illnesses in their workplaces and achieve better fiscal results. The benefits these best companies enjoy from adopting the kinds of risk-based management concepts the Guidelines encourage can and should be experienced in all workplaces, including the smallest. To help ensure the Guidelines achieve the goals we all share for them, ASSE offers the following suggestions based on the leadership of our members in championing safety and health management systems.
Prevention through Design (PtD)
In the Hazard Identification and Assessment section, ASSE strongly urges inclusion of Prevention through Design (PtD) in the process. PtD is at the cutting edge of what the safety and health profession knows about how to protect workers. Design review has always been a well-accepted practice in the hazard identification process. Safety and health professionals have long advocated the importance of “designing out” hazards before they appear in the workplace. The PtD approach ingrains the hierarchy of controls into the design of new operations and also in the review of existing operations after significant accidents and re-designs of operations. This cradle-to-grave design approach significantly enhances the opportunities for reducing risk in the workplace.
Through the efforts of forward-thinking safety and health professionals, safety researchers, and the excellent leadership of the National Institute for Occupational Safety and Health’s PtD program (http://www.cdc.gov/niosh/topics/ptd/), organizations are already succeeding in achieving worker protections and savings by incorporating safety considerations in their design process. Guidelines that do not encourage employers to know that the hazard identification process begins before a machine is built or a building is constructed will be outdated on publication.
Encouraging a systems approach to safety and health management
The seven core elements of OSHA’s proposed revision are excellent, as is guidance on how to implement these elements that OSHA has included. ASSE encourages OSHA to take its message a step further by better communicating that the way to achieve success in the core elements is by taking a systems approach.
A systems approach embraces a more holistic view of safety and health management, with each core element an important part of a whole. A more systematic approach also heavily engages both management as well as the workforce in this process, as OSHA recognizes, but it also encourages organizations to go more upstream in the risk assessment process. The systems approach also recognizes that every hazard cannot be eliminated but that the risks these hazards pose can be assessed, prioritized and addressed in any organization. This flexibility in managing risks is highly effective in the workplace, our members report.
To better establish an understanding of the systems approach, the Introduction could be expanded with a relatively short section that encourages readers to think of the seven elements as a part of a systematic whole, with each element dependent on the other. References to voluntary consensus standards that advance the systems approach should be included to encourage employers, especially larger employers, to develop management systems consistent with the best practices already widely accepted throughout industry. ANSI Z10 Occupational Health and Safety Management Systems, ISO 45001 Occupational Health and Safety Management Systems currently under development, and ANSI A10.33-2011 Safety and Health Program Requirements for Multi-Employer Projects are widely adopted standards that must be referenced if the Guidelines and employers who follow the Guidelines are to be consistent with industry best practices.
Appropriate reliance on occupational safety and health professionals
The knowledge and capabilities of occupational safety and health professionals have grown significantly since 1989. The days of appointing just anyone as the “safety guy” are long gone in all large and most mid-size organizations. Increasingly, employers understand the need for safety and health professionals with the training and expertise to address and implement the various components of the suggested guidelines. This is a development that every occupational safety and health stakeholder should applaud.
While there is some recognition of this reality in the current draft of the Guidelines, ASSE urges OSHA to include language that would help make employers aware that, in high-risk work sites, in complex operations, in workplaces that have experienced deaths, injuries or illnesses, and in larger organizations, it may be appropriate to engage an occupational safety and health professional to develop a safety and health management plan. This information is especially needed in the Hazard Identification and Assessment section where “safety and health consultants” and, OSHA’s 1926.20(b)(2) “competent person” requirement are mentioned but no guidance given on when a consultant might be considered.
Also, without professional licensing or common certification in the occupational safety and health profession, many employers who will be developing safety and health management plans will not know who to look towards as consultants. Employers increasingly look to the nationally accredited certifications of the Board of Certified Safety Professionals (http://www.bcsp.org/) and American Board of Industrial Hygiene (http://www.abih.org/) to help ensure the competence of the people they rely on to write programs and otherwise manage workplace safety and health risks.
To assist especially those employers who will be new to developing plans, ASSE urges OSHA, at the very least, to expand “Safety and health consultant” on page 12 of the draft to read,
Safety and health consultant with nationally accredited occupational safety and health certifications, especially in high-risk worksites; when worker deaths, injuries and illnesses have occurred; in complex operations or larger organizations; and on multiemployer worksites.
It is not OSHA’s responsibility to help advance the occupational safety and health profession or to create jobs for ASSE members. The profession is as fully employed as any profession without OSHA’s assistance. We do, however, believe OSHA has a responsibility to help employers understand all the ways they can make their workplaces safer and healthier. Encouraging employers to engage competent professionals when appropriate is fully consistent with OSHA’s mission.
Yet, ASSE fully knows that workplace safety and health is not the responsibility only of a safety and health professional. Everyone in an organization is responsible. For safety and health programs to be successful specifically, safety-competent supervisors, crew leaders and foreman are essential. The Management Leadership and Education and Training sections include supervision at all levels and recommend awareness-level training for them. However, that suggestion does not go far enough. ASSE urges OSHA to consider even greater emphasis on the need for safety-competent supervisors. Our members do not view safety awareness-level training as adequate for supervisors.
Small employers
ASSE applauds OSHA's efforts to address small employers in the Guidelines. Consistent with what we believe OSHA intends, the final Guidelines must point small employers to resources that can help them understand how to use the Guidelines and how management systems can be used in small businesses. ASSE encourages OSHA to use its cooperative relationships with a variety of stakeholders, especially small employer contractor and business groups, to develop tools needed by even proverbial “two-guys-and-a-truck” contractors.
Safety and health professionals help even the smallest employers achieve systematic understanding of risks through approaches as basic as simple checklists of risks. We know small employers can achieve what the best employers achieve in safe and healthy workplaces, but they will need assistance from OSHA and mentorship from the business and safety and health community. ASSE and our members can be a resource for such information, and we look forward to working with OSHA and other stakeholders to help build the resources needed to reach the needs of businesses, both small and large.
Program evaluation and improvement
Another area of the Guidelines that can and should be strengthened is in urging employers to evaluate their safety and health management programs and providing suggestions on how to measure improvement. Further, ASSE does not think it is too unreasonable to expect the Guidelines to provide some information to encourage employers to think about using leading instead of lagging indicators in such evaluations.
ASSE has suggested in the past that OSHA bring together stakeholders to develop more useful resources to encourage the use of leading indicators and has objected to OSHA policies that do not encourage their use. Final Guidelines with references that support employers’ use of measurements already used by the safest and healthiest organizations could be an opportunity to advance the creation of better resources to advance the use of leading indicators in safety and health management programs.
Resources
The following is a list of the resources ASSE urges OSHA to include in a final Guidelines document along with what we trust will be a wealth of resources provided by other stakeholders. Our members strongly rely on these resources when working with employers to establish safety and health management programs.
ANSI Z10 Occupational Health and Safety Management Systems - http://www.asse.org/ansiaihaasse-z10-2012-occupational-health-safety-management-systems/ansi/aiha/asse-z10-2012-occupational-health-and-safety-management-systems/
ISO 45001 Occupational Health and Safety Management Systems - http://www.iso.org/iso/iso45001.
ANSI A10.33-2011 Safety and Health Program Requirements for Multi-Employer Projects - http://www.asse.org/ansiasse-a1033-2011-safety-health-program-requirements-for-multi-employer-projects/ansiasse-a1033-2011-safety-health-program-requirements-for-multi-employer-projects/
ASSE Business of Safety Resource Center - http://www.asse.org/professionalaffairs/bosc/
ASSE Risk Assessment Institute http://www.oshrisk.org/ and the free video resources to help safety and health practitioners develop competencies in risk assessment and management at http://www.oshrisk.org/videos/
Safety Professionals Handbook - http://www.asse.org/the-safety-professionals-handbook-second-edition-two-volume-set/
ASSE Safety, Health and Environmental Body of Knowledge - http://www.safetybok.org/asses_body_of_knowledge/
Board of Certified Safety Professionals - http://www.bcsp.org/
American Board of Industrial Hygiene - http://www.abih.org/
NIOSH resources, including its Small Business Resource Guide - http://www.cdc.gov/niosh/topics/smbus/guide/guide-2.html; Elements of an Effective Safety and Health Program - http://www.cdc.gov/niosh/programs/wrt/pdfs/Example-Safety-Program.pdf; and research on the topic available generally at http://www.cdc.gov/niosh/.
Conclusion
ASSE represents 37,000 occupational safety and health professionals who see themselves as the leading stakeholders in advancing acceptance of safety and health management programs as the most important best practice to achieve significant workplace safety and health results. Safety and health management plans are what we do, who we are at our best, and how we help employers best protect workers’ lives.
ASSE and our members are grateful to OSHA for its work in revising and updating the guidelines. We hope these comments are useful, and we will not hesitate to continue to communicate our thoughts on the Guidelines as we look forward to final document. Likewise, we look forward to working alongside OSHA and other stakeholders in doing whatever we can to make sure as many employers as possible know and use these Guidelines.
Sincerely,
Michael Belcher, CSP
President
Looking for a reprint of this article?
From high-res PDFs to custom plaques, order your copy today!