From NSC Congress & Expo
Electrical safety: Improving your program
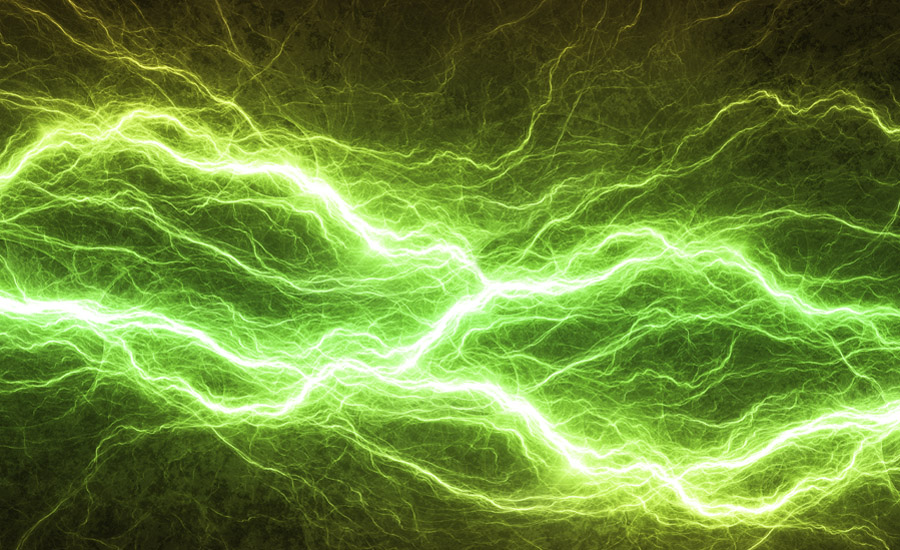
The results of an electrical industry study over 10 years with 120,000 workers showed that there are about 125 electrical injuries per year with 77 percent of them arc flash injuries, 21 percent permanent disabilities and 2.4 percent fatalities.
Hugh Hoagland, senior managing partner, eHazard and ArcWear, spoke about the importance of electrical safety Tuesday and shared his advice for improving safety programs and reducing injuries.
He said for overall safety, for every 300,000 at-risk behaviors, there are 300 recordable injuries and one fatality, however, 10 of those 300 are in the electrical industry with one fatality so the fatality rate is 1 in 10 recordable injuries versus one in 300 for overall safety.
The latest OSHA regulation 1910.269 states that when it comes to protection from flames and electric arcs, the employer must identify employees exposed, make a reasonable estimate of incident heat energy exposure, and ensure exposed employees wear PPE arc-rated to match or exceed energy estimate; do not wear clothing that could melt onto skin or ignite and continue to burn.
Electric arc protection requires FR clothing for incident energy exceeding 2.0 cal/cm2, protection for head and face, protection for hands and protection for feet (heavy work shoes or boots).
Hoagland said there are many arc-rated gloves that have no shock protection voltage rating. “Beware, these may only be used for limited activity such as LV switching and for equipment operation when no shock hazard exists,” he said.
What makes a person qualified?
The NFPA 70E standard defines it as a two-part process: “One who has demonstrated skills and knowledge related to the construction and operation of electrical equipment and installations and has received safety training to identity and avoid the hazards involved.” A person may be “task qualified,” qualified to perform a certain task or qualified to use certain equipment but not be low voltage qualified. Only the employer can determine if someone is qualified, Hoagland said.
Contractor responsibilities
- Inform employees of all potential hazards specific to the installation and require safe work practices be followed.
- Alert host employer to any unique hazards presented by contractor’s work.
- Inform host employer of any hazards encountered that host employer did not mention.
- Report measures taken to correct any violations of required safe work practices.
Document the meeting.
Maintenance reduces risk
Common maintenance standards require power circuit breakers be calibrated on an interval required by the manufacturer or every three years. Breaker maintenance and calibration are critical to arc flash protection. Maintenance, tests and inspections must be documented.
Hoagland mentioned that no PPE is required for normal operation if equipment is properly installed, maintained and doors and covers are closed and secured, and there is no evidence of impending failure. Signs to look for are evidence of excess heat, burning odor and unusual noise.
Looking for a reprint of this article?
From high-res PDFs to custom plaques, order your copy today!