Machine guard violations can cause serious injury
Consequences: amputations, lacerations, crushing injuries & death
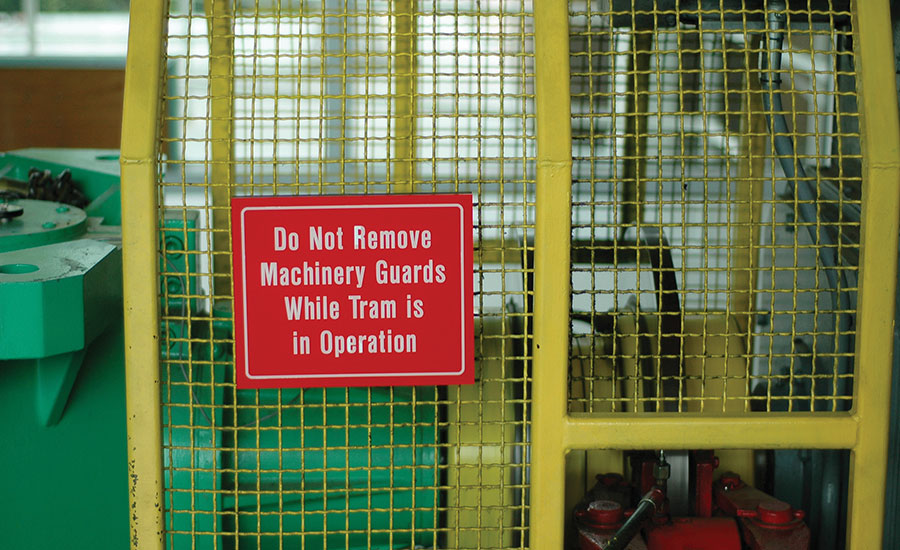
In fiscal year 2014, OSHA issued 2,396 citations and almost $7 million ($6,891,521)in penalties for violations of its machine guard standard (1910.212), making it the ninth-most violated standard in the time period.
The most-cited industries: machine shops – screw, nut and bolt manufacturing; architectural and structural metals manufacturing; and plastic product manufacturing. Other frequently-cited industries: fabricated metals manufacturing; wood products; printing; and motor vehicle parts manufacturing.
According to OSHA, workers who operate and maintain machinery suffer approximately 18,000 amputations, lacerations, crushing injuries, abrasions and more than 800 deaths per year.
The general requirement 1910.212 (a)(1) states that one or more methods of machine guarding must be used to protect operators and other employees from hazards including those created by point of operation, in-going nip points, rotating parts, flying chips and sparks.
Hazardous actions
Identifying hazards is the first step toward protecting workers. According to OSHA, the basic types of hazardous mechanical motions are:
• Rotating: Even smooth, slowly rotating shafts can grip clothing, and through skin contact, force an arm or hand into a dangerous position. Collars, couplings, cams, clutches, flywheels, shaft ends, spindles and horizontal or vertical shafting are examples of common hazardous rotating mechanisms.
• Reciprocating: This causes a back-and-forth or up-and-down action that can strike a worker or catch a worker between a moving and a stationary part.
• Transversing: Movement in a straight, continuous line; moving parts can catch or strike a worker in a pinch point or shear point.
The basic types of hazardous actions are:
• Cutting: Rotating, reciprocating or transverse motion, where finger, head and arm injuries can occur and where flying chips and scrap material can strike a worker’s eyes or face. Cutting actions are dangerous with bandsaws, circular saws and boring or drilling machines.
• Punching: When power is applied to a slide for the purpose of blanking, drawing or stamping metal. The danger occurs where stock is inserted, held and withdrawn by hand as with power presses.
• Shearing: Applying power to a shear or knife to trim or shear materials. The danger is where stock is inserted, held and withdrawn as with hydraulically or pneumatically powered shears.
• Bending: Power is applied to a slide to draw or stamp metal or other material. This is a threat where stock is inserted, held and withdrawn, with equipment such as power presses.
Safeguards
• Prevent contact: The safeguard must prevent hands, arms or any other part of a worker’s body from making contact with dangerous moving parts.
• Be secure: Workers should not be able to easily remove or tamper with the safeguard.
• Protect from falling objects: The safeguard should ensure that no objects can fall into moving parts.
• Create no new hazards: A safeguard defeats its purpose if it creates a hazard such as a shear point, a jagged edge or an unfinished surface.
• Create no interference: Any safeguard that impedes a worker from performing a job quickly and comfortably might soon be bypassed or disregarded.
Looking for a reprint of this article?
From high-res PDFs to custom plaques, order your copy today!