Are you ready to handle emergencies?
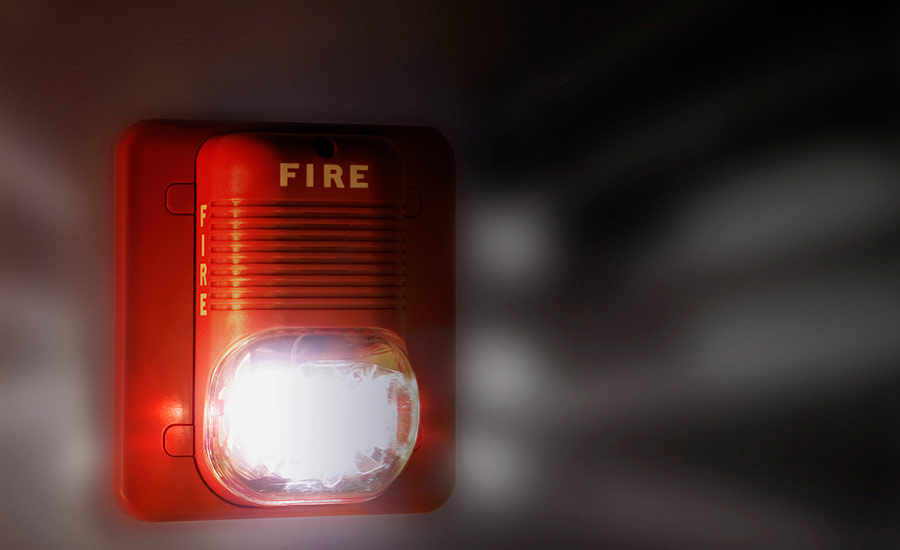
U.S. fire departments receive an estimated 42,800 reports of fires from industrial and manufacturing facilities each year, according to the NFPA. Fire prevention and emergency action plans are two tools to ensure employees know what to do before and after a fire alarm sounds.
Fire hazards
Fire hazards aren’t limited to open flames and vapors from flammable liquids. They also include hot surfaces, welding sparks, processes that create friction and many others. A leading cause of workplace fire risk, according to OSHA, is electrical hazards, which include things like improper ground connections, frayed wire insulation, misuse of extension cords and overloaded circuits.
Production, handling and storage areas typically come to mind when fire hazards are mentioned, but office areas can be prone to fire problems as well. Recyclables are sometimes permitted to accumulate to unsafe levels, office areas become cluttered, space heaters may be overused, and office equipment such as computer mainframes and copiers that aren’t kept in climate controlled environments or provided adequate cooling space are among the more common office fire hazards.
Even the lack of a smoking policy can be a fire hazard. In the absence of designated smoking areas and/or dedicated cigarette butt receptacles, people are more likely to flick cigarette butts into mulch or landscaped areas where the butts can smolder and catch exterior building siding materials on fire.
Fire prevention plans
By identifying fire hazards in a workplace and establishing safe storage and handling procedures that prevent fires from occurring, emergencies that impact worker safety and loss of company property can be avoided.
Several OSHA regulations require facilities with certain types of hazardous chemicals and/or hazardous processes to have written fire prevention plans that identify fire hazards and outline safe procedures for storing and handling them. When required, these plans must also list the names or job titles of the person(s) responsible for controlling fuel source hazards, as well as who will maintain equipment to prevent ignition sources and fires [29 CFR 1910.39].
Emergency action plans
Fires are just one type of emergency that facilities must be prepared to handle. Emergency action plans address workplace emergencies and detail the processes and procedures (actions) that will be taken to safely evacuate facilities and account for employees, visitors and contractors. In addition to establishing emergency escape routes, plans must also list procedures for employees who will shut down equipment before evacuating the facility, or perform other functions such as medical or rescue operations.
Because a variety of alarms may be used in a facility to indicate different types of emergencies, plans need to outline how employees will be trained to recognize different alarms, as well as the method for reporting emergencies. For example: should an employee pull an alarm, alert a supervisor, dial an in-house emergency number or call 9-1-1?
Accountability for all employees is a key provision in Emergency Action Plans that is sometimes overlooked, is often under-planned for and is rarely drilled. First responders are taught that life safety is their first priority. If employees cannot be accounted for after an evacuation, time will be spent searching for anyone who is missing. This puts responders at risk and can delay other response actions. Establishing clear plans for accountability and detailing the names or job titles of the people who will be responsible for these activities promotes safety for both employees and responders.
Emergency action plans and fire protection plans should both be coordinated with local fire departments, and where appropriate, local or county hazmat teams. Doing this helps these outside responders better understand the specific hazards and needs of the facility. It also helps set realistic expectations for both parties.
Training
Fire protection and emergency action plans should be available for employees to review. However, because most people don’t take the time to review them, regular training is necessary to teach employees about the alarm systems used in the facility as well as emergency notification protocols. Safe storage, use and handling of flammable liquids and safe procedures for working around other fire hazards should also be taught, as well as good housekeeping and emergency shutdown procedures that help minimize fire dangers.
In addition to knowing the primary evacuation route, employees should also be aware of at least one other alternate evacuation route from their work area as well as the meeting area to go to so that managers, supervisors or other designated personnel can account for everyone to ensure that no one has been left in a building. If fire extinguishers are present, employees must be trained on how to use them properly and under what conditions they should be used.
A good way to ensure that training has been effective is to host regular drills. Although they do take time away from production and other work activities, drills help everyone become more comfortable with their roles and responsibilities. They also help identify any weaknesses so that plan improvements can be made and training can be revised to improve safety.
The NFPA 101 Fire Code establishes guidelines for the frequency of drills. According to the standard, drills should be frequent enough that everyone is familiar with procedures, and their actions become routine. [NFPA 1: Fire Code, 10.6.2]. Further, the NFPA Life Safety Code suggests goals for evacuation drills, which include recognizing alarms, evacuating according to the established plan and reporting to an assembly area. The code emphasizes that the goal of drills is “orderly evacuation rather than speed.”
Looking for a reprint of this article?
From high-res PDFs to custom plaques, order your copy today!