Lockout/Tagout and machine guarding
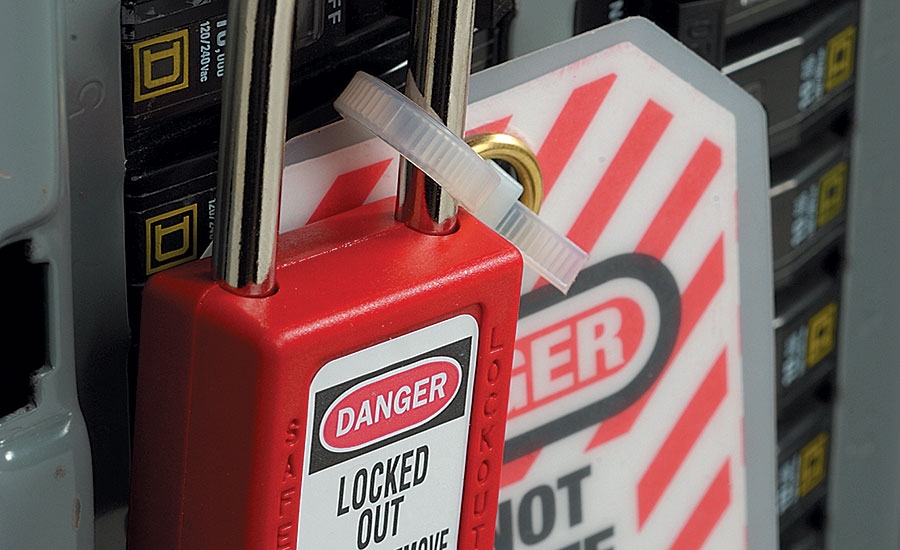
Scope and purpose
To better understand this relationship, let’s first explore the scope and purpose of each standard. The LO/TO standard covers the servicing and maintenance of machines and equipment in the unexpected energization or start-up of machines or equipment, or release of stored energy that could cause injury to employees. The purpose of the LO/TO standard is to control the energy that may be present during the servicing and/or maintenance of machines and equipment to avoid injury through the use of established procedures and techniques.
The machine guarding standard covers any machine where machine parts, functions or processes may present hazards created by ingoing nip points, motions (rotating, reciprocating, transversing), actions (cutting, punching, shearing, bending), flying chips and sparks resulting in injury. Its purpose is to protect the machine operator and other employees in the work area from these hazards by use of a type of safeguard technique compliant with the machine guarding standard.
Safeguards fall into five main categories: guards, devices, safety controls, gates, and location/distance.
Safeguards must meet these minimum general requirements:
1. Prevent contact: The safeguard must prevent hands, arms or any other part of a worker’s body from making contact with dangerous moving parts.
2. Be secure: Workers should not be able to easily remove or tamper with the safeguard. Guards and safety devices should be made of durable materials that will withstand normal use. They must be firmly secured to the machine where possible or secured elsewhere if attachment to the machine is not possible.
3. Protect from falling objects: The safeguard should ensure that no objects can fall into moving parts.
4. Create no new hazards: A safeguard defeats its purpose if it creates a hazard such as a shear point, a jagged edge or an unfinished surface.
5. Create no interference: Any safeguard that impedes a worker from performing a job quickly and comfortably might soon be bypassed or disregarded. Proper safeguarding can actually enhance efficiency because it relieves a worker’s injury apprehensions.
6. Allow safe lubrication: If possible, one should be able to lubricate the machine without removing the safeguard. Locating oil reservoirs outside the guard, with a line leading to the lubrication point, will reduce the need for the operator or maintenance worker to enter the hazardous area.
Now that we know the scope and purpose of each standard and what a safeguard should do, we need to know when a standard and safeguard may apply during an activity being performed. OSHA has identified two key activities that are performed. The first activity is called normal production. This is defined as any utilization of a machine or equipment to perform its intended purpose. The second activity is call servicing and/or maintenance. This is defined as any action that is necessary to prepare or maintain a machine or equipment such as: installing, setting up, inspecting, adjusting, repairing, replacing, constructing, modifying, lubricating, cleaning, unjamming, or pretty much any activity outside the definition of normal production.
Servicing and/or maintenance
As a general principle, the LO/TO standard does not apply to servicing and/or maintenance activities when employees are not exposed to hazardous energy. OSHA has identified six circumstances where employees are not exposed to hazardous energy:
1. Complying with LO/TO 29 CFR 1910.147;
2. Complying with the minor servicing exception to the LO/TO standard contained in the note found in 29 CFR 1910.147(a)(2)(ii)(B);
3. Utilizing the cord and plug connected equipment or hot tap exemptions found in 29 CFR 1910.147(2)(iii)(A) and (B) respectively;
4. Effective machine guarding, in compliance with Subpart O, that eliminates or prevents employee exposure from the hazardous energy associated with the machines or equipment;
5. Final actions granting LO/TO standard variances or;
6. Other applicable portions of Part 1910 that prevent employee exposure to hazardous energy.
As listed in number four, an employer may avoid the requirements of the LO/TO standard for servicing and/or maintenance activities if they eliminate exposure to hazards by using safeguarding techniques compliant with OSHA’s machine guarding standard. However, any time a guard is removed or bypassed, compliance with LO/TO is again required. This would include practices such as reaching around guards while equipment is energized. This practice could expose the operator to hazardous mechanical energy. Rule of thumb dictates under no circumstances is any part of an employee’s body ever permitted to be exposed within a hazardous area, such as the point-of-operation or in-going nip point area, during servicing and/or maintenance activities while the machine is running or energized.
Machine guarding requirements complement the requirements of the LO/TO standard. During the promulgation of the LO/TO standard, OSHA recognized this relationship with machine guarding and identified it in the LO/TO compliance directive.
LO/TO compliance directive
OSHA Instruction CPL02-00-147 became effective February 11, 2008. It is not a standard, regulation or any other type of substantive rule that can be enforced. It serves as a guide to OSHA compliance officers on how to enforce the LO/TO rule and related standards in a consistent and uniform fashion. This directive provides insight into OSHA’s interpretations of the LO/TO standard and applicable standards. It is a must read for anyone responsible for administering a LO/TO program in their workplace. It provides great examples of how LO/TO and machine guarding rules relate to each other.
Examples
The following two examples from OSHA’s LO/TO compliance directive illustrate the complementary relationship between the LO/TO standard and the machine guarding standard:
Example 1 (General): An employer who requires employees to perform servicing and/or maintenance while a machine or equipment is operating in the production mode must provide employee protection. Operations, such as lubricating, draining sumps, servicing filters, making simple adjustments, and inspecting for leaks and/or malfunction, are examples of routine operations that often can be accomplished with effective production-mode machine guarding as addressed in Subpart O. The LOTO standard does not apply if employee exposure to hazardous energy is eliminated through compliance with the Subpart O, machine guarding, requirements.
In contrast, the replacement of machine or process equipment components such as valves, gauges, linkages or support structure is not considered a normal routine maintenance function that can be safely accomplished during machine or equipment operation. Such maintenance requires LO/TO.
Example 2 (Specific): In a machine shop, a milling machine operator must adjust the flow of coolant oil to parts being milled while the cutting tool is in operation. This operation, which is part of the normal production process for the machine, is covered by the machine guarding requirements, which prevent employee contact with nip points and other points of operation. However, if it becomes necessary to perform an adjustment which requires the operator to bypass a guard or to place any part of his/her body in an area where work is performed on the material or where a danger zone exists during the machine’s operating cycle, the LO/TO standard would then apply.
Summary
Employee protection from hazardous energy during normal production activities is generally accomplished by compliance with applicable machine guarding standards found in Subpart O. If maintenance and/or servicing activities take place during normal production activities, and the operator is required to remove or bypass machine guarding required by subpart O, or place any part of their body in an area where unexpected startup of the machine or equipment may cause injury, the LO/TO standard would apply. If unsure about a maintenance and/or service activity falling under normal production conditions, always play it safe and lock it out.
Looking for a reprint of this article?
From high-res PDFs to custom plaques, order your copy today!