Work strain & heat stress
Make sure clothing cools down workers
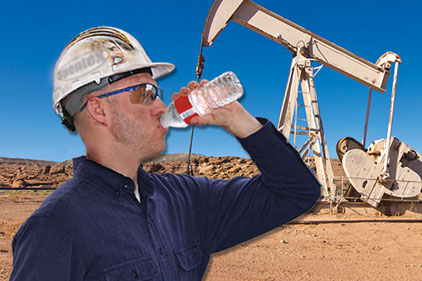
Heat stress dangers
For years cotton fabric has been the standard in comfort, but untreated cotton garments offer no thermal, flame or arc protection. Cotton fabric loves moisture and will hold onto it, resulting in soaked, heavy and clammy garments. There are numerous flame-resistant (FR) PPE garments in today’s market that will provide necessary protection, but without moisture transport, the body is not ventilated; this increases the risk of heat stress dangers.
Heat stress danger from PPE has been a prominent topic of discussion for many years. Dr. Thomas Bernard, an expert on the physical stress faced by industrial workers, is quoted as saying:
Among the workplaces with which I am most familiar, clearly high environmental heat and clothing requirements are the biggest problems. The environmental heat comes in the form of high workplace temperatures and humidity, and on occasion significant amounts of radiant heat. A person’s capacity for balancing the heat stress by evaporative cooling is truly remarkable. When special purpose clothing is worn to prevent burns or chemical contamination of the skin, the rate of evaporative cooling is greatly reduced.
Hot work environments combined with exertion are especially dangerous when coupled with PPE that encapsulates sweat rather than allowing it to dissipate and provide evaporative cooling. Numerous studies have documented that strenuous activities where protective garments are worn can lead to near maximum heart rates and dangerously raised body core temperatures. When a person engages in elevated levels of physical activity, the body increases the metabolic rate and thus the rate of heat production. The body must then use additional resources to remove the additional heat produced in order to keep the internal temperature at a healthy level.
New technologies
Fortunately, there are new technologies utilizing proprietary fiber combinations and fabrics that now address heat stress concerns while providing outstanding thermal, flame and arc protection in a single, lightweight and breathable layer. These fabrics can also be inherently flame-resistant, durable and machine washable. Generally, most fabrics are manufactured in both twill and knit blends, meaning garments made from these technologically-advanced fabrics provide the wearer with proven inner and outer layer protection.
In colder months, a layered FR PPE garment system can be worn to provide insulation against the cold temperatures and wind. Layering can result in bulky garments systems that are heavy and restrict heat dissipation leading to heat strokes, heart attacks and death.
Most of today’s FR garment systems include wearing base layers to provide additional warmth; this additional layer also adds a higher protection against thermal, flame and arc injury. If an FR PPE garment possesses insulating properties but no moisture management properties, heat stress dangers are further compounded. Layering of moisture-wicking garments not only creates a layer of air between the garments, which keeps the wearer warm in the winter, but also allows moisture transport. Utilizing the correct base layer will wick perspiration away from the body to the outer layer that will then release it into the environment; this will keep a body dry, and therefore warmer, in the winter months.
Verification testing
When choosing FR garments that need to provide protection as well as wear comfortably, it is important that the supplier can provide verification that the fabric used to construct their garment truly does allow the release of body heat and moisture into the environment.
One such verification test is ASTM F1868, which measures total heat loss (THL). The THL value is useful because it represents the highest possible amount of heat that can be transferred through a material system for a given set of environmental conditions without active cooling or ventilation. THL measurements per ASTM F1868 are required by several National Fire Protection Association (NFPA) standards: NFPA 1951, NFPA 1977, NFPA 1994 and NFPA 1999. High THL values are difficult to achieve if a fabric does not allow heat and moisture to escape into the environment, but they are even more difficult to achieve if the garment system consists of multiple layers. Some of the new technologies and fiber combinations can provide THL values above and beyond the minimum required THL values, as both twill and knits.
To get an idea of a full garment’s moisture management properties, verification testing per ASTM F2370 can be performed. ASTM F2370 testing is performed on a sweating thermal manikin and is the only standard that measures the evaporative resistance properties of garment ensembles; the higher the evaporative resistance value, the less permeable the garment is to moisture transport. Low evaporative resistance values are generally associated with garment comfort. Thermal manikins provide useful and valuable complements to direct trials with human subjects, as they simulate the physical shape and size of a typical man covered with a “skin” which then “sweats” enough to keep the “skin” saturated. Thermal manikins produce relevant, reliable and accurate values for a whole body; these values help determine the thermal properties of garments, predict human responses to extreme conditions and simulate thermal responses in humans.
Protection plus comfort
More work is currently being done to demonstrate that new fabric technology exists within the PPE arena that can provide thermal, flame and arc protection while mitigating skin temperature rise, regardless of how tough or hot the environment may be.
Looking for a reprint of this article?
From high-res PDFs to custom plaques, order your copy today!